PET Preform Molding Solution: A Detailed Guide to PET Preform Manufacturing
2024-10-30 16:20:36
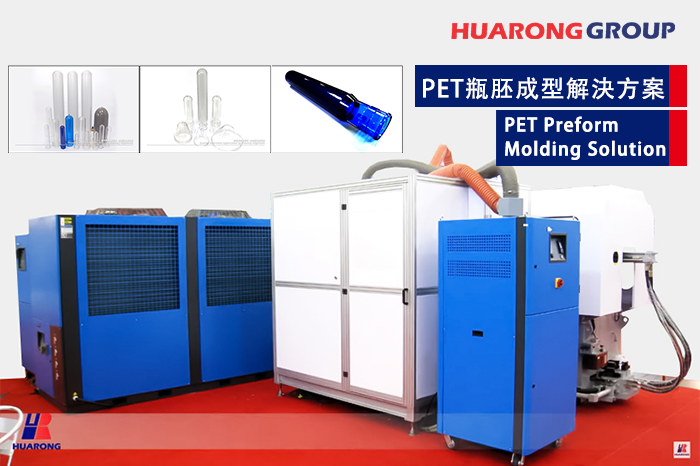
Many people ask Huarong questions about starting their PET preform manufacturing unit but are often unsure where to begin. Huarong, an experienced injection molding machine manufacturer, has crafted this comprehensive guide to the PET Preform Molding Solution to address these needs. This article covers every step of the preform production process to solve your related problems.
PET preforms are a vital intermediary step in bottle production, ensuring manufacturers achieve high-quality, lightweight, and substantial containers. The demand for PET preforms stems from their durability, lightweight properties, and recyclability, which make them ideal for packaging a range of beverages and products.
What Is a PET Preform?
A PET preform is a test-tube-shaped initial product created from PET plastic, which is then expanded into bottles during the blow molding process. Preforms provide a standardized, quality-controlled step in bottle manufacturing, enabling consistent shapes, sizes, and weights in the final product.
Benefits of PET Preforms for Bottling Applications
Preforms can be produced, stored, and transported as needed, allowing for better inventory management. Manufacturers can produce preforms during off-peak seasons and stockpile them for peak demand, ensuring a consistent supply without overextending their resources, which achieves more efficient production cycles.
Using PET preforms that separate bottle production in the two-step process, injection molding and blow molding operations, provides manufacturers with greater operational flexibility. During the reheating stage in blow molding operations, manufacturers can adjust blow molding machine settings such as heating, position, and power to make bottles more evenly stretched and lighter in weight, significantly lowering material costs without sacrificing quality.
PET preforms are especially beneficial for high-volume production and are well-suited for the beverage industry's packaging requirements, where reducing weight is essential for cost savings and environmental sustainability.
The PET preform molding process begins with preparing PET resin, which must be handled appropriately to ensure optimal molding results. Here is an in-depth look at each step of PET preform manufacturing:
Step 1: PET Resin Preparation and Drying
Drying PET resin is essential as it ensures that the material is free from moisture, which can cause defects like cloudiness and brittleness. With dehumidifying dryers, the resin removes moisture to set the stage for high-quality injection molding.
Step 2: Injection Molding for PET Preforms
In the injection molding process, dried PET resin is heated and injected into a preform mold. This step determines the preform's shape, weight, and wall thickness.
Step 3: Preform Cooling and Solidification
Once molded, the preform undergoes rapid cooling. Cooling is a crucial step in the PET preform manufacturing process, impacting cycle time and the preform’s transparency and structural integrity. Uneven cooling can cause dimensional inaccuracies and defects in clarity, as PET is sensitive to temperature changes.
Step 4: Quality Control in PET Preform Manufacturing
Quality control is essential for ensuring that each preform meets precise specifications for efficient, high-quality bottle production. Automated inspection systems evaluate various aspects of each preform, emphasizing quality checks, dimensional accuracy, and other factors to reduce production issues, ensuring that each preform is optimized for the blow molding process. Below are the primary areas inspected:
- Perform Neck and Thread Inspection: Inspect for defects such as chips, scratches, and foreign particles. Check the preform's threading area for scratches and black spots, and ensure accuracy around the thread and support ring, which are vital for cap compatibility and sealing.
- Bottom Inspection: Inspect the base of the preform for issues like yellowing, scratches, and foreign particles that could affect bottle stability and appearance.
- Body Inspection: Ensure a smooth, defect-free surface along the preform’s body, checking for scratches, black spots, or any contaminants.
Producing high-quality PET preforms depends on specialized equipment designed to handle the demands of high-output manufacturing environments. With reliable machinery, the production of PET preforms becomes more efficient, minimizing issues that could compromise quality.
Injection Molding Machine for PET Preforms
As the core of PET preform manufacturing, the PET preform injection molding machine is built for precision, efficiency, and consistency. These machines transform PET resin into high-quality preforms that serve as the intermediate product in bottle production.
Related product: PET Injection Molding Machine – PET Series
Essential Features for High-Performance PET Preform Production
- Enhanced Barrel and Screw Design for PET Materials
Feature a specialized PET-specific barrel and screw design that maximizes injection volume and feeding speed. With an increased screw diameter and Length-to-Diameter (L/D) ratio, that maintains stable material flow and minimizes cycle times. - Configurable Double-Circuit System for Optimized Cooling and Storage
Our machines will evaluate the customers’ production conditions to be equipped with a double-circuit system for simultaneous mold opening and material storage. This setup is especially advantageous for preforms with thinner walls, as the cooling time is shorter than the storage time. This system improves production efficiency and cycle consistency by initiating material storage while the mold is still cooling, resulting in a smoother workflow and higher productivity. - Optional Separate Injection and Plasticization Unit for Enhanced Stability
For applications needing consistent plasticization, an optional separate unit can be installed so that isolating plasticization from injection enhances material quality stability. - Servo System
Combine the speed and power of hydraulic components with the precision of electric-driven systems to create a servo system ideal for PET preforms. This setup delivers the necessary force for high-speed injection.
PET Preform Mold Design and Cavity Options
Designing an effective PET preform mold requires thoroughly evaluating multiple factors, including preform dimensions, weight, wall thickness, and projected production volume. These factors help determine the appropriate mold cavity count and design specifications to meet production needs efficiently and precisely.
Related production video: 48-Cavity Preform Production
Key Specifications for PET Preform Molds
- Preform Dimensions and Neck Standards: PET preforms are produced with neck standards. PCO 1881 is one of the most common dimensions used in the beverage industry due to its compatibility with lightweight, high-volume bottle production. Other neck standards, such as PCO 1810, BPF, and 30/25, are also available and vary based on end-use, application requirements, and regional preferences.
- Preform Weight and Wall Thickness: The weight of the preform determines the bottle’s overall strength and structural integrity, directly impacting its ability to withstand pressures, particularly in carbonated applications. Wall thickness (“preform thickness”) is another critical factor affecting cycle time.
- Mold Cavity Count for Production Efficiency: Based on the required production output, the mold’s cavity count is carefully chosen to balance productivity with quality. For high-volume operations, multi-cavity molds with 24, 48, 72, or even 96 cavities are often used to maximize production rates without compromising the consistency of each preform.
Auxiliary Equipment in PET Preform Molding
Auxiliary equipment is essential to maintain the consistency of bottle preform quality and improve production efficiency. It is configured based on the hourly PET usage (kg), and common related equipment is as follows:
- Dehumidifying Dryer and Feeder Combination: This equipment combines dehumidification and drying systems to remove moisture from PET resin, ensuring a stable feed and protecting the production process from moisture interference.
- Vacuum Automatic Feeding System: This system utilizes a vacuum feeding method to ensure continuous material supply, reduce downtime, and enhance production efficiency.
- Mold Dehumidifier: The mold dehumidifier keeps the mold interior dry, paired with a detachable return air collector to prevent excessive moisture retention, ensuring stable mold performance and extending mold life.
- Chiller: Rapidly cools preforms and maintains stable temperature control, shortening production cycles while meeting environmental standards.
Huarong, as a machine manufacturer, determines the optimal specifications for the injection molding machine according to the detailed customer information. Below is a guide to the critical details to configure the machine to meet your production goals effectively.
Preform Information
Please provide the preform photo, dimensions, weight, thickness, and intended use. For example, the thickness and dimensions of the PET preform impact the machine’s required injection capacity, clamping force, and cycle time. Knowing the application (e.g., water bottles, carbonated beverages) also helps us determine the ideal machine configuration to maintain consistent quality.
Mold Information
The design and cavity count of your mold greatly influences machine selection. Please share details about the mold dimensions and cavity number (e.g., 24, 48, or 96 cavities). This enables us to match the machine’s clamping force and platen size to your mold, ensuring compatibility and efficient operation.
Expected Productivity
The anticipated production volume is essential for configuring machine output and efficiency. By specifying your target production rate (e.g., daily or hourly capacity), we can recommend an injection molding machine with the appropriate cycle time and cavity count. This information also informs decisions on automation features and auxiliary equipment to optimize production flow.
When selecting a partner for PET preform production, a reliable and experienced solution provider makes a difference. With over 40 years of expertise, Huarong Group—which includes brands like Huarong, Yuhdak, and Nanrong—stands out as a trusted partner for injection molding solutions, offering a complete range of injection molding machines and automation systems. For inquiries on injection molding machines or complete automation solutions, Huarong Group is ready to be your dependable partner in injection molding.
- Group Name: Huarong Group
- Brand: Huarong, Yuhdak, Nanrong
- Service Offerings: Injection Molding Machine, Vertical Injection Molding Machine, Injection Molding Automation
- Tel: +886-6-7956777
- Address: No.21-6, Zhongzhou, Chin An Vil., Xigang Dist., Tainan City 72351, Taiwan
- Official Website: https://www.huarong.com.tw/
Previous news : 4 Core Innovations in Revolutionary Double-Shot Hairpins Automated Technology by Huarong
Next news : Huarong Wins 2025 Taiwan Excellence Award for Innovative Injection Molding Technology