How to Repair an Injection Molding Machine: A Step-by-Step Guide
2025-01-15 11:03:48
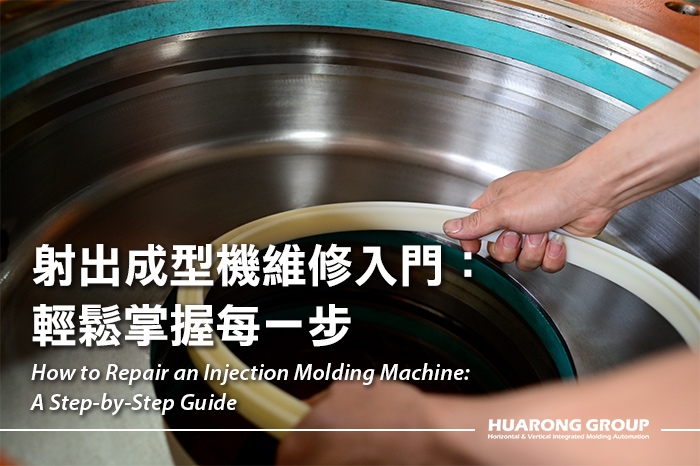
Injection molding machines play a pivotal role in manufacturing, enabling the production of diverse plastic products with accuracy and efficiency. However, as with any sophisticated equipment, they are prone to issues that can disrupt operations and affect productivity. This article offers actionable insights on repairing an injection molding machine to keep it functioning smoothly.
Injection molding machines may encounter a variety of issues, including:
- Hydraulic System Failures:
- Insufficient hydraulic pressure can lead to incomplete molding or poor clamping force.
- Oil leaks, often caused by worn-out seals or damaged hoses, can affect machine performance and create safety hazards.
- Malfunctioning pumps or motors may result in erratic movements or complete operational failure.
- Electrical Control Issues:
- Sensor failures can disrupt feedback loops, leading to inaccuracies in mold positioning or temperature control.
- Control panel malfunctions, such as unresponsive touchscreens or incorrect error codes, can make troubleshooting challenging.
- Wiring problems, including loose connections or insulation damage, may cause intermittent faults or machine shutdowns.
- Mechanical Wear and Tear:
- Screws and barrels, subjected to high pressure and friction, can become worn over time, leading to poor material mixing or reduced output quality.
- Molds may develop cracks or deformation, particularly under high-stress production conditions.
- Tie bars and toggle mechanisms can suffer from fatigue, compromising clamping force and alignment.
- Heating System Problems:
- Malfunctioning heating bands can result in uneven barrel temperatures, causing inconsistencies in material flow.
- Unstable temperature control may stem from faulty thermocouples or damaged controllers, impacting product quality.
- Overheating due to insufficient cooling can lead to thermal degradation of materials and increased downtime.
- Clogging and Contamination:
- Residual material buildup in the barrel or mold can lead to defects in molded parts and reduce cycle efficiency.
- Contamination from degraded polymers or foreign particles can cause nozzle blockages and affect overall performance.
Identifying these problems early through routine inspections and monitoring can prevent extensive damage and costly repairs. By understanding these common issues, operators can implement targeted solutions to maintain optimal machine performance.
Before starting any repair work, follow these steps to ensure safety and efficiency:
- Shut Down the Machine: Disconnect the power supply and allow the machine to cool down. This step prevents accidental starts and reduces the risk of burns or electrical shocks during the repair process.
- Gather Necessary Tools: Assemble essential tools such as wrenches, multimeters, lubricants, cleaning supplies, and any specific replacement parts that might be needed. Having all tools within reach reduces downtime and ensures smoother repairs.
- Consult the Manual: Refer to the machine’s operation manual for detailed troubleshooting guidelines and part specifications. This will help you identify the correct procedures and avoid unnecessary damage.
- Assess Workplace Safety: Ensure the repair area is well-lit, spacious, and free from obstructions. Use protective gear such as gloves, safety goggles, and steel-toed boots to minimize risks during repairs.
- Check Spare Parts Availability: Verify that you have the necessary spare parts in stock, especially for components prone to frequent wear, like seals, screws, and filters. Ordering parts in advance can prevent prolonged machine downtime.
- Communicate with the Team: Inform all relevant personnel about the repair schedule to avoid interruptions or accidental operations. Establish clear communication to coordinate tasks efficiently.
Thorough preparation not only ensures safety but also streamlines the repair process, allowing for quicker problem resolution and a faster return to production.
Follow these steps to repair your injection molding machine effectively:
1. Diagnose the Problem
- Observe error codes on the control panel.
- Listen for unusual noises or vibrations.
- Inspect the machine for visible signs of damage.
- Use diagnostic tools like multimeters or hydraulic pressure gauges for a detailed analysis.
2. Clean and Inspect
- Remove residual material from the hopper, barrel, and mold.
- Check for worn-out parts, loose connections, or leaks.
- Inspect critical components like toggle mechanisms and tie bars for cracks or misalignment.
3. Replace Damaged Components
- Replace consumable parts such as screws, nozzles, or heating elements.
- Upgrade outdated components, if necessary, to improve machine efficiency.
- Verify that all replacements are installed securely and calibrated correctly.
4. Test and Calibrate
- Restart the machine and conduct a test run.
- Monitor the machine’s performance and adjust settings as needed.
- Document changes made during the repair for future reference.
Preventive maintenance can minimize the need for repairs and extend the machine’s lifespan:
- Regular Cleaning: Clean machine components after each production cycle to prevent buildup.
- Lubrication: Apply lubricant to moving parts to reduce friction and wear.
- Hydraulic System Checks: Replace hydraulic oil and filters periodically.
- Electrical Inspections: Check wiring and sensors regularly to avoid unexpected failures.
- Operator Training: Train staff to handle the machine correctly and identify early signs of issues.
- Schedule Routine Maintenance: Implement a maintenance calendar to systematically address wear and tear.
Further reading: Injection Molding Machine Maintenance PDF and Checklist
Proactive repairs and consistent maintenance are key to ensuring the reliability and longevity of injection molding machines. By addressing issues promptly and adhering to best practices, you can reduce downtime and maintain seamless production.
For more advanced repairs or persistent issues, professional assistance is invaluable. Huarong’s team of skilled technicians is equipped to handle complex repairs and optimize machine performance. Contact us today to ensure your injection molding operations remain efficient and trouble-free!
- Group Name: Huarong Group
- Brand: Huarong, Yuhdak, Nanrong
- Service Offerings: Injection Molding Machine, Vertical Injection Molding Machine, Injection Molding Automation
- Tel: +886-6-7956777
- Address: No.21-6, Zhongzhou, Chin An Vil., Xigang Dist., Tainan City 72351, Taiwan
- Official Website: https://www.huarong.com.tw/
Previous news : Common Injection Molding Defects: Causes, Types, and Solutions
Next news : Automotive Injection Molding: What You Need to Know