PET Preform Manufacturing: A Customer Success Story with Huarong
2024-11-20 12:06:21
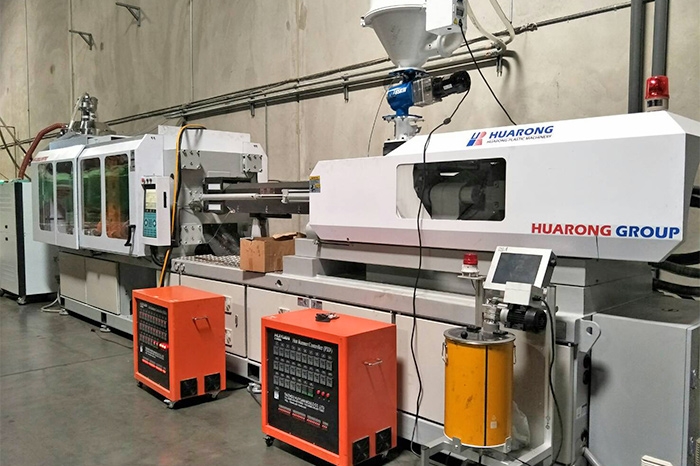
In the competitive PET preform production market, achieving excellence in quality, efficiency, and sustainability is essential. This case study highlights how a forward-thinking beverage packaging manufacturer partnered with Huarong to revolutionize their PET preform production capabilities, setting new benchmarks in performance and efficiency.
Before implementing advanced solutions, manufacturers in the PET preform industry grappled with several persistent challenges that impact their productivity and competitiveness:
Inconsistent Preform Quality
The manufacturer struggled with uneven wall thickness and crystallinity, leading to downstream issues in blow molding. These inconsistencies often resulted in rejected batches, wasting materials, and increasing costs.
Limited Production Efficiency
Their existing equipment was constrained by lengthy cycle times, frequent breakdowns, and fewer cavities per mold. This inefficiency hindered their ability to meet growing market demand.
Energy-Intensive Operations
Drying PET material efficiently while maintaining its clarity and strength was a significant energy burden. The pre-drying process consumed substantial resources, further driving up operational costs. Before processing, PET material must be carefully dried to a moisture content below 50 ppm to prevent hydrolytic degradation during molding. The drying process typically requires temperatures between 160-180°C for 4-6 hours, making it energy-intensive and time-critical.
To address these issues, the manufacturer invested in Huarong's PET Preform Injection Molding Machines. Designed for precision, efficiency, and reliability, these machines were tailored to the customer's specific needs.
Key Features of Huarong’s Solution
1. High-Performance Screw Design
Huarong's machines feature a specialized screw geometry that optimizes plasticization and ensures homogeneous melt quality. The low-shear design minimizes material degradation, enhancing clarity and strength.
2. Advanced Process Control
Real-time monitoring and intelligent control systems guarantee precise parameter adjustments, ensuring consistent quality across production runs.
3. Efficient Ejection System
The machines have an enhanced ejection mechanism that reduces cycle times and ensures smooth removal of preforms, even in high-cavity molds.
4. Integrated Dehumidification System
A top-ventilation channel and optional desiccant dryer work to maintain optimal material conditions, eliminating moisture-related defects.
5. Energy-Saving Technologies
Innovative features, such as servo-driven systems, significantly reduce energy consumption during each production cycle.
Related product: PET Injection Molding Machine – PET Series
The deployment of Huarong’s PET injection molding machine delivered impressive results across key performance indicators:
Enhanced Production Output
- 30% Increase in Capacity: Faster cycle times and optimized processes allowed the manufacturer to meet increasing market demands.
- Improved Equipment Utilization: Multi-cavity molds enabled higher throughput without compromising quality.
Superior Quality
- Reduced Scrap Rates: Advanced control systems minimized defects, ensuring consistency in weight and dimensions.
- Enhanced Preform Clarity: Optimized material handling eliminated crystallinity issues and gate vestige problems.
- Dimensional Accuracy: Stringent quality control measures met or exceeded industry standards.
Operational Efficiency
- 20% Lower Energy Consumption: Energy-efficient technologies reduced power usage while maintaining performance.
- Predictive Maintenance: Reduced downtime through intelligent diagnostics and maintenance alerts.
- OEE Improvements: Overall Equipment Effectiveness increased, streamlining the manufacturer’s operations.
The quantifiable improvements across these key performance indicators demonstrate how Huarong's advanced technology transforms PET preform production capabilities while delivering substantial cost savings and quality improvements.
Further Reading: PET Preform Molding Solution: A Detailed Guide to PET Preform Manufacturing
The manufacturer's production manager praised the transformative impact of Huarong's technology:
The success demonstrated in this case study underscores the transformative impact of partnering with the right injection molding machine manufacturer. By leveraging Huarong's advanced injection molding technology, manufacturers can achieve immediate performance improvements and long-term business benefits that position them for sustained success.
- Market Competitiveness: Enhanced production capabilities enable manufacturers to meet increasing market demands while maintaining competitive pricing and high-quality standards.
- Sustainability Achievements: Reduced energy consumption and minimized material waste align with environmental goals and deliver significant cost savings.
- Future-Ready Operations: Advanced technology integration ensures readiness for Industry 4.0 adoption and adaptability to future market requirements.
If you're looking to achieve similar breakthroughs in your PET preform production, Huarong offers tailored solutions to meet your specific needs. Contact our expert team today to explore how we can optimize your manufacturing operations and deliver sustainable growth. Schedule a consultation now to experience the difference Huarong can make in your PET preform production.
- Group Name: Huarong Group
- Brand: Huarong, Yuhdak, Nanrong
- Service Offerings: Injection Molding Machine, Vertical Injection Molding Machine, Injection Molding Automation
- Tel: +886-6-7956777
- Address: No.21-6, Zhongzhou, Chin An Vil., Xigang Dist., Tainan City 72351, Taiwan
- Official Website: https://www.huarong.com.tw/
Previous news : Microcellular Foam Injection Molding: Achieving Maximum Weight Reduction and Dimensional Stability
Next news : Plastic Bottle Cap Manufacturing: Injection Molding Technology and Applications