Multi Injection Molding: Advanced Configurations & Applications for Modern Manufacturing
2024-12-11 10:09:08
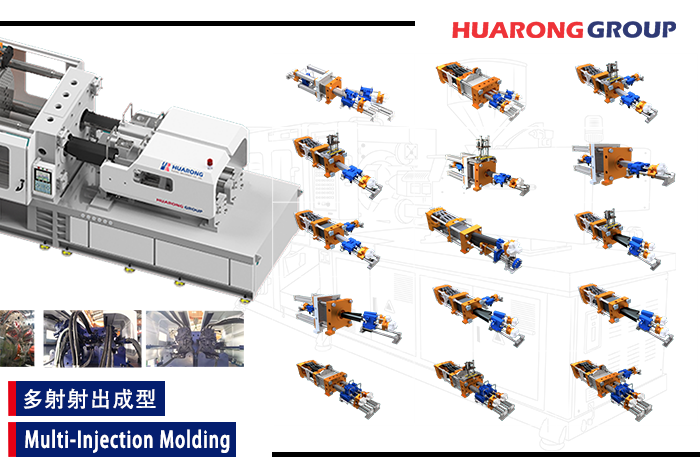
Multi Injection Molding, also known as multi-color or multi-material injection molding, is revolutionizing industries by combining two or more materials into a single product in one production cycle to enable complex, high-precision parts manufacturing. In this article, we explore its configurations, advantages, and real-world applications.
Multi-injection molding utilizes injection molding machine with multiple injection units to mold two or more injection molding materials into a single component. These units can operate sequentially or simultaneously, depending on the design requirements. This technique enables the integration of materials with contrasting properties, such as rigidity and elasticity, or different colors, creating functional and visually appealing products.
Principles of Multi Injection Molding
This process revolves around precision and coordination, ensuring that multiple materials or colors are injected seamlessly. Here’s a breakdown of the main steps involved:
- Selecting materials with compatible properties is critical for ensuring a strong bond between different layers or sections. Incompatible materials may lead to delamination or weak spots in the finished product.
- Common combinations include rigid plastics with elastomers or materials with contrasting thermal and mechanical properties.
Each injection unit operates with independent temperature and pressure settings tailored to the specific material being used. This ensures optimal flow, bonding, and curing for each layer.
- Molds for multi-injection molding are more complex than those for single-material molding. They feature mechanisms like rotating cores or sliding plates to position the part for subsequent material injections.
- The mold design incorporates separate zones for each material, ensuring the materials flow into the intended sections without overlap or distortion. This is essential for parts with distinct functional or aesthetic areas.
Multi-injection molding units come in several configurations, each designed to cater to specific manufacturing needs. Below are the key configurations commonly used in multi-injection molding:
Related machine: Multi Injection Machine
Parallel Configuration (P Type)
In this setup, the injection units are positioned side-by-side on the machine.
- Compact design, suitable for machines with space constraints.
- Facilitates simultaneous injection of multiple materials for high-speed production.
Side + Top Unit Configuration (L Type)
The injection unit has one horizontal type and one vertical type and is installed above a fixed platen or a moving platen, which can be adjusted according to customer needs.
Side + Back Unit Configuration (T Type)
This setup pairs a side-mounted injection unit with a back-mounted unit positioned at the rear of the machine.
Rotating Configuration
This setup incorporates a rotating platen or core that moves the part between different injection positions for subsequent material additions.
- Enables the creation of complex, multi-layered designs.
- Reduces cycle time by allowing simultaneous operations for different parts of the process.
Opposite Configuration (In-Line Configuration)
Both injection units are aligned in a straight line along the horizontal axis of the machine.
- Ideal for molds requiring uniform material flow from opposite directions.
- Supports symmetrical part designs and prevents material imbalances.
Piggyback Configuration (Side + Oblique Unit Configuration)
In this setup, one injection unit is mounted on top of or directly behind another, creating a compact over-and-under arrangement.
- Compact design, saving floor space.
- Enhanced flexibility for molds with unique geometries.
Multi-injection molding is revolutionizing manufacturing with its numerous advantages, enabling companies to innovate and optimize production processes.
- Design Flexibility
- Multi-injection molding allows for the creation of intricate designs, such as soft-touch grips, dual-layer components, and multi-colored parts, all in a single production cycle.
- Eliminates the need for secondary assembly, streamlining production and reducing lead times.
- Cost Efficiency
- By combining multiple production steps into one seamless process, manufacturers save on labor costs, raw materials, and assembly time.
- Minimizes production errors and reduces waste, further driving down costs.
- Enhanced Product Durability
- The integration of materials with complementary properties enhances product strength, resilience, and longevity.
- Ensures better performance under stress, making it ideal for high-demand applications like automotive and medical devices.
- Sustainability
- Reduces material waste by utilizing precise injection techniques and recycling capabilities.
- Facilitates the use of eco-friendly materials, including recycled plastics and bio-based polymers, aligning with green manufacturing goals.
This technology’s versatility makes it a preferred choice in many industries:
- Automotive
- Enables the creation of multi-colored dashboards, ergonomic handles, and functional switches that combine durability with aesthetic appeal.
- Improves safety and comfort through advanced material integration, such as soft-touch surfaces for steering wheels and control panels.
- Medical Devices
- Facilitates the production of biocompatible instruments, including surgical tools and diagnostic devices, with multi-material designs for precision and usability.
- Ensures compliance with stringent medical regulations while enhancing device performance.
- Consumer Electronics
- Ideal for products like smartphone cases, wearable devices, and gadget housings, where rigid and flexible materials must be integrated seamlessly.
- Elevates user experience with enhanced durability and sleek designs.
- Consumer Goods
- Supports the development of high-quality household items, such as ergonomic kitchen tools, durable toys, and multi-material appliance components.
Success Stories with Our Multi Injection Molding Machines
- Dual-Material Hair Clip
- Dual-Material Headphone Outer Cases
- Dual-Material Car Light
- Explore the HDC 160 Cap (White+Blue) details in our YouTube video.
- Dual-Color Cap
- Explore the Dual Color Headlight details in our YouTube video.
- Dual-Color Storage Box
- Explore the Two Color Storage Box details in our YouTube video.
- Dual-Material Toothbrush Handle
- Explore the Toothbrush Handle details in our YouTube video.
- Dual-Material Oil Seal
- Explore the HDC- 300SS (TPV+PP) Oil Seal details in our YouTube video.
- Dual-Material Anti-Collision Protective Strip
- Explore the Anti-Collision Protective Strip details in our YouTube video.
The future of multi-injection molding lies in leveraging advanced technologies and sustainable practices to push boundaries in manufacturing:
- Industry 4.0 Integration
- AI-driven process optimization ensures consistent quality and efficient resource use.
- Real-time monitoring and predictive maintenance reduce downtime, enabling manufacturers to meet tight production schedules.
- Sustainability Trends
- Energy-efficient machines and innovative molding techniques lower environmental footprints.
- Increased adoption of recycled and bio-based materials supports global sustainability goals.
- Enhanced Customization
- Advances in mold design and material science will allow manufacturers to produce increasingly complex, customizable parts tailored to specific market needs.
- Digital twin simulations and data analytics will enable faster prototyping and reduced time-to-market.
- Market Adaptation
- As industries grow more competitive, adopting multi-injection molding helps businesses adapt to changing consumer demands and market trends.
Multi-injection molding is not just a manufacturing innovation; it's a strategic advantage for businesses aiming to stay competitive. With its unparalleled design flexibility, cost efficiency, and support for sustainability goals, this technology is shaping the future of production.
Ready to transform your production line?
Connect with Huarong, we are an experienced injection molding machine manufacturer in Taiwan, today and discover how multi-injection molding can drive efficiency, innovation, and sustainability for your business. If you have any inquiries, please feel free to contact Huarong.
- Group Name: Huarong Group
- Brand: Huarong, Yuhdak, Nanrong
- Service Offerings: Injection Molding Machine, Vertical Injection Molding Machine, Injection Molding Automation
- Tel: +886-6-7956777
- Address: No.21-6, Zhongzhou, Chin An Vil., Xigang Dist., Tainan City 72351, Taiwan
- Official Website: https://www.huarong.com.tw/
Previous news : Custom Injection Molding for Complex Designs: Turning Ideas Into Reality
Next news: Vertical Injection Moulding Machine Specifications Explained: A Buyer's Guide