Understanding Injection Molding Machine Types: Advantages and Disadvantages of 7 Popular Models
2024-08-22 13:10:41
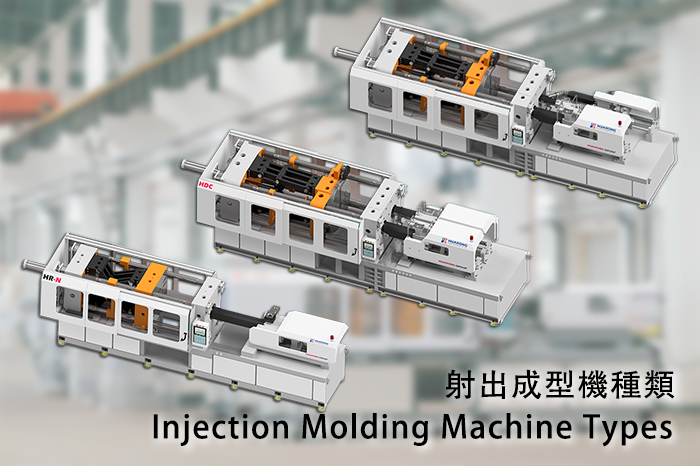
Injection molding machines are essential for mass-producing high-precision parts across the automotive, electronics, medical devices, and consumer goods industries. As industry demands evolve, so does the technology behind these machines, resulting in a range of machines suited to various production needs. This article explores the different types of injection molding machines, including their advantages and disadvantages, to help you choose the best option for your manufacturing requirements.
Injection molding machines are engineered for diverse manufacturing needs, with each type tailored to specific applications. By understanding the types of injection molding machines—classified by power drive, clamping style, and injection molding materials compatibility—you can optimize production processes, minimize waste, and enhance product quality.
Power Drive Classification: Hydraulic, All-Electric, and Hybrid Injection Molding Machines
Injection molding machines can be classified based on their power drive mechanisms:
- Hydraulic Injection Molding Machine: Powered by hydraulic cylinders, offering high clamping force.
- All-Electric Injection Molding Machine: Uses servo motors for precision and energy efficiency.
- Hybrid/Servo Injection Molding Machine: Combines features of both hydraulic and electric machines for balanced performance.
Clamping Style Classification: Horizontal, Vertical, Toggle, and Two-Platen Machines
The clamping style of an injection molding machine influences its footprint, production speed, and suitability for various applications:
- Horizontal Injection Molding Machine: Widely used, with horizontal operation.
- Vertical Injection Molding Machine: Ideal for insert molding and overmolding.
- Toggle-Type Injection Molding Machine: Uses toggle mechanisms for consistent clamping force.
- Two-Platen Injection Molding Machine: Compact, designed for large-part injection molding production.
Material Classification: Thermoplastics, Thermosets, and More
Injection molding machines also vary by material compatibility:
- Thermoplastic Injection Molding Machine: Reusable and versatile with melting and cooling cycles.
- Thermoset Injection Molding Machine: Suited for high-heat applications with irreversible chemical changes.
- Multi-Material Injection Molding Machine: Allows the production of complex parts with multiple materials.
Power drive refers to the machine’s mechanism for generating power and controlling injection. Let’s explore each type, along with their advantages and disadvantages.
Hydraulic Injection Molding Machines
Hydraulic injection molding machines are the most traditional type, offering reliability and power through hydraulic cylinders.
Advantages
- Cost-Effective: Lower initial costs make hydraulic machines affordable.
- Durability: Hydraulic components withstand wear, ensuring longevity.
- High Clamping Force: Suitable for molding large or complex parts.
- Simple Operation: Easy to operate and maintain.
Disadvantages
- High Power Consumption: Energy costs are higher than with electric machines.
- Limited Precision Control: Less precise than electric systems.
- Warm-Up Required: Needs a warm-up period, impacting efficiency.
Electric Injection Molding Machines
Electric machines have become popular due to their energy efficiency and precision.
Advantages
- Energy Efficiency: Power is used only when necessary, minimizing waste.
- Fast Cycle Times: Electric controls allow for quick, repeatable processes.
- Clean and Quiet: Suitable for cleanrooms; produces minimal noise.
- High Precision: Excellent for high-accuracy applications.
Disadvantages
- Higher Initial Costs: More expensive due to advanced servo motors.
- Clamping Force Limitations: Less effective for very large parts.
- Maintenance Expertise: Requires specialized knowledge and upkeep.
Hybrid/Servo Injection Molding Machines
Hybrid machines combine hydraulic power and electric efficiency, offering a balanced approach.
Advantages
- Versatile Performance: Ideal for high-precision and high-force needs.
- Efficient Motor Operation: Servo motors optimize power use, reducing waste.
- Cost-Effective: A balanced option for various manufacturing sectors.
Disadvantages
- Higher Cost than Hydraulic Machines: More expensive but often justified by efficiency gains.
- Manufacturer Variation: Performance can vary, making it essential to select a reputable manufacturer.
Related product: Servo machine – HRS series
Clamping style impacts machine setup and production flow. Here’s a look at horizontal, vertical, toggle-type, and two-platen styles.
Horizontal Injection Molding Machines
Horizontal machines are the industry standard, with molds clamped horizontally.
Advantages
- High Output: Suitable for large-scale production.
- Wide Applicability: Works with a variety of materials and parts.
Vertical Injection Molding Machines
Vertical injection molding machines inject material from above, ideal for specialized tasks.
Advantages
- Insert Molding: Facilitates complex insert molding and overmolding applications.
Disadvantages
- Lower Output: Not suitable for high-volume production due to reduced efficiency.
Further reading: Comprehensive Guide to Vertical Injection Molding Machines
Toggle-Type Injection Molding Machines
Toggle machines apply clamping force via toggle mechanisms, available in inward and outward models.
Advantages
- Consistent Clamping Force: Ideal for complex parts.
- Cost-Effective: Affordable option for many manufacturers.
Related product: Inward-toggle machine – HRN series
Related product: Outward-toggle machine – NRV series
Two-Platen Injection Molding Machines
Two-platen machines have a compact design, excellent for large molds.
Advantages
- Space-Saving: Reduced footprint.
- High Clamping Force: Suitable for large parts like automotive components
Further reading: 2 Platen Injection Molding Machine vs 3 Platen
Related product: Twp platen machine – NRH series
Injection molding machines can be divided by material capability, essential for selecting machines that handle thermoplastics or thermosets.
Thermoplastic Injection Molding Machines
Advantages
- Reusability: Allows material scraps to be reused.
Disadvantages
- Temperature Sensitivity: Requires precise temperature control.
Thermoset Injection Molding Machines
Advantages
- Durability: Suitable for high-heat, non-meltable applications.
Disadvantages
- Irreversible Process: Mistakes lead to waste, requiring careful management.
Multi-Material Injection Molding Machines
Designed for products needing multiple materials in one part.
Advantages
- Reduced Assembly Time: Produces multi-material components in a single cycle.
Related product: Double-shot machine – HDC series
Related product: Tri-shot machine – HTC series
The most commonly used machines today are horizontal-type, servo-driven hydraulic machines. These offer a balance of reliability, energy efficiency, and power, with applications across various sectors.
Further reading: Choosing the Right Injection Molding Machine: A Comprehensive Guide
FAQs About Injection Molding Machine Types
What are the different types of injection molding machines?
Injection molding machines are classified by power drive (hydraulic, electric, hybrid), clamping style (horizontal, vertical, toggle, two-platen), and material compatibility (thermoplastic, thermoset, multi-material).
Which injection molding machine type is best for high-precision parts?
All-electric machines are typically best for high-precision applications due to their energy efficiency, precision, and repeatability.
Selecting the right machine depends on your manufacturing needs, such as precision, production volume, and material requirements. Hydraulic machines are cost-effective and powerful, electric machines provide precision and energy savings, and hybrid machines offer a balance of both. For expert advice on choosing the best injection molding machine, contact Huarong—your experienced partner in injection molding solutions.
If you are searching for machines, please contact Huarong, an experienced injection molding machine manufacturer to provide expert guidance and support to help you achieve your needs.
- Group Name: Huarong Group
- Brand: Huarong, Yuhdak, Nanrong
- Service Offerings: Injection Molding Machine, Vertical Injection Molding Machine, Injection Molding Automation
- Tel: +886-6-7956777
- Address: No.21-6, Zhongzhou, Chin An Vil., Xigang Dist., Tainan City 72351, Taiwan
- Official Website: https://www.huarong.com.tw/
Previous news : Celebrating Innovation and Excellence: Huarong at TaipeiPlas 2024
Next news: Case Study: Elevating Product Packaging with In-Mold Labeling (IML) Technology