Microcellular Foam Injection Molding: Achieving Maximum Weight Reduction and Dimensional Stability
2024-11-13 11:29:57
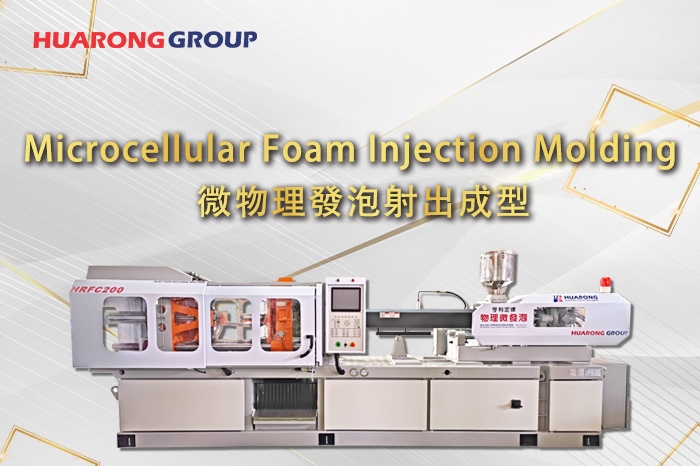
In today’s rapidly evolving manufacturing environment, the focus on sustainability and long-term growth is stronger than ever, with environmental, social, and governance (ESG) considerations driving innovation. Reducing plastic material usage is not just a cost-saving measure—it’s a critical strategy for companies seeking lasting success in this eco-conscious future. Microcellular Foaming Injection Molding offers a cutting-edge solution to this challenge, enabling manufacturers to minimize material use while maintaining or improving product strength and performance.
Microcellular foam injection molding involves introducing a gas, such as nitrogen or carbon dioxide, into the polymer melt under high pressure. The gas is dissolved evenly in the material, forming a supersaturated polymer-gas mixture. The pressure drops sharply upon injection into the mold, causing the gas to expand and form micro-cellular bubbles within the polymer. This controlled foaming process results in a final product with a reduced density while maintaining the mechanical integrity of the component.
Further reading: Microcellular Foam Injection Molding Technology
Core Characteristics of Microcellular Foam Injection Molding
Because this technology forms microcellular bubbles within the polymer, the injection molding process has a few core characteristics that set it apart from traditional injection molding:
- Weight and Density Reduction (Lightweight Parts): The primary benefit is significant weight reduction by 15%-20% without compromising mechanical strength.
- Lower Material Costs: By reducing the amount of plastic used in each part, manufacturers can save significant amounts on raw materials.
- Dimensional Stability: After introducing microcells, the parts produced exhibit excellent dimensional stability.
- Cycle Time Reduction: The part's uniform cell structure eliminates the holding pressure phase, shortening production times and resulting in faster cycle times.
- Environmental Benefits (Sustainability and Recycling): This process lowers energy consumption by reducing the material used and shortening cycle times, making it more environmentally friendly than traditional molding. Besides, unlike chemical foaming methods, microcellular foam injection molding belongs to physical forming methods, not leaving behind harmful residues, making the product more environmentally friendly and suitable for recycling back into the production stream.
- Clamping Force Requirement Reduction: The foaming process reduces clamping force compared to traditional injection molding, allowing manufacturers to produce larger components on smaller machines and lowering costs.
- Process Efficiency Enhancement: Through the combination of reduced cycle times, material savings, and the ability to use smaller tonnage machines, microcellular foam injection molding offers substantial cost savings and faster cycle times, enhancing productivity and throughput in the manufacturing process.
- Mold Wear Reduction: The lower internal pressure in microcellular foaming reduces mold wear and tear, extending mold service life and allowing for longer production runs before refurbishment or replacement.
Microcellular foam injection molding follows a similar sequence to traditional injection molding but introduces additional steps that enhance the final product's performance, particularly in weight reduction and material efficiency. Here’s how the process compares to the traditional method, highlighting the unique elements of microcellular foam molding:
Further reading of traditional injection molding: What is Injection Molding? Processes, Benefits, and Applications
Step 1: Clamping
The process starts with clamping, where the two halves of the mold are pressed together using a clamping unit. This step ensures that the mold stays securely closed during the injection phase. However, a key difference is that microcellular foam molding requires much less clamping force due to the foaming action. The decreased clamping force saves energy and enables larger parts to be produced on smaller machines, reducing costs.
Step 2: Injection with Gas Dissolution
In traditional injection molding, plastic granules or pellets are melted and injected into the mold cavity under high pressure. However, in microcellular foam injection molding, a supercritical gas, nitrogen or carbon dioxide, is introduced into the molten plastic during the injection phase. This process, known as gas dissolution, allows the gas to dissolve into the polymer melt evenly. The presence of gas reduces the density of the material, offering the potential for lightweight yet strong parts.
Step 3: Nucleation and Eliminating Dwelling
In traditional injection molding, the dwelling phase is necessary to maintain pressure, ensure cavity fill, and prevent material backflow. This stage often leads to increased cycle times and energy consumption due to the sustained holding pressure. However, in Microcellular Foam Injection Molding, the formation of uniform microcells within the material eliminates the need for this dwelling phase. As a result, there is no need to hold pressure to fill gaps in the cavity. This reduction in energy-intensive steps contributes to lower energy consumption during molding.
Step 4: Cooling and Cell Growth
In both processes, the plastic begins to cool once it is injected into the mold cavity. During this stage in Microcellular Foam Injection Molding, the formed cells (bubbles) expand uniformly as the material cools. This cell growth reduces the overall density of the part while maintaining its structural integrity. The cooling time may be slightly shorter in microcellular molding due to the presence of gas bubbles, which can improve production efficiency.
Step 5: Mold Opening
After the plastic part has cooled and solidified, the mold is opened like traditional molding. The clamping mechanism releases, and the mold halves separate, revealing the newly formed part. Microcellular foam parts have a lower density, resulting in less material shrinkage than traditional solid parts. This leads to better dimensional stability and fewer post-mold defects.
Step 6: Ejection
The cured part is ejected from the mold cavity in the final stage. Like the traditional process, an ejector pin is used to push the part out of the mold. The main difference here is that microcellular parts often require less force during ejection due to the material's reduced density and foamed nature, leading to smoother ejection with fewer defects. Trimming of excess material may still be necessary, but microcellular parts tend to have less material waste due to their efficient use of raw materials.
The efficiency of Microcellular Foam Injection Molding relies on a few critical components:
- Gas Supply (Nitrogen or Carbon Dioxide): The gas supply is a crucial component that provides the necessary inert gas, typically nitrogen or carbon dioxide, to create the microcellular structure.
- Gas Drive Source: This component delivers the precise amount of gas at a controlled pressure into the polymer melt. It ensures consistent and homogeneous gas dissolution within the polymer during the plasticizing phase, essential for forming a uniform microcellular structure.
- Microcellular Foam-Dedicated Barrel Set with Shut-Off Nozzle: The specially designed barrel set is optimized for microcellular foam processes, improving the mixing and dispersion of gas within the polymer. The shut-off nozzle is a critical addition, preventing premature gas escape during the injection phase and maintaining the integrity of foam formation. This specialized equipment ensures controlled expansion of the polymer-gas mixture upon injection into the mold, resulting in a uniform and stable foam structure throughout the part.
Microcellular Foam Injection Molding is highly versatile and is used in a range of industries, including:
- Automotive: Microcellular foam injection molding is suitable for producing lightweight, high-performance interior trim to engine components because the reduction in part weight directly translates to improved fuel efficiency.
- Consumer Goods: The material is commonly used in consumer electronics to create strong and lightweight casings for devices like smartphones, laptops, and tablets. Its improved dimensional stability ensures that the parts fit together perfectly, while its lightweight nature enhances the portability of these devices.
- Packaging: By reducing the amount of plastic required for each package, manufacturers can lower costs and produce eco-friendly packaging solutions without sacrificing quality.
What other types of foam injection molding are available besides microcellular molding?
Foam injection molding can be classified based on the method used to create foam within the polymer. There are three methods: physical, chemical, and structural forming. The microcellular injection molding discussed in this article is a form of physical foaming, and other methods are also utilized.
Microcellular foam injection molding is undoubtedly the future of sustainable manufacturing for lightweight and high-strength products. It's poised to revolutionize industries with benefits like reduced material usage, faster cycle times, and improved dimensional stability.
Get in Touch
To learn more about how our microcellular foam injection molding process can benefit your next project, Huarong is an experienced injection molding machine manufacturer that provides complete injection machine types and customers’ injection molding partners to provide workable solutions for the future.
- Group Name: Huarong Group
- Brand: Huarong, Yuhdak, Nanrong
- Service Offerings: Injection Molding Machine, Vertical Injection Molding Machine, Injection Molding Automation
- Tel: +886-6-7956777
- Address: No.21-6, Zhongzhou, Chin An Vil., Xigang Dist., Tainan City 72351, Taiwan
- Official Website: https://www.huarong.com.tw/
Previous news : Huarong Wins 2025 Taiwan Excellence Award for Innovative Injection Molding Technology
Next news : PET Preform Manufacturer Achieves Higher Output with Advanced Injection Molding Machine