Vertical Injection Moulding Machine Specifications Explained: A Buyer's Guide
2024-12-18 17:28:29
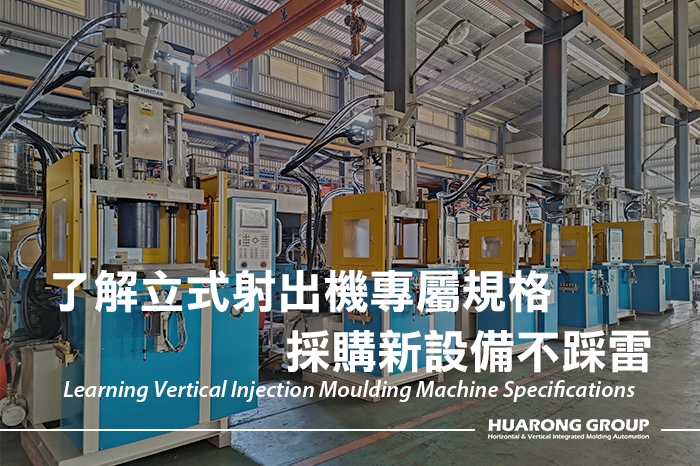
Vertical injection moulding machine specification is a crucial aspect for manufacturers seeking to invest in new equipment for precision moulding applications. From electronic components to automotive parts, the right machine specifications can significantly impact production efficiency, product quality, and overall operational cost. In this guide, we will delve deep into understanding vertical injection moulding machine specifications, their unique features, and how to choose the right machine tailored to your needs.
Vertical injection moulding machines are designed with the injection and clamping units positioned vertically. This configuration is particularly advantageous for insert moulding, overmoulding, and applications requiring precise component placement. Unlike horizontal machines, vertical machines offer a compact footprint, making them ideal for factories with limited space. They are widely used across industries for their flexibility and capability to handle complex moulding tasks with high precision.
Understanding the core principles and advantages of vertical injection moulding machines lays the foundation for evaluating their specifications and unique features. Let's dive into the critical technical aspects to consider when choosing a machine.
Further reading: Comprehensive Guide to Vertical Injection Molding Machines
Below, we'll explore the injection unit, clamping unit, and power unit specifications.
Injection Unit Specifications
The injection unit determines the injection molding material flow and the quality of the final product. Key parameters to evaluate include:
Specification | Unit | Description |
Screw Diameter | mm | Determines the throughput and compatibility with different mould sizes. |
Injection Pressure | kgf/cm² | The force used to inject material into the mould, ensuring uniform filling and product quality. |
Injection Capacity | cm³ | Maximum volume of material the machine can inject in one cycle. |
Max. Injection Weight (PS) | gr/oz | The weight of polystyrene that can be injected in one shot, indicating material flexibility. |
Injection Rate | cm³/sec | Speed at which material is injected, influencing cycle time and production efficiency. |
Injection Speed | mm/s | The velocity of the injection process, critical for moulding precision and thin-wall parts. |
Heater | kW | Energy required to heat the material, affecting operational costs and process consistency. |
Clamping Unit Specifications
The clamping unit ensures that the mould remains securely closed during the injection process. Important specifications include:
Specification | Unit | Description |
Clamping Force | tf | Maximum force applied to keep the mould closed and prevent flash during injection. |
Clamping Stroke | mm | The distance the mould plates can travel to open or close. |
Max. Open Distance | mm | The maximum gap between the plates when fully opened, suitable for different mould heights. |
Min. Mold Height | mm | Minimum height of the mould that can be accommodated. |
Hydraulic Ejector Force | tf | The force applied to eject the finished part from the mould. |
Ejector Stroke | mm | The range of movement for ejecting parts, essential for moulding larger or complex products. |
Mould Unit Specifications
Vertical injection moulding machines often feature advanced mould systems like sliding and rotary tables. Here are the key specifications:
Specification | Unit | Description |
Max. Mold Size | mm | The largest mould dimensions that can fit the machine, critical for compatibility. |
Slide Dimension | mm | Dimensions of the sliding table, used for insert moulding operations. |
Rotary Diameter | mm | The diameter of the rotary table, allowing multi-station operations for enhanced efficiency. |
Power Unit and Other Specifications
The power unit and auxiliary specifications influence the machine's energy efficiency and operational convenience. These include:
Specification | Unit | Description |
Drive Motor | kW (hp) | Power rating of the main motor, impacting machine performance and energy usage. |
Oil Tank Capacity | L | Volume of hydraulic oil the machine can hold, ensuring smooth operation. |
Dimension of Machine | L (m) x W (m) x H (m) | Overall size of the machine, important for factory layout planning. |
Weight of Machine | T | Total weight of the machine, relevant for transport and installation considerations. |
Further reading: Injection Molding Machine Specifications: What to Look For When Choosing the Right Equipment
Vertical injection moulding machines stand out for their distinct features that cater to specialized manufacturing needs. Below, we'll explore the unique advantages that make these machines a preferred choice for many applications.
Insert Moulding Advantages
Vertical machines excel in insert moulding, allowing for easy placement of components into the mould before injection. This capability ensures accurate positioning and eliminates the risk of movement during the moulding process, resulting in high-quality, integrated products.
Rotary Table and Multi-Station Configurations
Rotary tables and multi-station setups are common in vertical machines, enabling simultaneous operations such as moulding, cooling, and ejection. These features significantly boost productivity and are ideal for complex, high-volume production.
Compact Design for Space Efficiency
The vertical configuration offers a smaller footprint compared to horizontal machines, making them suitable for facilities with space constraints. Despite their compact design, these machines maintain robust performance and versatility.
Vertical injection moulding find extensive applications across various industries. Let's look at the most common use cases that showcase their versatility.
Electronics and Precision Components
From cables to light bulb housings, vertical machines are widely used in the electronics industry for producing high-precision, small-scale components. Their ability to handle intricate designs and tight tolerances makes them indispensable for this sector.
Overmoulding and Multi-Material Production
Vertical machines are ideal for overmoulding processes, where multiple materials are combined to create a single product. Common examples include dual-material bicycle pedals, tool handles, and automotive grips.
Further reading: A Success Story with Huarong's Vertical Injection Machine: Enhancing Precision and Efficiency
Further reading: How Our Vertical Injection Machines Produce High-Quality Tubes for CPAP | Success Story
Choosing the right vertical injection moulding machine specification isn't just about immediate needs; it's also about ensuring long-term value. Matching machine capabilities with production requirements can reduce waste, enhance operational efficiency, and improve product consistency. Additionally, investing in machines with energy-efficient designs and automation options can lead to significant cost savings over time.
By evaluating injection, clamping, and power unit parameters, along with unique machine features, you can select a machine that aligns with your manufacturing goals. Ready to take your production efficiency to the next level? Contact Huarong, an industry-leading injection molding machine manufacturer, to explore our range of high-performance vertical injection moulding machines, and find the perfect fit for your needs.
- Group Name: Huarong Group
- Brand: Huarong, Yuhdak, Nanrong
- Service Offerings: Injection Molding Machine, Vertical Injection Molding Machine, Injection Molding Automation
- Tel: +886-6-7956777
- Address: No.21-6, Zhongzhou, Chin An Vil., Xigang Dist., Tainan City 72351, Taiwan
- Official Website: https://www.huarong.com.tw/
Previous news : Multi Injection Molding: Advanced Configurations & Applications for Modern Manufacturing