Huarong Showcase 4 Innovative Breakthroughs in 7 Injection Molding Machines at TaipeiPlas 2024
2024-09-19 14:15:34
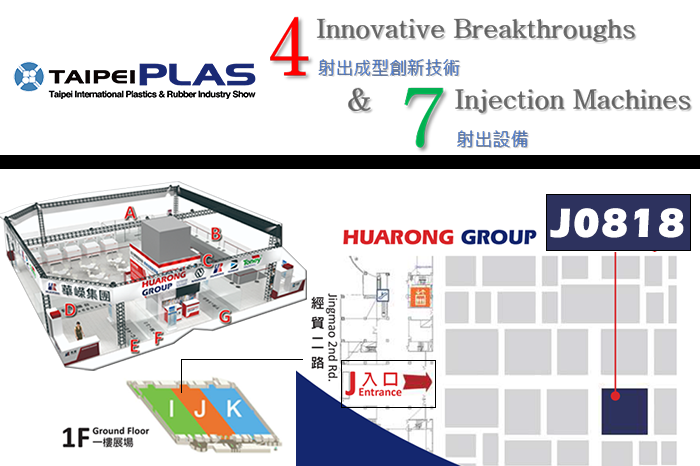
As a specialized injection molding machine manufacturer, Huarong continuously strives to develop groundbreaking technologies that meet the demands of a rapidly evolving market. With the injection molding market growing, sustainability and ESG (Environmental, Social, and Governance) are no longer just trends—they are imperatives. Upholding the spirit of ESG, Huarong is committed to innovating for the future, focusing on reducing plastic waste and energy consumption.
Here at Huarong, we proudly present our latest technological advancements, which improve operational efficiency and reduce energy consumption and material waste. These advancements are in line with our commitment to sustainability and ESG principles. Below, we will delve into 4 innovative breakthroughs in injection molding machines that will be displayed at TaipeiPlas 2024:
- Smart Two-Platen Injection Molding Machine
- Ultra-Energy Efficient Direct Drive Material Storage
- Hairclip Double-Shot Automated Molding System
- Microcellular Foam Injection Molding Device.
Related reading: Celebrating Innovation and Excellence: Huarong at TaipeiPlas 2024
The Smart Two-Platen Injection Molding Machine is our featured popular product and winner of the 2024 Taiwan Excellence Award.
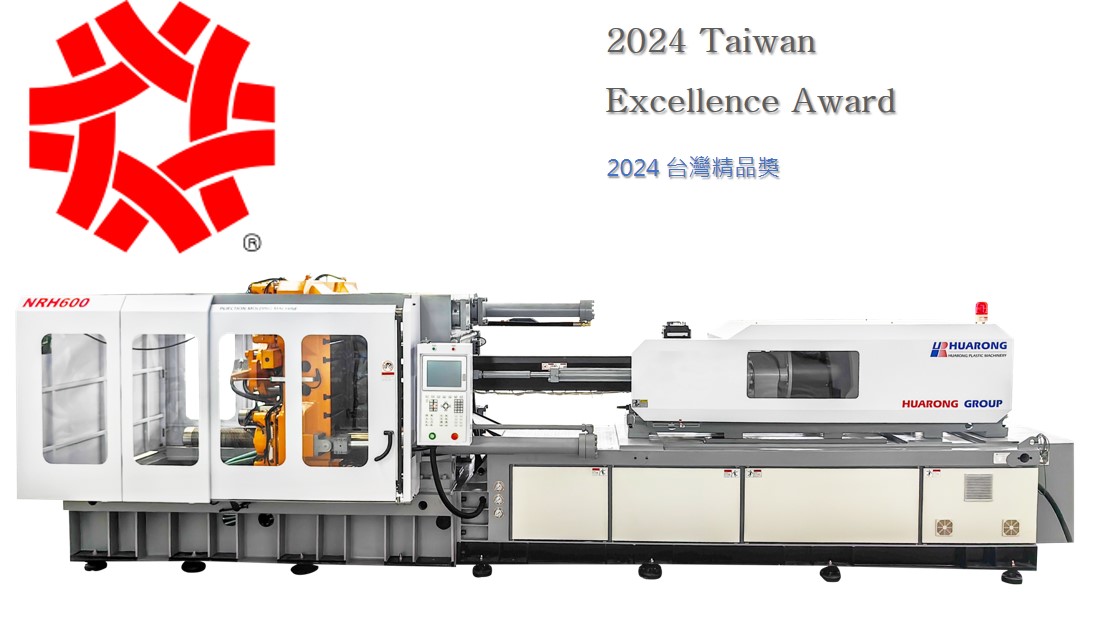
Further reading: HUARONG is honored with the 2024 Taiwan Excellence Award!
Unlike traditional injection molding machines, the two-platen design reduces the space footprint by up to 22%, making it ideal for medium-to-large machines with premium factory space.
Related product: Two-platen Injection Molding Machine – NRH Series
Advanced Patented Technology for Enhanced Precision
Regarding technological innovation, we’ve improved assembly efficiency and accuracy by optimizing the design of the tie-bar bearing, inner sliding, and machine positioning, which is backed by patent certifications. These innovations help reduce raw material waste, enhance machine stability, and minimize wear and tear.
- Suspension Bearing Module – Patent M634662
- Inner Sliding Module – Patent M578643
- Injection Machine Positioning Device – Patent M636571
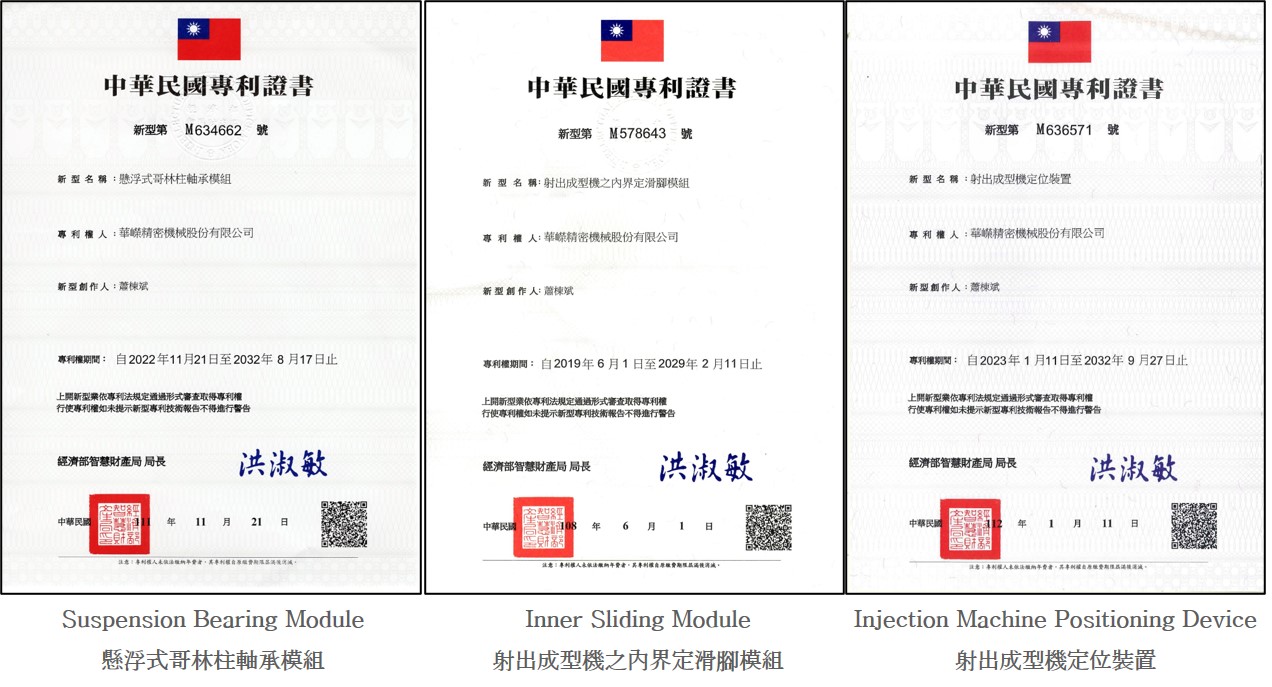
Further reading: Two-Platen Injection Molding Machine Obtained Patent Certification to Provide Better Machine
Smart Factory Management for Real-time Monitoring and Access to Crucial Data
The machine features a Smart Factory Management System aligned with ESG trends. This system allows companies to integrate machine statuses across all plants, offering real-time monitoring and access to crucial information like production data, machine parameters, alarm records, and even micro-anomalies. It can also be integrated with the MES system for detailed production data tracking and analysis, further boosting production efficiency.
Related product: Smart Factory Management – HFM
Huarong’s patented direct-drive material storage servo motor is an innovative breakthrough in material storage systems. This innovative system aims to minimize energy consumption while maintaining high performance and stability.
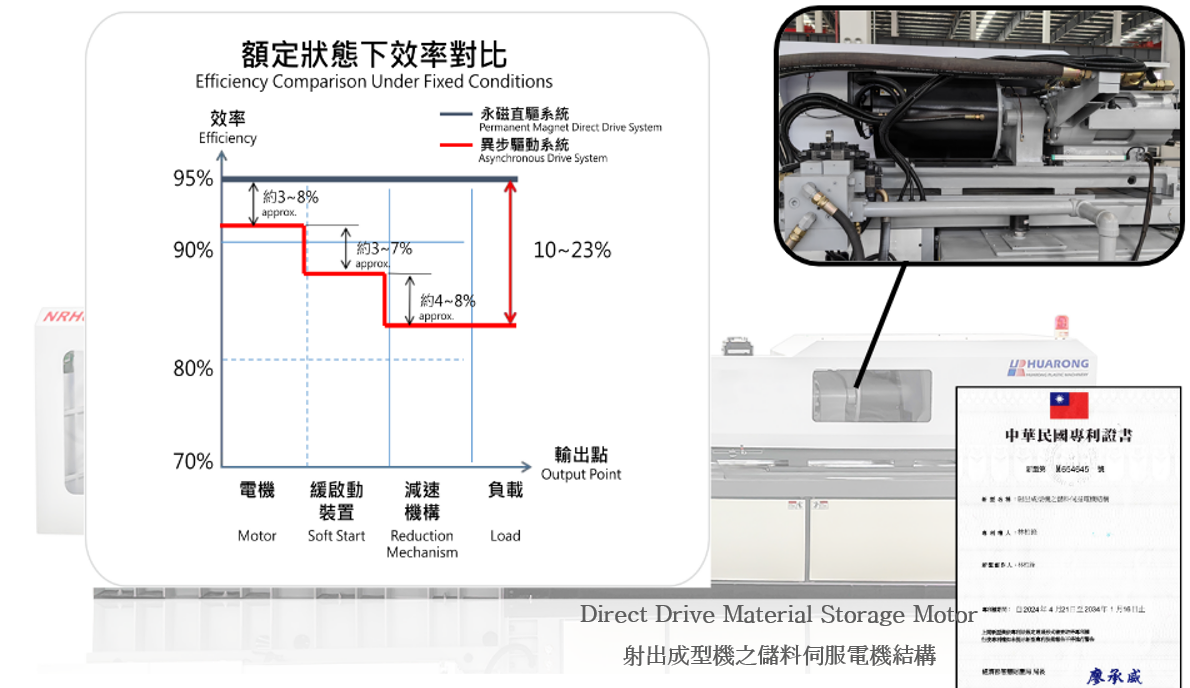
Highly Efficient and Stable Design
Our patented direct-drive servo motor is designed to handle high axial and torque loads, eliminating the need for traditional hydraulic motors and gearboxes. This makes the system more efficient and reliable, reducing the risk of mechanical breakdowns. As a result, the system consumes up to 26% less energy than conventional systems during the material storage process.
Synchronized Operations for Shorter Cycles
What sets this system apart is its ability to operate independently. The direct-drive material storage servo motor can be controlled independently, allowing simultaneous storage during mold opening and product cooling, shortening the molding cycle.
Further reading: Energy-Efficient Direct Drive Material Storage Motor
Huarong has customized the planning of hairclip double-shot molding automated production systems for manufacturers looking to enhance production efficiency through automation. This system integrates the injection, transfer, assembly, and packaging systems to fulfill a fully automated production process.
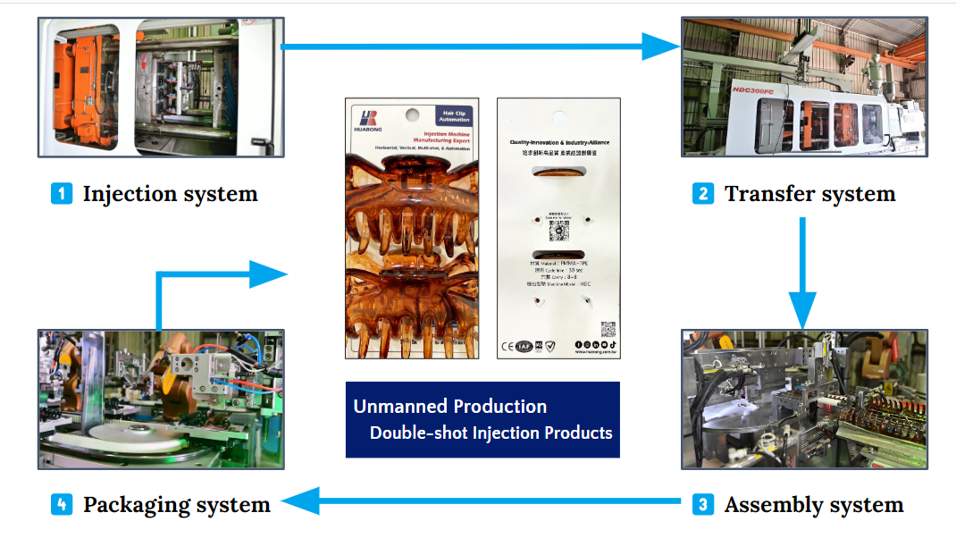
Real production video: Automated Hair Clip Production With Injection Molding | Huarong
Seamless Automated Process, 24/7 Operation
The process starts with injecting the hairclip, which is then automatically transferred to the assembly area. Once the assembly is complete, a robotic arm places the hairclips into the packaging section, where they are attached to the cardboard using silicone straps. With this system, manufacturers can achieve 24-hour production with minimal human intervention.
Innovative Threading Method
This fully automated system overcomes the challenges of transferring, positioning, clamping, and assembling irregularly shaped products, combining two opposite hairclips with a torsion spring and pin. Most importantly, there is an innovative threading method to fix hairclips onto packaging carboard with silicone bands to complete production.
Related service: Automation system
Microcellular Foam Injection Molding Device is a breakthrough technology designed to reduce material usage, lower product weight, and improve dimensional stability.
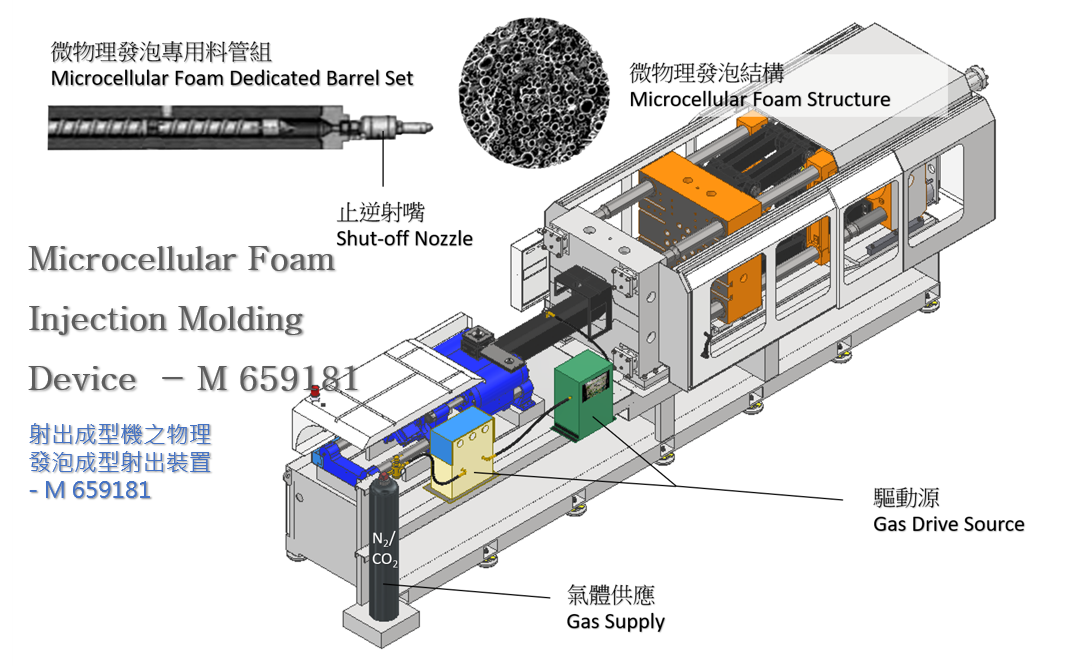
Supercritical Fluid Technology for Lightweight and Material Cost Savings
Supercritical fluids, such as nitrogen or carbon dioxide, are precisely controlled to be injected into molten plastic, forming a uniformly distributed microcellular structure (foam). The internal microcellular structure reduces the product's density and weight, plastic usage, and material costs without significantly affecting its mechanical properties.
Improved Dimensional Stability
Microcellular foam injection molding technology reduces internal stress shrinkage, improving warpage deformation and enhancing dimensional stability for greater accuracy and stability.
Shorter Molding Cycles
Compared to traditional injection molding, microcellular foam injection molding shortens cycles, boosts efficiency, and suits time-sensitive industries.
Environmental Protection and Energy Saving
The reduced material usage and shorter molding cycles offer environmental and energy-saving benefits, helping companies meet higher environmental standards and ESG goals.
We warmly welcome all visitors to experience our latest innovations firsthand at booth J0818. Taipeiplas 2024 (9/24 to 28) will be open daily from 10 AM to 6 PM. To enter TaipeiPlas, visitors have two options:
- Online Pre-Registration: Complete the registration on the official exhibition website and obtain a QR code for entry. Scan your QR code at the entrance during the exhibition period for hassle-free entry. Registration URL: Online registration
- On-Site Registration: During the exhibition, visitors can register at the reception desk using a computer or mobile device to fill out the required details and receive a QR code for entry.
Don't miss this opportunity to see our latest innovations and enjoy the exclusive giveaways!
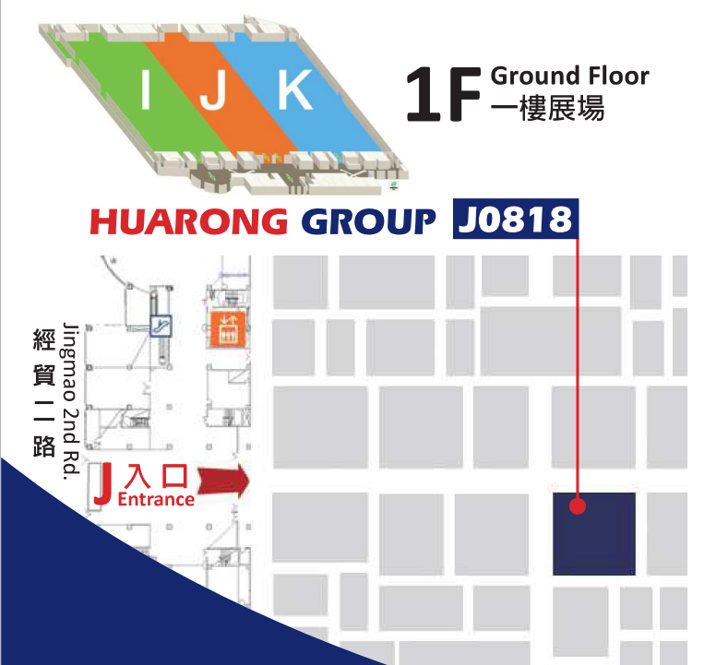
7 Innovative Equipments Display at Booth J0818
At TaipeiPlas 2024, we proudly showcase 7 advanced injection molding machines, each highlighting our commitment to cutting-edge technology and automation. These machines will be in full operation, producing high-quality plastic products that will be gifted to visitors. The featured equipment includes:
- Smart Two-Platen Injection Molding Machine (NRH-600L) – Paired with an HFM robotic arm, this machine will produce PP stools.
- Hairclip Double-Shot Automated Molding System (HDC-300FC) – This fully automated system integrates injection, transfer, assembly, and packaging to produce double-shot hairclips.
- In-Mold Labeling System (IML)
- Microcellular Foam Servo Injection Molding Machine (HRF-200) – This machine will produce lightweight PE fan guards using microcellular foam technology.
- Tie-bar-less Vertical Clamping Machine with Horizontal Injection (YC-40-V)
- Vertical Injection Machine with Rotary Table (YR-90-3R2)
- Rubber Vertical Injection Machine with Tie-bar-less (CM-30-3L1S-ZS)
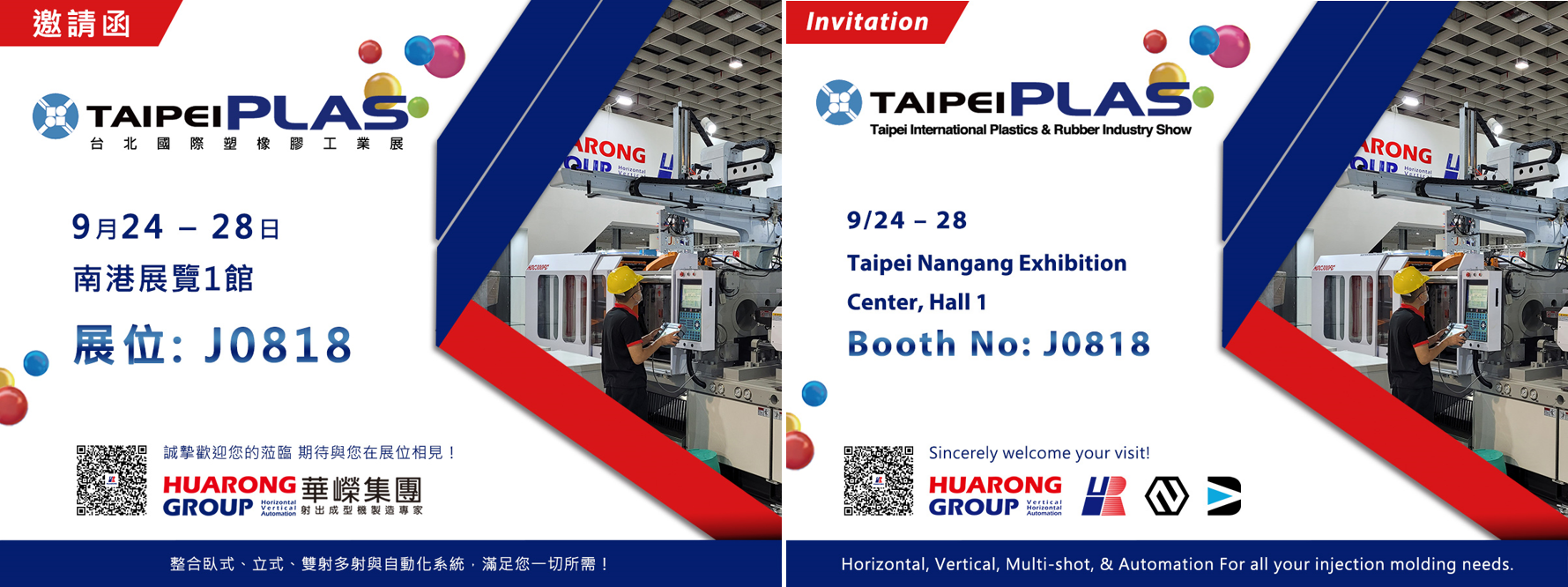
Previous news : A Success Story with Huarong's Vertical Injection Machine: Enhancing Precision and Efficiency
Next news : Interview: Vice Chairman of the Plastics and Rubber Machinery Committee – Huarong Plastic Machinery