Boosting Efficiency: NEOLITE ZKW's Success with Huarong Injection Molding Machine
2024-10-11 16:00:58
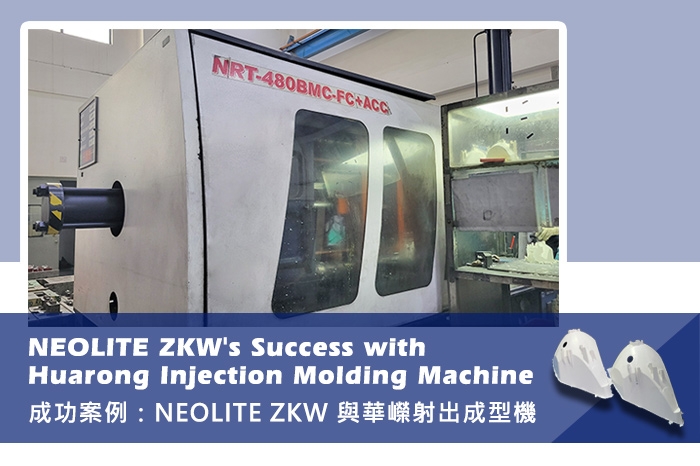
Manufacturing precision and efficiency are crucial for maintaining a competitive edge in the highly competitive automotive lighting market. One of India’s largest automotive lighting OEMs sought a solution to overcome production challenges, particularly those related to the complex injection molding materials used in their lamp housings. After implementing Huarong’s BMC injection molding machine, the company experienced remarkable improvements in production stability and efficiency, making its investment in high-performance machinery a crucial factor in its ongoing success.
Further reading: Injection Molding Machine: Key to Precision Manufacturing of Automotive Parts
Producing automotive lamp housings involves working with complex composite materials, including unsaturated polyester resin, epoxy resin, glass fibers, and other additives that ensure high insulation and temperature resistance. These materials placed a heavy strain on the manufacturer’s production equipment, leading to critical issues:
Impact on Production Efficiency
The BMC materials used by the manufacturer were rigid on the material cylinders of their existing injection molding machines, leading to frequent malfunctions and downtime. This not only slowed production but also affected overall product quality and consistency. The primary challenges included:
- Material Cylinder Durability: The combination of glass fibers and resins severely impacted the durability of the machine’s material cylinder, causing frequent breakdowns.
- Inconsistent Product Quality: Machine instability directly affected product precision, leading to higher defect rates and compromised quality control.
- Production Downtime: Each material cylinder malfunction halted production, reducing efficiency and delaying deliveries.
The company needed a machine that could withstand the rigors of BMC materials while maintaining high production efficiency and product quality.
Further reading: Thermoset Injection Molding: Process, Benefits & Applications
To address these challenges, the manufacturer invested in Huarong’s HMC series horizontal injection molding machine, specifically designed for processing BMC (Bulk Molding Compound) materials. The machine’s advanced features proved critical in solving their production issues.
Key Features of the Huarong Machine
Huarong’s machine provided several innovative features that ensured better performance and reliability for the manufacturer:
- Dual Alloy Screw: The machine is equipped with a dual alloy material cylinder, enhancing wear resistance when processing thermosetting plastics like BMC. This upgrade significantly reduced material cylinder wear and tear, lowering the risk of downtime.
- Patented BMC Feeding System: This system offers independent feeding, ejection, and material loading, improving both speed and stability in production. It ensures the smooth processing of BMC materials without clogging or delays.
- ACC Accumulator System (Optional): The ACC system uses nitrogen gas pressure to accelerate hydraulic operations, reduces overall molding time, and contributes to shorter production cycles and enhanced efficiency.
These features enabled the manufacturer to overcome the durability and efficiency challenges posed by their materials, improving production processes across the board.
Related product: HMC Injection Molding Machine
Since integrating Huarong’s HMC series machine, the manufacturer has reported significant improvements in the injection molding field in several key areas of their production:
Improved Product Precision
One of the most immediate benefits was the enhancement of product precision. The advanced features of Huarong’s machine minimized the variations that previously affected the quality of the lamp housings. As a result, the company saw a reduction in defective products and an increase in overall quality.
Reduced Defect Rate
With improved precision, the company significantly lowered its defect rate. This decrease in defective units reduced waste and improved overall production efficiency and cost management.
Enhanced Production Efficiency
By reducing the frequency of machine malfunctions and minimizing downtime, the company experienced a marked increase in production speed. They maintained a more consistent output without sacrificing quality, leading to shorter lead times and better customer satisfaction.
Cost Savings and Improved Competitiveness
The combination of reduced defects and enhanced efficiency led to significant cost savings. These savings allowed the company to allocate resources to other areas of its injection molding business, strengthening its competitive position in the global automotive lighting market.
Further reading: Success Stories: How Elevate South African Manufacturer's Manufacturing Capabilities with Two-platen
Huarong's BMC injection molding machine provided the manufacturer with a highly reliable solution to their production challenges. By improving machine stability and enhancing production efficiency, the company was able to overcome long-standing issues, ultimately improving its ability to meet the increasing demand for high-quality automotive lighting products.
For manufacturers facing similar production challenges, investing in advanced machinery like Huarong's injection molding equipment can provide a critical advantage in maintaining high standards of precision and efficiency.
Ready to transform your production line with Huarong's reliable injection molding machines?
- Group Name: Huarong Group
- Brand: Huarong, Yuhdak, Nanrong
- Service Offerings: Injection Molding Machine, Vertical Injection Molding Machine, Injection Molding Automation
- Tel: +886-6-7956777
- Address: No.21-6, Zhongzhou, Chin An Vil., Xigang Dist., Tainan City 72351, Taiwan
- Official Website: https://www.huarong.com.tw/
Previous news: Huarong's Success at TaipeiPLAS 2024: A Step Toward Sustainable Innovation
Next news: Four Core Innovations: Enhancing Efficiency with Hairclip Dual-Injection Molding Automation System