微物理发泡注塑成型:实现最大化的减重与尺寸稳定性
2024-11-13 11:29:57
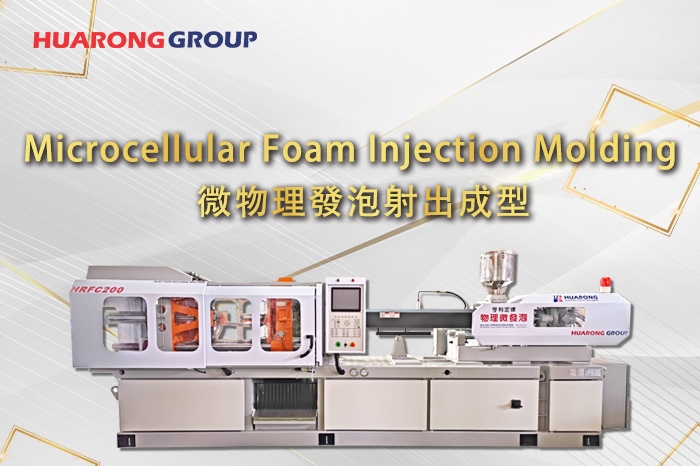
在当今迅速发展的制造环境中,对于可持续发展与长期增长的关注比以往任何时候都更加强烈,环境、社会和治理(ESG)的考量正推动创新。 减少塑料材料的使用不仅是一种节约成本的措施,更是企业在这个注重环保的未来中,追求长远成功的关键策略之一。 微物理发泡射出成型提供一个先进的解决方案,使制造商能够在保持或提升产品强度与性能的同时,减少材料的使用。
微物理发泡射出成型是将气体(例如氮气或二氧化碳)在高压下引入聚合物熔体中,气体均匀溶解于材料中,形成过饱和的聚合物-气体混合物。 当材料被射入模具时,压力急剧下降,气体膨胀并在聚合物内形成微小的气泡。 这个可控的发泡过程使最终产品在保持机械完整性的同时,达到降低密度的效果。
延伸阅读:微物理发泡射出成型技术
微物理发泡注塑成型的核心特点
由于该技术在聚合物内形成微细气泡,与传统注塑成型相比,它具有几个主要特点:
- 重量与密度降低(轻量化零件):主要优势是能在不影响机械强度的情况下,使重量降低15%-20%。
- 降低材料成本:通过减少每个零件所需的塑料量,制造商可以大幅节省原料成本。
- 尺寸稳定性:引入微气泡后,产品具有出色的尺寸稳定性。
- 缩短生产周期:产品的均匀气泡结构取消保压阶段,缩短生产时间,加快生产周期。
- 环保效益(可持续性与回收):此过程通过减少材料用量和缩短生产周期降低能源消耗,较传统成型工艺更环保。 此外与化学发泡方法不同,微物理发泡属于物理发泡,不会留下有害残留物,因此产品更环保且适合回收再利用。
- 降低锁模力需求:发泡过程使得所需的锁模力低于传统射出成型,允许制造商在较小的机台上生产较大的零件,进一步降低成本。
- 提升制程效率:由于生产周期缩短、材料节省以及能使用较小吨位机台,微物理发泡射出成型大幅提升生产效率与产能。
- 减少模具磨损:微物理发泡的低内压减少模具磨损,延长模具的使用寿命,使得每次生产的运行时间更长,降低翻新或更换模具的频率。
微物理发泡射出成型与传统射出成型的流程相似,但引进额外的步骤来提高产品性能,特别是在减重与材料效率方面。 以下是微物理发泡成型与传统方法的比较,并重点介绍该技术的特有要素:
传统注塑成型的延伸阅读:塑料注塑成型流程为何? 注塑机制程的6个步骤
步骤 1:锁模
该过程始于锁模,模具的两半借由锁模单元紧紧合在一起,以确保在射出阶段模具保持闭合。 与传统射出成型的不同之处在于,微物理发泡成型所需的锁模力远低于传统方法,这是由于发泡作用减少内部压力,进一步节约能源,并且允许在较小的机台上生产较大的零件,从而降低生产成本。
步骤 2:气体溶解的注射
在传统注塑成型中,塑料颗粒或胶粒会在高压下融化并注入模腔,而微物理发泡射出成型则会在注射阶段向熔融塑料中引入超临界气体,如氮气或二氧化碳。 这个过程称为气体溶解,气体均匀地溶解于聚合物熔体中,降低材料的密度,从而制造出轻量但坚固的零件。
步骤 3:成核与取消保压
在传统注塑成型中,保压阶段至关重要,对模具内的空间继续加压,用来维持模具中的压力,确保模具腔体均匀填充并防止材料回流。 由于需要持续的压力来保持保压,这一阶段通常会导致生产周期延长并增加能源消耗。 然而在微细孔泡沫注塑过程中,材料内部均匀微泡的形成消除保压阶段的需求,因此不再需要持续加压来填补模具腔体中的空隙,这减少能源密集型步骤的改进,有助于在注塑成型过程中降低能源消耗。
步骤 4:冷却与气泡成长
当塑料注入模腔后,塑料开始冷却。 微物理发泡射出成型中,形成的气泡在冷却时会均匀膨胀,从而降低零件的整体密度,并保持结构完整性。 由于气泡的存在,冷却时间可能会比传统成型略短,进一步提升生产效率。
步骤 5:开模
塑料冷却并固化后,模具会如同传统成型一样打开,锁模单元松开,模具分离,展示新成型的零件。 微物理发泡零件密度较低,与传统实心零件相比,材料收缩较少,从而达到更好的尺寸稳定性,并减少成型后的缺陷。
步骤 6:顶出
在最后一步中,固化的零件从模腔中顶出,这一过程与传统制程类似,顶出针会将零件从模具中推出。 不同的是,微物理发泡零件由于材料密度降低且具有发泡特性,通常需要的顶出力较小,使顶出过程更加顺畅,缺陷较少。 尽管仍可能需要修剪多余材料,但由于其原材料利用效率高,微物理发泡零件的材料浪费通常较少。
微物理发泡注塑成型的效率依赖于几个关键组件:
- 气体供应(氮气或二氧化碳):气体供应是创造微胞结构的重要组件,通常使用氮气或二氧化碳等惰性气体。
- 气体驱动源:这个组件能够以控制压力精确地将气体注入聚合物熔体,确保在塑化阶段内气体均匀且稳定地溶解于聚合物中,从而形成均匀的微胞结构。
- 专用微物理发泡料管组与止逆射嘴:此专门设计的料管组针对微物理发泡工艺进行优化,改善气体在聚合物中的混合与分散。 指逆射嘴是关键组件,防止气体在射出过程中过早逃逸,确保发泡的完整性。 这些专业设备可控制聚合物与气体混合物在射入模具时的膨胀,确保零件内部的泡孔结构均匀且稳定。
物理发泡射出成型具有高度的灵活性,广泛应用于各个行业,包括:
- 汽车产业:微物理发泡射出成型适合生产轻量化且高性能的内饰件到引擎零组件,因为减轻零件重量能直接提升燃油效率。
- 消费品产业:这种材料常用于消费电子产品中,用来制造像是智能手机、笔记本电脑、平板电脑等设备的轻量化且坚固的外壳。 它出色的尺寸稳定性确保零件完美契合,而轻量特性则提升这些设备的便携性。
- 包装行业:通过减少每个包装所需的塑料量,制造商能降低成本并生产具备环保特性的包装解决方案,同时不牺牲质量。
除微物理发泡成型外,还有哪些其他的发泡注塑成型方式?
发泡射出成型可以根据在聚合物内产生泡沫的方式进行分类,主要分为三种方法:物理发泡、化学发泡和结构发泡。 本文讨论的微物理发泡成型属于物理发泡,而其他方法也广泛应用。
项目 | 物理发泡 | 化学发泡 | 结构发泡成型 |
---|---|---|---|
过程 | 将惰性气体或低沸点液体溶解于聚合物熔体中形成泡沫 | 化学发泡剂在加热时分解,释放气体产生泡沫 | 同时使用物理或化学发泡剂来形成微胞结构 |
机械强度 | 中等; 依赖气体分布的均匀性 | 适合复杂形状; 强度依泡沫密度而异 | 高; 结合发泡与厚壁结构,提高整体耐用性 |
使用范围(应用) | 轻量化汽车零件、包装、保温材料 | 复杂消费品、保温材料、电子产品 | 大型零件,如面板、汽车、重工业建筑产品 |
优点 | 轻量化,气泡均匀,材料使用量低 | 适合复杂设计,高密度潜力 | 适合大型复杂结构,模具成本低,可使用多腔模具 |
缺点 | 需要精确控制压力与气体 | 发泡剂残留可能影响质量 | 生产周期较长,小批量生产成本较高,适合小批量 |
微物理发泡注塑成型无疑是未来轻量化与高强度制造技术的发展趋势。 它具有减少材料使用、缩短生产周期和提升尺寸稳定性等多重优势,将彻底改变多个行业。
联系我们
欲解更多关于我们的微物理发泡射出成型技术如何助您下一个项目成功,华嵘机械作为一家专业的注塑成型机制造商,不仅提供全系列射出成型机,还为客户提供可行的解决方案,携手共创未来
- 集团名称: 华嵘集团
- 品牌: 华嵘、煜达、南嵘
- 服务项目: 注塑机、立式射出机、成型设备取出装置
- 服务电话: (06)7956777
- 集团总部: 台南市西港区庆安里中州21之6号
- 官方网站: https://www.huarong.com.tw/
前一则新闻:华嵘荣获2025年台湾精品奖,展现创新注塑技术
下一则新闻:PET瓶胚注塑成型机:实现高产能与高效率的制造