Assembly Robots: The Evolution and Future of Robot Assembly Lines
2024-09-05 10:53:00
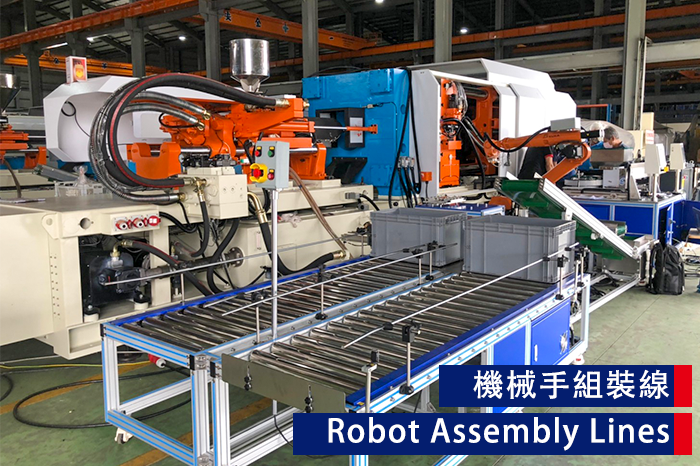
As businesses strive to meet the demands of the global market, the integration of assembly robots into production lines has become a cornerstone in modern manufacturing, enabling companies to enhance productivity, improve accuracy, and reduce operational costs. This article delves into the evolution, working mechanisms, and future trends of assembly robots.
Assembly robots are automated facilities designed to assemble parts and products on a production line. These robots are equipped with advanced sensors, actuators, and control systems, enabling them to perform complex assembly tasks with high precision and consistency. In the injection molding business, assembly robots ensure that components are accurately assembled, reduce human error, and increase production efficiency.
History of Robot Assembly Lines
The concept of robot assembly lines dates back to the early 20th century, but it wasn’t until the 1960s that the first industrial robots were introduced.
- Adoption and Expansion (1970s-1980s): Companies like General Motors were pioneers in adopting these robots, primarily for tasks such as welding and material handling. As technology advanced, so did the capabilities of assembly robots. By the 1980s, robots were being used in more intricate tasks, including assembly operations in the automotive and electronics industries.
- Technological Advancements (1990s-Present): The injection molding industry began integrating robots into assembly lines in the late 1990s. This shift was driven by the need for higher precision and the ability to handle delicate components that manual labor could not efficiently manage. Over the years, the evolution of robotics has led to more sophisticated assembly robots, capable of performing multiple tasks with minimal supervision.
Components of a Robot Assembly Line
A typical robot assembly line consists of several key components:
- Robotic Arms: Perform the actual insert molding and assembly tasks using tools attached to the end of manipulator arms, such as grippers, vacuum pads, welding torches, or screwdrivers, customized for specific assembly tasks.
- Conveyors: Transport finished or semi-finished parts between different stations on the assembly line, coordinating with the robots to ensure seamless operation.
- Sensors and Control Systems: Ensure each movement is executed accurately.
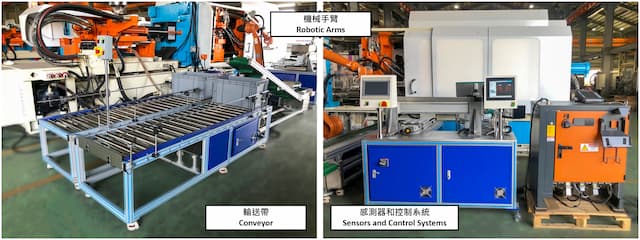
Types of Robotic Arms
Assembly robots are categorized by structure, arm design, and number of axes. Linear robots have hanging arm types for lightweight tasks, frame types for medium loads, and bullhead types for heavy-duty operations. Arm designs include single-arm single-section models and double-arm double-section designs. Robots operate on three to six axes, suitable for basic to complex assembly operations.
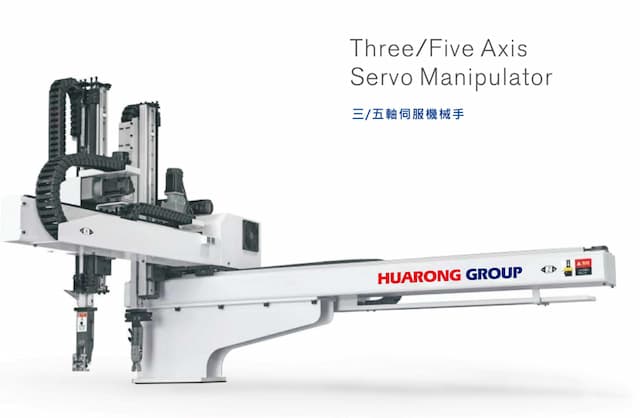
Related product: Manipulator Arm – HRB Series
Further reading: Comprehensive Guide to Injection Molding Robots: Automate Your Production Process
Robot assembly lines operate through a highly coordinated system integrating multiple advanced technologies. By combining programmable logic with real-time data processing and customized tooling, their capability to execute intricate, repetitive tasks with precision significantly boosts production efficiency and product quality, meeting the unique demands of modern manufacturing.
- Parts Feeding Systems: Supply the necessary components to the assembly robot, like the autoloader, incline conveyor, and vibration plate, which are designed to deliver parts consistently to ensure a steady stream of materials for the robots to work with.
- Machine Vision Technology: Integrate 'eyes' into the robots to verify part placement, sort through components, and perform quality inspections.
- Specialized Tooling: Customize end-of-arm tooling (EOAT) to handle the diverse range of parts that the robots may encounter, such as gripping, manipulating, and assembling components of varying shapes, sizes, and materials.
Applications in Different Industries
Assembly robots are used across various industries, including:
- Automotive: Perform tasks like welding, painting, and assembling parts to ensure that vehicles are assembled with high precision, reducing defects and improving safety.
- Electronics: Used to assemble small and delicate components, such as circuit boards and microchips to ensure that the components are assembled without damaging them.
- Injection Molding: Assemble parts of plastic components quickly and accurately to improve the overall production process efficiency.
- Food and Beverage Industry: Used for packaging, sorting, and palletizing food products in a hygienic and efficient manner to enhance operational efficiency and reduce the risk of contamination.
Integrating assembly robots into manufacturing processes can offer companies both advantages and limitations.
Pros
- Increased Efficiency: Assembly robots can operate 24/7 without fatigue, significantly increasing production rates.
- Enhanced Precision: Robots can perform tasks accurately, ensuring consistent product quality and reducing waste and rework.
- Cost-Effective: Over time by minimizing the need for manual labor, robots can lower operational costs, increase productivity, and improve profitability, leading to a higher return on investment.
- Safety: Robots can perform dangerous tasks, reducing the risk of injury to human workers.
Cons
- High Initial Cost: The setup cost of purchasing and integrating assembly robots can be prohibitive for small businesses.
- Maintenance: Robots require regular maintenance to ensure they operate efficiently.
As technology continues to evolve, with advancements in AI and machine learning leading to more intelligent and autonomous robots, the role of robots in assembly lines will grow to be more innovative, faster, and more efficient in the production process. Additionally, integrating collaborative robots (cobots) will allow human workers to work alongside robots, combining both strengths to achieve optimal results. In injection molding, we also expect to see more specialized robots designed.
- Industry 4.0: The integration of IoT, AI, and big data is expected to create smarter, more autonomous robotic systems.
- Collaboration with Humans: Advances in cobot technology will enable robots and humans to work side by side safely.
- Increased Customization: Future assembly lines may allow for more flexible manufacturing processes to accommodate smaller batch sizes and customization.
- Sustainability: Robotic systems will likely incorporate environmentally friendly practices, such as energy-efficient operations and reduced waste.
Robotic assembly lines offer an efficient and safe manufacturing environment. Despite challenges like high costs and the need for specialized training, the benefits of increased productivity, quality, and safety make them indispensable in modern production. With ongoing advancements in AI and robotics, these systems will continue to evolve, driving innovation across industries.
FAQ Related to Assembly Robots
1. What maintenance do assembly robots require?
Assembly robots require regular maintenance to ensure optimal performance. This includes routine checks on sensors, actuators, control systems, and software updates to improve functionality. Preventive maintenance can help avoid costly breakdowns and extend the lifespan of the robots.
2. Can assembly robots work with existing manufacturing systems?
Yes, assembly robots can be integrated into existing manufacturing systems. However, some modifications to the current setup may be required. Many modern assembly robots are designed to be flexible and compatible with various systems, making integration smoother and more efficient.
Meet Your Injection Molding Needs
Huarong is an experienced injection molding machine manufacturer that provides not only complete injection machine types but also customers’ injection molding partners to provide future-automated production lines and factory automation to enhance competitiveness. Huarong has an independent and professional automation department with over ten years of expertise and experience in electromechanical integration to provide customers with non-standard and customized automation systems.
- Group Name: Huarong Group
- Brand: Huarong, Yuhdak, Nanrong
- Service Offerings: Injection Molding Machine, Vertical Injection Molding Machine, Injection Molding Automation
- Tel: +886-6-7956777
- Address: No.21-6, Zhongzhou, Chin An Vil., Xigang Dist., Tainan City 72351, Taiwan
- Official Website: https://www.huarong.com.tw/
Previous news : Case Study: Elevating Product Packaging with In-Mold Labeling (IML) Technology
Next news : A Success Story with Huarong's Vertical Injection Machine: Enhancing Precision and Efficiency