Injection Molding for Plastic Bottle Caps: Manufacturing Processes & Applications
2024-12-02 10:20:15
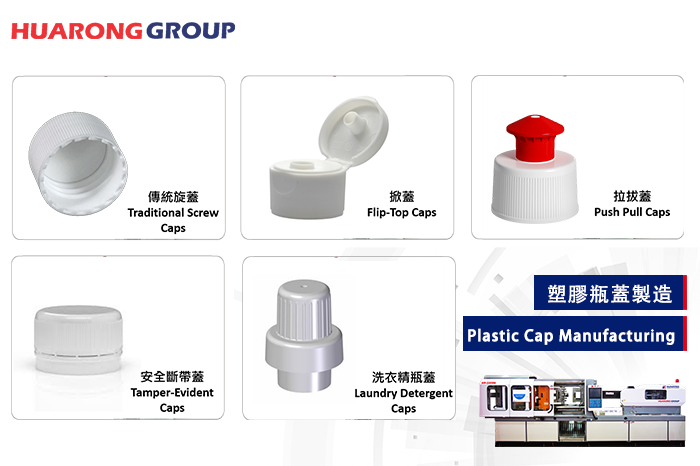
Plastic bottle caps are essential for modern packaging, offering sealing, protecting contents, and enhancing consumer convenience. As market demands become increasingly diverse, bottle caps have evolved in design, functionality, and manufacturing technology. The use of injection molding techniques allows for the production of highly efficient, precise, and versatile bottle caps that meet the needs of various industries.
Plastic bottle caps are versatile and cater to different products and consumer scenarios. Below are some common types of caps and their applications:
- Traditional Screw Caps: Commonly used for packaging mineral water and soft drinks, offering reliable sealing performance.
- Flip-Top Caps: Ideal for products that require easy pouring, such as condiment bottles and shampoo bottles, providing the convenience of single-handed operation.
- Push Pull Caps: Used in juice, milk, and other food and beverage packaging, featuring easy tear-off functionality while meeting food safety standards.
- Tamper-Evident Caps: Suitable for packaging requiring anti-counterfeiting and tamper-proofing, such as pharmaceuticals and baby food.
- Laundry Detergent Caps: Often designed with a measuring cup feature, combining sealing effectiveness with ease of use.
Whether it's traditional screw caps, flip-top caps, push-pull caps, tamper-evident caps, or laundry detergent caps, the design and functionality of bottle caps significantly influence user experience and product protection. To better understand the essential role of bottle caps in the market, this section will explore the various types of plastic bottle caps categorized by purpose, structure, and material while discussing their practical applications and unique design features across different industries.
Plastic Caps Categorized by Use
- Beverage Caps
- Applications: Sealing packages for mineral water, carbonated drinks, and juices.
- Features: Lightweight design suitable for mass production, offering excellent airtightness and leak-proof performance.
- Food Caps
- Applications: Packaging for condiments and sauces.
- Features: A combination of flip-top and screw cap designs for easy pouring, often with enhanced sealing to prevent contamination.
- Pharmaceutical Caps
- Applications: Packaging for prescription and over-the-counter medications, as well as dietary supplements.
- Features: Often include tamper-evident designs, such as safety rings, to ensure the product has not been opened.
- Cosmetic Caps
- Applications: Packaging for skincare, lotions, perfumes, and high-end cosmetics.
- Features: Premium design focusing on aesthetics and ease of use, sometimes paired with spray heads or droppers.
- Industrial Caps
- Applications: Suitable for motor oils, detergents, and industrial liquids like cleaning agents.
- Features: High chemical resistance with functional designs, often including measuring cup features for convenience.
Plastic Caps Categorized by Structure
- Screw Caps
- Applications: Most commonly used in food and beverage packaging.
- Features: Simple to operate, stable structure, suitable for high-precision injection molding.
- Flip-Top Caps
- Applications: Ideal for condiments, shampoos, and other quick-use scenarios.
- Features: Convenient single-handed operation with complex internal structures requiring precision molds.
- Tamper-Evident Caps
- Applications: Common in food and pharmaceutical packaging.
- Features: Tamper-proof design ensures product safety and integrity.
- Leak-Proof Caps
- Applications: Used for industrial or specialty liquid packaging.
- Features: Incorporates internal sealing rings to enhance leak prevention.
- Multi-Functional Caps
- Applications: Examples include measuring cup caps for laundry detergents and sieve caps for condiments.
- Features: Additional features enhance usability and convenience.
Plastic Caps Categorized by Sealing Type
- Conical Seals
- Structural Features: The key to conical seals lies in the annular conical sealing ring located on the inside top of the bottle cap. This sealing ring is specially designed to extend into the bottleneck and create an interference fit with the inner neck surface (an interference fit ensures a tight contact between the sealing ring and bottleneck, applying a small amount of compression).
- The sealing ring is designed to have flexibility, allowing it to adhere tightly to the inner surface of the bottleneck.
- When the cap is screwed on, the sealing ring generates radial compression, filling any potential gaps and achieving an airtight seal.
- Derivative Structure - Sealing Needle Design: In specific applications requiring controlled fluid or liquid dispensing, the concept of the conical sealing ring is adapted into a cylindrical sealing needle.
- The sealing needle, positioned at the center of the cap, has a conical shape and directly inserts into the outlet upon tightening, ensuring an interference fit to create a secure seal.
- This design is often employed for small outlet containers or specialized liquid dispensing systems.
- Applications: Conical seals, such as condiment bottles or specific industrial liquid containers, are commonly used in liquid packaging requiring high sealing performance.
- Structural Features: The key to conical seals lies in the annular conical sealing ring located on the inside top of the bottle cap. This sealing ring is specially designed to extend into the bottleneck and create an interference fit with the inner neck surface (an interference fit ensures a tight contact between the sealing ring and bottleneck, applying a small amount of compression).
- Liner Seals
- Structural Features: Liner seals rely on an elastic gasket inside the bottle cap. This gasket is compressed against the container opening by the cap structure to complete the seal.
- Common materials for the gasket include PE/EVA foam, silicone, and rubber, offering flexibility and durability for a wide range of applications.
- Applications: Liner seals are ideal for packaging that requires frequent opening and resealing while maintaining leak-proof integrity, such as cosmetics and food products.
- Structural Features: Liner seals rely on an elastic gasket inside the bottle cap. This gasket is compressed against the container opening by the cap structure to complete the seal.
Further reading: The Science Behind Plastic Caps: How are Plastic Bottle Caps Made
Injection molding machines are at the core of bottle cap production, enabling high-precision and fast production processes. Key benefits include:
- Precision and Consistency: Controls temperature, pressure, and cooling to ensure uniformity in dimensions and quality, which is critical for standard bottle caps.
- Multi-Cavity Molds: Allows simultaneous production of multiple caps in one cycle, significantly increasing efficiency and reducing costs.
- Material Selection and Performance:
Common injection molding materials include polypropylene (PP) and polyethylene (PE), which are characterized by their lightweight properties, chemical resistance, and high toughness, making them suitable for various bottle cap applications.- Lightweight Design: By reducing material usage, environmental impact is minimized, and costs are saved.
- Addition of Functional Materials: Examples include anti-slip surfaces, UV resistance, or antibacterial materials.
- Automation and Inspection: Automated systems handle demolding, band cutting, and labeling, ensuring consistent quality and 100% inspection for defects.
Recommend machine: General Injection Molding Machine – HRN Series
Although Huarong is a professional injection molding machine manufacturer, we also provide turnkey solutions to meet customers' injection molding needs. When customers require molds, it is essential to understand their detailed expectations and product requirements:
Design Details for Plastic Caps
- The shape of the bottle cap (e.g., screw caps, flip-top caps, tamper-evident caps).
- Special features required (e.g., tamper-evident rings, sealing rings, leak-proof designs).
- Product dimensions (e.g., 28mm, 30mm, 38mm—commonly used in international standard packaging), thickness, and tolerance requirements.
- Appearance preferences (e.g., glossy finish, matte finish, anti-slip texture).
Application Scenarios of Plastic Caps
- Types of contents the cap will be used for (e.g., beverages, food, pharmaceuticals, industrial liquids).
- Whether the cap needs to withstand high temperatures, corrosion, or UV exposure.
International Standards for Plastic Caps
- Does the product need to comply with specific international standards (e.g., ISO, FDA, CSD, GB, food-grade certifications)?
Mold Cavity Count and Functionality Design
- What is the customer's approximate production demand? (High production volumes suggest using multi-cavity molds to improve efficiency.)
- Does the mold require a hot runner system to reduce waste and improve molding quality?
- Are specific demolding mechanisms needed (e.g., automated internal thread demolding, pneumatic ejection)?
Manufacturers face several challenges in cap production:
- Dimensional Stability: To address shrinkage and deformation during the cooling process, precise control of mold temperature and material flow can enhance stability.
- Production Efficiency: Using all-electric injection molding machines or efficient hydraulic servo systems can improve production capacity per minute while reducing energy consumption.
- Environmental Requirements: Increasing the use of renewable or biodegradable materials aligns with market demands for green packaging.
Plastic bottle caps hold a significant position in the packaging industry. Among them, water caps and oil caps are two commonly used categories. Below is a detailed explanation of their structural designs and applications.
Innovative Designs for Water Caps
Type | Applications | Features | Advantages |
---|---|---|---|
Traditional Screw Cap (PCO Standard) | Mineral water, carbonated drinks | Inner conical sealing structure provides excellent airtightness, suitable for carbonated and still beverages | Lightweight design, reduces plastic usage, high pressure resistance |
Tear-Off Cap | Sports drinks, on-the-go beverages | Ring-pull design allows quick opening, single-use to prevent tampering | Easy to use, no need to unscrew after opening, suitable for outdoor activities |
Pierceable Cap | Children’s water, outdoor bottles | Includes a thin film seal that can be pierced with a straw or puncture device | Hygienic and convenient, minimizes contact between contents and external environment |
Bulk Water Cap | 18.9L or 20L water bottles | Features piercing film or valve, compatible with automated water dispensers | Automated operation, reliable sealing, ideal for large-capacity water requirements |
Advanced Features of Oil Caps
Type | Applications | Features | Advantages |
---|---|---|---|
Screw Cap | Large-capacity oil bottles (e.g., 1L or 5L cooking oil) | Inner liner seal or conical sealing structure ensures no leakage | Stable structure, suitable for long-term storage |
Flip Top Cap | Small bottles of flavor oils (e.g., olive oil, sesame oil) | One-handed operation flip design with inner flow control spout | Convenient, ideal for kitchen use |
Pour Spout Cap | Premium olive oil, cooking oil | Embedded pouring spout with anti-drip design for controlled pouring | Enhances user experience, prevents overpouring or spillage |
Tamper-Evident Cap | High-value edible oils or chemical oils | Includes safety ring that breaks upon opening, preventing unauthorized access | Ensures product safety and brand trust |
Water and oil caps often follow international standards to ensure compatibility with common container designs and meet global market requirements. These standards facilitate production, enhance usability, and maintain consistency across industries. Below is an overview of the essential international standards for water caps and oil caps:
Global Standards for Water and Oil Bottle Caps
Category | Standard Size/Type | Applications | Key Features |
---|---|---|---|
Water Caps | PCO 1810/1881 | Bottled water, carbonated drinks | 28mm diameter; PCO 1881 is a lightweight version reducing material usage while maintaining sealing performance. |
30/25 Neck Finish | Still water bottles | 30mm diameter; designed for lightweight caps to support environmental sustainability. | |
38mm Standard | Larger water bottles (e.g., 1.5L and above) | Larger opening for high-flow requirements, ensuring user convenience. | |
5-Gallon Caps | Bulk water containers (18.9L or 5-gallon) | Standardized for compatibility with automated water dispensers. | |
Oil Caps | 29/21, 38/23, 48mm | Edible oil bottles (small and medium sizes) | Suitable for consumer-friendly edible oil packaging; offers tamper-evident features. |
63mm | Larger edible oil jugs (2L–5L) | Wide-mouth design for easy pouring and dispensing. | |
DIN 45 | Industrial oils, motor oils, lubricants | 45mm diameter; standardized threading ensures leak-proof sealing for transport and storage. | |
Specialized Closures | Bulk oil containers | Large openings (63mm+), often equipped with tamper-evident and flow-control features. |
Integrating injection molding technology in plastic bottle cap production enables manufacturers to meet design requirements while ensuring efficiency and high quality. The industry is moving towards lighter, eco-friendly, smarter designs with innovative materials. Manufacturers must collaborate with reliable equipment suppliers and expert mold designers to stay competitive. If you have any inquiries, please feel free to contact Huarong.
- Group Name: Huarong Group
- Brand: Huarong, Yuhdak, Nanrong
- Service Offerings: Injection Molding Machine, Vertical Injection Molding Machine, Injection Molding Automation
- Tel: +886-6-7956777
- Address: No.21-6, Zhongzhou, Chin An Vil., Xigang Dist., Tainan City 72351, Taiwan
- Official Website: https://www.huarong.com.tw/
Previous news : PET Preform Manufacturer Achieves Higher Output with Advanced Injection Molding Machine
Next news : Custom Injection Molding for Complex Designs: Turning Ideas Into Reality