PVC注塑成型:工艺、挑战与最佳实践
2025-02-27 15:22:01
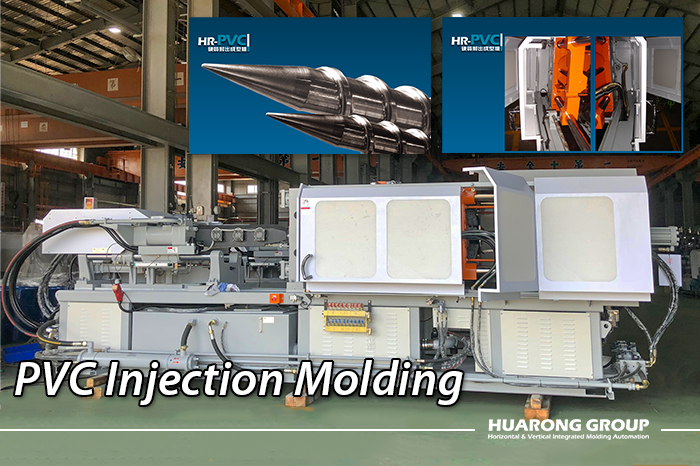
PVC注塑成型是一种广泛应用的制造工艺,能够以卓越的精度生产高质量、耐用的塑料零件。PVC因其多功能性、成本效益及化学抗性而受到青睐。然而,与其他塑料相比,PVC的加工需要特殊技术及严格控制,以确保产品质量、机械寿命及安全性。本文将深入探讨PVC注塑成型,包括材料特性、成型工艺、设计准则及最佳实践。
PVC(聚氯乙烯)是一种合成热塑性聚合物,主要分为刚性PVC(RPVC)和软性PVC(FPVC)两种形式。PVC由氯乙烯单体(VCM)、增塑剂、稳定剂及其他添加剂组成,这些成分影响其机械及热性能。与其他塑料不同,PVC因其低热稳定性及潜在的降解风险,需要严格的加工控制。
PVC类型:
- 刚性PVC(RPVC): 以其硬度和强度著称,广泛应用于建筑材料,如管材和窗框。
- 软性PVC(FPVC): 添加增塑剂后,材料变得更柔软且具可塑性,常用于医疗管材、电缆绝缘层及各类消费品。
延伸阅读:10 个常见注塑成型塑料及其特性
PVC的关键特性
PVC的普及归因于其多种优异特性:
- 化学抗性: 对酸、碱及大多数有机溶剂具有优异的抗性,非常适合化学处理应用。
- 电绝缘性: 具备优异的绝缘特性,被广泛应用于电子与电气领域。
- 阻燃性: 天然具有耐燃性且自熄特性,可提升防火应用的安全性。
- 耐久性: 拥有高抗拉强度与抗冲击性,确保在严苛环境中的使用寿命。
- 低吸湿性: 即使在潮湿环境中,也能保持尺寸稳定及机械性能。
材料性能比较
性质 | 刚性PVC(RPVC) | 软性PVC(FPVC) |
---|---|---|
密度(g/cm³) | 1.35 - 1.45 | 1.1 - 1.3 |
拉伸强度(MPa) | 45 - 60 | 10 - 25 |
断裂伸长率(%) | 10 - 40 | 100 - 400 |
弯曲模量(GPa) | 2.4 - 4.1 | 0.01 - 0.1 |
介电常数 | 3.0 - 3.8 | 3.2 - 4.0 |
(注:具体数值可能因PVC配方及添加剂不同而有所变化。)
PVC注塑成型应用领域
PVC注塑成型广泛应用于各行业,包括:
- 建筑: 生产耐用且耐候的管材、接头及外墙覆层材料。
- 医疗: 制造具有生物相容性和可消毒性的软管、点滴袋及其他医疗器材。
- 汽车: 用于内饰件、仪表板及密封条,因PVC的美观性及耐用性而受到青睐。
- 消费品: 用于制造鞋类、玩具及各类家用产品,具有成本效益及多用途性。
相关文章:成功案例:最适合您的PVC塑胶管件注塑机
PVC注塑成型过程遵循一系列关键步骤,确保将原料转化为精确且一致的成品。
1. 材料准备
PVC树脂需与稳定剂、增塑剂及润滑剂混合,以改善流动性及热稳定性。预干燥(60°C 2-3小时)可防止因水分引起的气泡或烧焦痕迹。
2. 熔融与塑化
PVC的加工温度范围较窄,过热会导致降解。维持熔融温度在170°C至190°C之间,可确保流动性而不降解。
3. 注塑
当PVC熔融后,在受控的压力及速度下注入模具腔内。精确控制可确保无空洞填充,并最小化残余应力。
4. 冷却
冷却过程至关重要,以防止变形及收缩。高效的模具冷却系统可确保均匀冷却并保持尺寸稳定。
5. 脱模
冷却后,固化的PVC零件从模具中取出。可使用防粘涂层或脱模剂,以防止粘附问题。
参数 | 建议设置 |
---|---|
熔融温度 | 170°C – 190°C |
注塑压力 | 80 – 120 MPa (800 – 1200 bar) |
注塑速度 | 中等至高速 |
模具温度 | 20°C – 50°C |
冷却时间 | 20 – 70秒 |
尽管PVC具有出色的多功能性,但对其进行成型需要特殊的考虑。以下是一些常见的挑战:
1. 热敏感性
PVC在高温下会分解,释放盐酸(HCl),可能腐蚀机械元件并影响成品质量。防止降解的方法包括:
- 维持加工温度在 170°C至190°C。
- 使用温控料筒并避免过长的停留时间。
2. 高粘度
PVC熔融后的粘度较高,填充模具较困难。解决方案:
- 使用 80 – 120 MPa 的注塑压力。
- 确保模具设计具有足够的排气孔。
3. 腐蚀问题
PVC会释放酸性气体,导致模具及机械元件腐蚀。建议:
- 使用不锈钢或镀铬模具。
- 定期维护及润滑机械部件。
4. 吸湿性
水分可能导致成品产生气泡或空洞。解决方案:
- 预干燥 PVC树脂(60°C 2-3小时)。
设计PVC注塑成型产品时,需要考虑多个因素,以提升可制造性与产品性能:
- 均匀壁厚: 保持一致的壁厚可减少内部应力,降低变形及缩痕风险。
- 脱模斜角: 设计适当的脱模角度(通常1° 至 2°),可帮助零件顺利脱模,减少模具损耗与生产困难。
- 圆角处理: 避免尖锐直角,适当添加圆角(R角)可减少应力集中,并改善材料流动性,提高产品质量。
- 孔洞设计: 确保孔洞的深径比不超过2:1,以防止注塑成型时产生缺陷,并保持零件的结构完整性。
模具设计对PVC注塑成型零件的质量具有关键影响:
- 材料选择: 应使用耐腐蚀材料(如 H13、S136 不锈钢或镀铬钢),以延长模具寿命并减少腐蚀问题。
- 冷却通道: 应设计符合模具形状的冷却通道(Conformal Cooling),以确保均匀冷却并提升生产效率。
- 通气设计: 适当的排气设计能有效防止气体滞留,降低烧焦痕迹或气泡等缺陷的发生率。
遵循业界最佳实践可提升生产效率及产品质量:
1. 材料处理与准备
- 适当存放PVC树脂,防止污染或受潮。
- 成型前预干燥(60°C 2-3小时),以降低水分影响,提高成品一致性。
2. 机械选择与维护
推荐产品:PVC注塑机 – PVC系列
3. 优化加工参数
- 背压: 维持在 3-10 bar(50-150 psi),确保塑化均匀,防止材料降解。
- 螺杆转速: 建议设定 20-60 RPM,确保均匀熔融,避免过度剪切加热。
了解可能出现的缺陷及相应解决方案,有助于提升成品质量:
1. 烧焦痕迹
- 成因: 注塑速度过快或气体滞留,导致“柴油效应”(Diesel Effect)产生高温燃烧痕迹。
- 解决方案:
- 降低注塑速度
- 优化模具排气设计,确保气体顺利排出
2. 变形
- 成因: 冷却不均匀或壁厚不一致,导致材料内应力分布不均。
- 解决方案:
- 设计均匀壁厚的零件,降低内应力
- 优化冷却通道配置,提高冷却效率
3. 变色
- 成因: 熔融温度过高或材料在料筒内停留时间过长,导致热降解。
- 解决方案:
- 适当降低料筒温度
- 减少材料在料筒内的停留时间
PVC注塑成型是一项技术复杂但具有高回报的制造工艺,在塑料零件生产中扮演关键角色。通过深入理解材料特性、严格控制加工参数,并遵循最佳模具设计及机械维护实践,制造商可显著提高产品质量及生产效率,确保在市场竞争中保持优势。
- 集团名称: 华嵘集团
- 品牌: 华嵘、煜达、南嵘
- 服务项目: 注塑机、立式射出机、成型设备取出装置
- 服务电话: (06)7956777
- 集团总部: 台南市西港区庆安里中州21之6号
- 官方网站: https://www.huarong.com.tw/