Case Study: Elevating Product Packaging with In-Mold Labeling (IML) Technology
2024-08-30 11:38:08
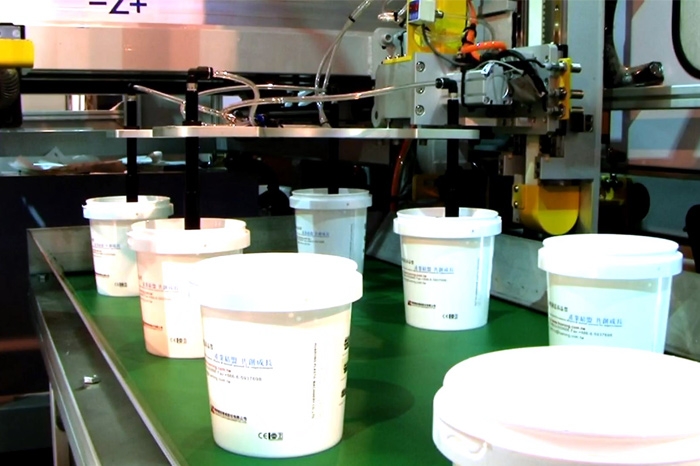
In-Mold Labeling (IML) packaging revolutionizes the way products are presented and protected in today's competitive market. This innovative technology seamlessly integrates product labeling with the packaging manufacturing process, resulting in durable, visually appealing, and cost-effective packaging solutions. In this case study, we'll explore how our customer leveraged IML technology to transform their product packaging, overcome traditional limitations, and achieve remarkable results in both aesthetics and functionality.
In-Mold Labeling (IML) packaging is a cutting-edge technique that integrates the label into the molding process, creating a seamless and durable finish. Unlike traditional methods, where labels are applied post-production, IML labels are placed directly into the mold before injection molding or blow molding begins, resulting in a seamless integration of the label and the packaging container. IML creates a single, unified product where the label becomes an integral part of the packaging itself.
We have previously shared more detailed knowledge about in-mold labeling, regarding its different processes and advantages. You can refer to it from the text below.
Further reading: What is IML? In Mold Labeling Process, Benefits, and Applications
Before we start analyzing our case study, let's first explore the limitations of traditional packaging methods, which are the main problems for our customers and lead them to adopt in-mold labeling.
Label Durability
For many manufacturers, especially those in the food and beverage industry, label durability is a crucial concern that directly affects product appeal and customer satisfaction. Traditional labeling methods typically involve applying labels to products after production. However, these labels often face durability issues such as:
- Peeling and Fading: Labels applied after production often peel off or fade when exposed to moisture, high humidity, or varying temperatures, especially for perishable products like dairy and beverages. This diminishes the product's visual appeal and compromises important information like brand identity, nutritional facts, and expiration dates, leading to potential consumer mistrust.
- Damage During Handling: Traditional labeling makes the labels more susceptible to damage during transportation, handling, and stocking. Scratches, scuffs, and tears can occur easily, affecting the product's overall appearance on retail shelves.
- Regulatory Compliance Risks: In industries where labeling is essential for compliance, such as food and pharmaceuticals, any decline in label quality can result in regulatory issues. If labels become faded or illegible, they may not meet legal standards, risking fines, recalls, and legal action. It is crucial to ensure that labels are durable and remain intact to comply with industry regulations and standards.
High Production Costs
Traditional labeling methods add significant overhead to the production process, particularly in high-volume industries. The extra steps needed for post-production labeling pose various cost-related challenges.
- Labor Costs: Workers are needed to manually or semi-automatically operate labeling machines, inspect products, and manage quality control processes, which increases payroll expenses.
- Material Waste: Traditional labeling methods often lead to higher material waste due to misaligned labels, errors in application, or damage during the labeling process, resulting in increased costs. The need for additional materials, such as adhesives and protective coatings, further contributes to material expenses and production costs.
- Production Downtime: Post-production labeling adds extra steps that can slow down manufacturing, as machines need to stop for labeling. This downtime reduces production efficiency and increases costs. Production delays can lead to missed deadlines, lost sales, and dissatisfied customers in competitive markets.
- Storage and Logistics: Managing separate inventories for labels and products increases logistical complexity and storage costs. Labels are applied after the product is formed. Finished products with labels cannot be stacked together due to the risk of damaging the labels. Labels must be stored in controlled environments to prevent damage or degradation before application, adding to storage overhead.
This case study examines the application of In-Mold Labeling (IML) packaging in a real-world scenario, focusing on how Huarong, a leading injection molding machine manufacturer, partnered with one of its valued customers—a prominent consumer goods company specializing in eco-friendly household products.
The customer was facing increasing pressure to improve its packaging to align with its sustainable brand image while also enhancing shelf appeal and durability. However, their existing packaging faced several issues:
- Labels were prone to peeling off when exposed to moisture or during prolonged use.
- The design options were limited, making it challenging to create visually striking packaging that stood out on store shelves.
- The labeling process was time-consuming and added significant costs to production.
- There were concerns about the environmental impact of adhesive-based labels on the recyclability of the containers.
To address these challenges, the company partnered with Huarong. Together, we embarked on a project to revolutionize customer's packaging using In-Mold Labeling Machine.
The implementation of In-Mold Labeling technology for customer's product line involved a carefully planned and executed process.
Label Design and Planning
Before entering the field of injection molding, let's talk about the preparatory steps that were taken to integrate IML into their packaging production. The process begins with designing the label, taking into account the product’s shape, size, and branding requirements. The designs incorporated vibrant colors, high-resolution graphics, and important product information. Special consideration was given to ensuring the designs would work seamlessly with the curvature and shape of the containers.
High-quality labels were produced using a material compatible with the container plastic. Common materials include polypropylene (PP) or polyethylene (PE). Additionally, the printing process may involve applying protective coatings to enhance the label’s resistance to scratches and fading.
Integration of IML Equipment
Now let’s talk about the equipment, including injection molding machines and molds. The mold itself is specially designed to accommodate the IML process. It includes cavities that precisely match the product's dimensions and features slots or recesses where the label will be placed. These molds are engineered with high precision to ensure a perfect fit for both the label and the plastic.
Huarong provided customer with state-of-the-art injection molding machines specifically designed for IML applications. Robotic systems were installed to automate the precise placement of labels into the mold cavities. With the label securely in place, the mold is closed, and molten plastic is injected into the cavity. The high temperature and pressure cause the plastic to flow around the label, encapsulating it and bonding it to the product surface. As the plastic cools and solidifies, the label becomes an integral part of the product's surface.
Related Product: IML - in molding labeling
The implementation of In-Mold Labeling technology brought numerous advantages to customer's product packaging. Let's explore the key benefits that IML offered:
Enhanced Durability:
The fusion of label and container created a scratch-resistant, waterproof surface that maintained its appearance throughout the product's lifecycle. Labels no longer peeled or faded, even when exposed to moisture or frequent handling.
Superior Aesthetic Appeal:
IML allowed for high-resolution, photorealistic graphics that wrapped seamlessly around the entire container. The ability to use a wider range of colors and finishes resulted in packaging that truly stood out on store shelves.
Improved Brand Consistency:
With labels integral to the packaging, brand elements remained pristine and visible, enhancing brand recognition and perception. The inseparable nature of IML labels made it easier to implement tamper-evident features, enhancing product security.
Increased Sustainability:
The elimination of separate labels and adhesives simplified the recycling process. The use of a single material for both container and label aligned with customer's eco-friendly brand image.
Improved Production Efficiency:
The integrated labeling process reduced overall production time and minimized the risk of labeling errors.
These benefits not only addressed customer's initial packaging challenges but also provided unexpected advantages that positively impacted various aspects of their business, from marketing to supply chain management.
The implementation of In-Mold Labeling (IML) technology has proven to address the customer's packaging challenges while aligning perfectly with their brand values and market positioning. By embracing IML, the company has not only enhanced the visual appeal and durability of their product packaging but also improved their production efficiency and environmental sustainability.
Are you ready to revolutionize your product packaging with In-Mold Labeling technology? Huarong offers state-of-the-art IML solutions tailored to your specific needs. Contact us today to explore how our expertise in IML technology can transform your packaging and give your products the competitive edge they deserve. Let's work together to create packaging that not only looks great but also contributes to a more sustainable future.
- Group Name: Huarong Group
- Brand: Huarong, Yuhdak, Nanrong
- Service Offerings: Injection Molding Machine, Vertical Injection Molding Machine, Injection Molding Automation
- Tel: +886-6-7956777
- Address: No.21-6, Zhongzhou, Chin An Vil., Xigang Dist., Tainan City 72351, Taiwan
- Official Website: https://www.huarong.com.tw/
Previous news : 7 Injection Molding Machine Types and Their Advantages and Disadvantages
Next news : Assembly Robots: The Evolution and Future of Robot Assembly Lines