Thermoplastic Injection Molding Explained: How It Works & Why It’s Essential
2025-02-07 14:43:07
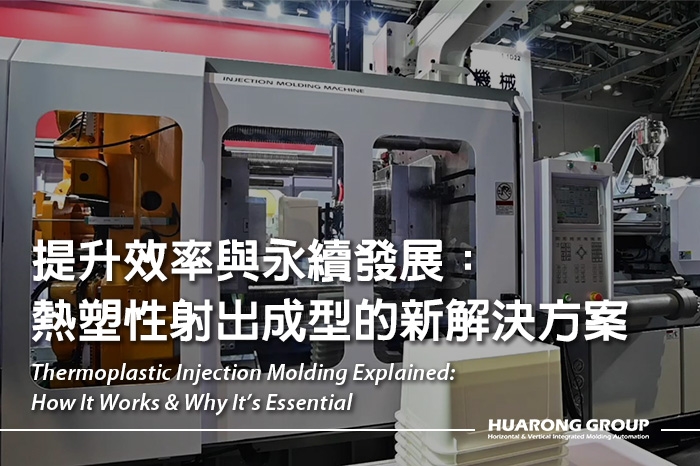
Thermoplastic injection molding is a highly efficient and versatile manufacturing process, enabling the mass production of complex plastic components across automotive, consumer electronics, medical devices, and packaging industries. This guide explores thermoplastic injection molding, detailing its process, key materials, advantages, and how Huarong's innovative technology transforms the industry.
Thermoplastic injection molding is a widely adopted manufacturing method that involves melting thermoplastic materials, injecting them into a high-precision mold cavity, and allowing them to cool and solidify into accurate, durable plastic parts. Unlike thermoset plastics, which cannot be reshaped after molding, thermoplastics are fully recyclable and can be reheated and remolded multiple times, making them a sustainable choice for various industries.
Key Benefits of Thermoplastic Injection Molding
Thermoplastic injection molding is highly scalable, enabling high-volume production with precision and minimal defects. It supports complex geometries, offers material versatility, and accommodates high-strength, heat-resistant, and flexible plastics. The process is eco-friendly, as thermoplastics can be recycled and reused, reducing waste. Additionally, its cost-effectiveness stems from automation, rapid cycle times, and minimal material loss, making it an efficient and sustainable manufacturing solution.
The thermoplastic injection molding process follows a highly controlled series of steps to ensure consistent part quality and production efficiency.
- Material Preparation
- Raw thermoplastic pellets are loaded into the hopper.
- The material moves into a heated barrel, where it starts to soften.
- Melting and Homogenization
- A reciprocating screw inside the barrel rotates, applying heat and shear forces to the pellets.
- The material reaches a molten, uniform state, ensuring consistent part formation.
- Injection into the Mold
- The molten thermoplastic is injected into a precision-engineered mold cavity at high pressure.
- This step ensures that even the smallest details are captured in the final product.
- Cooling and Solidification
- The injected material gradually cools, conforming to the mold's exact shape.
- A temperature-controlled cooling system accelerates cycle time and prevents defects.
- Ejection of the Molded Part
- Once fully solidified, the mold opens, and ejector pins release the finished part.
- Excess material, such as sprues or runners, is trimmed and often recycled.
- Repeat Cycle
- The mold closes, and the cycle repeats, allowing for continuous, high-speed production.
Further reading: What is Injection Molding? Processes, Benefits, and Applications
Different thermoplastic polymers offer unique mechanical, thermal, and chemical properties for various applications.
Material | Key Properties | Applications |
---|---|---|
Polyethylene (PE) | Flexible, chemical-resistant | Packaging, containers, medical tubing |
Polypropylene (PP) | Tough, fatigue-resistant | Automotive parts, reusable containers |
Acrylonitrile Butadiene Styrene (ABS) | Strong, impact-resistant | Electronic housings, automotive components |
Polyamide (Nylon) | High strength, wear-resistant | Gears, bearings, structural parts |
Polycarbonate (PC) | Transparent, impact-resistant | Eyewear lenses, safety shields |
Polyvinyl Chloride (PVC) | Weather-resistant, rigid | Pipes, construction materials |
Further reading: Understanding the 10 Most Common Injection Molding Materials
Huarong's cutting-edge injection molding machines provide innovative solutions for high-precision, sustainable manufacturing.
Further reading: Understanding Injection Molding Machine Types: Advantages and Disadvantages of 7 Popular Models
1. HRN Toggle Injection Molding Machine
The HRN Toggle Injection Molding Machine is designed for high precision and durability, ensuring consistent molding quality. It is especially suitable for applications demanding accuracy and longevity. Its robust mechanical structure and superior performance make it a top choice for many customers.
- High-precision molding with tight dimensional tolerances
- Durable mechanical structure for long-term performance
- Ideal for high-volume production requiring consistency
Related product: Toggle Injection Molding Machine - HRN Series
2. NRH Two-Platen Injection Molding Machine
Renowned for its space-saving design, the NRH Two-Platen Injection Molding Machine is ideal for facilities with limited floor space but requiring high-pressure molding. Additionally, the NRH machine supports the production of medium to large thermoplastic products, offering exceptional flexibility for larger molds.
- Compact design saves factory space
- Optimized for large thermoplastic components
- Supports high-pressure molding for more substantial plastic parts
Related product: Two-Platen Injection Molding Machine - NRH Series
Microcellular foaming technology enhances traditional injection molding by introducing a precisely controlled gas into the polymer. This creates a uniform cell structure, offering several key performance and sustainability benefits.
Related feature: Microcellular Foam Injection Molding Technology
Key Benefits of Microcellular Injection Molding
- Reduces part weight by 15-20% while maintaining strength
- Lowers injection pressure, extending mold lifespan
- Minimizes cycle times, boosting production efficiency
- Reduces energy consumption, lowering carbon footprint
- Enhances product durability and impact resistance
Further reading: Microcellular Foam Injection Molding: Achieving Maximum Weight Reduction and Dimensional Stability
Huarong is at the forefront of thermoplastic injection molding innovation, offering solutions that combine efficiency, quality, and sustainability.
Our Competitive Edge
- Industry-Leading Machine Technology – Several injection machine types optimized and customized solutions for high-precision and manufacturing needs
- Sustainable Manufacturing Solutions – Microcellular foaming for reduced waste and energy consumption
- ISO-Certified Quality Standards – Ensuring consistent, reliable production
- Smart Factory & Automation Integration – Enhancing efficiency and cost savings
Related product: Innovative Injection Molding Machines | HUARONG GROUP
Related product: Vertical Injection Molding Machine | Insert Molding Solutions | HUARONG GROUP
Related product: Smart Factory Management - HFM System
Related product: Injection Molding Robot - Manipulator Arm
Thermoplastic injection molding is one of the most scalable, cost-effective, and precise manufacturing methods. Huarong is an experienced injection molding machine manufacturer that offers sustainable and high-efficiency plastic production equipment with advanced microcellular foaming technology and high-quality injection molding machines. Ready to optimize your injection molding process? Contact Huarong today to discover custom solutions tailored to your business needs!
- Group Name: Huarong Group
- Brand: Huarong, Yuhdak, Nanrong
- Service Offerings: Injection Molding Machine, Vertical Injection Molding Machine, Injection Molding Automation
- Tel: +886-6-7956777
- Address: No.21-6, Zhongzhou, Chin An Vil., Xigang Dist., Tainan City 72351, Taiwan
- Official Website: https://www.huarong.com.tw/
Previous news: Automotive Injection Molding: Process, Benefits, and Key Applications
Next news: Thermoset Injection Molding: Process, Benefits & Applications