Beyond Injection Molding! Analyzing Successful Transformation Through Turn-Key Automation Solutions
2025-02-20 16:15:01
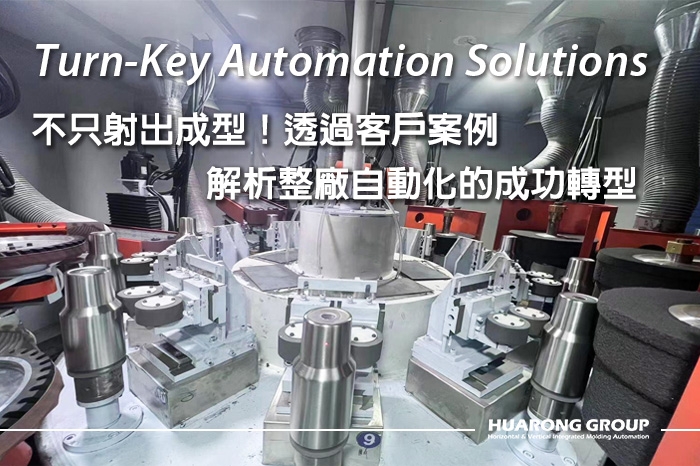
In the wave of industrial upgrades and transformation, automation and smart manufacturing have become key trends. As labor costs continue to rise and product quality demands increase, companies must seek more efficient and stable production models. Huarong has transformed from a traditional injection molding machine manufacturer into a provider of comprehensive turn-key automation solutions, helping various industries advance toward intelligent manufacturing. Today, let's explore how comprehensive factory design plays a critical role in business transformation through a successful case study of a leading insulated bottle manufacturer.
Turn-key automation is not just a trend—it is a necessary path for the future of manufacturing. Leveraging years of expertise in injection molding and automation technology, Huarong offers highly customized solutions that help clients overcome production bottlenecks, enhance efficiency, and improve competitiveness.
Market Trends: The Importance of Automation and Smart Manufacturing
As global manufacturing faces challenges such as rising labor costs, unstable product quality, and limited production capacity, more companies are focusing on smart factories and digital transformation. The changing market demands are pushing businesses to shift from manual operations to automated production to increase efficiency and quality. With years of technological expertise, Huarong not only excels in injection molding equipment but also actively invests in comprehensive factory automation planning, providing tailored solutions for diverse manufacturing industries.
Why Do Companies Need "Turn-Key Solutions"?
In a highly competitive market, a single automated device is no longer sufficient to meet diverse demands. Turn-key solutions provide a more comprehensive approach. Huarong specializes in customized factory automation designs, automating and standardizing complex production processes to fundamentally improve capacity and product quality.
Traditional production models often suffer from low efficiency and inconsistent quality, whereas intelligent manufacturing offers clear advantages in stability, efficiency, and cost reduction. Turn-key solutions address multiple production pain points simultaneously, from raw material loading, processing, and monitoring to final quality inspection. Full-process automation not only reduces human error but also significantly increases production efficiency.
A core value of turn-key solutions lies in their high customization and flexibility. Huarong provides modular equipment designs that can be adjusted as market demands change. Whether it's adding new production lines or switching product models, businesses can respond quickly. Our collaboration with a globally recognized insulated bottle manufacturer demonstrates how turn-key automation helps companies overcome bottlenecks and achieve smart manufacturing transformation.
Related feature: Automation system
This case study showcases how Huarong provided a professional and comprehensive smart automation solution to meet the customer's needs, solve production challenges, and enhance market competitiveness.
Customer Background
The customer is a globally renowned insulated bottle manufacturer with a significant international market share. Specializing in high-end stainless steel insulated bottles, their product design and quality lead the industry. However, the company's traditional production model relied heavily on manual operations, especially in key processes such as polishing, grinding, and assembly, making it challenging to maintain both production efficiency and quality consistency.
Challenges and Pain Points
The insulated bottle manufacturer faced several persistent challenges that hindered business growth:
- Inconsistent Quality: Manual polishing and grinding depend on workers' experience and skills, making it difficult to ensure consistent appearance and texture. For the high-end market, any defect directly impacts brand reputation.
- Rising Labor Costs: Polishing and grinding are labor-intensive tasks requiring skilled workers. As the labor supply shrinks, labor costs continue to rise, increasing operational pressures.
- Limited Production Capacity: Traditional manual operations cannot quickly meet large-scale order demands, resulting in extended lead times and reduced customer satisfaction.
- Environmental and Safety Concerns: Polishing and grinding generate dust and metal debris, posing health risks to workers and creating potential long-term occupational hazards.
Further reading: 4 Core Innovations in Revolutionary Double-Shot Hairpins Automated Technology by Huarong
Huarong's professional technical team tailored a comprehensive smart polishing and grinding automation solution to meet the customer's specific needs, driving intelligent production and efficiency improvements.
Solutions to Address Challenges
We designed a complete smart polishing and grinding production line for the customer, including:
- Automatic Feeding: Reducing manual intervention and improving accuracy and speed, with a precise positioning system ensuring each insulated bottle is accurately delivered to the processing station, minimizing misalignment and delays.
- Top and Bottom Edge Correction: Automated sensors detect and correct minor deformations on the bottle's top and bottom edges, ensuring product shape consistency.
- Surface Sanding: Multi-axis robotic arms control grinding tools for uniform surface sanding, achieving high-end product standards while preventing over-polishing or defects.
- Base and Side Processing: An automatic calibration system precisely handles the bottle's base and side details, ensuring dimensions and appearance meet design specifications.
- Base Polishing: High-precision polishing machines ensure a smooth, burr-free finish on the bottle's base, enhancing product aesthetics and user experience.
- Cotton Wheel Polishing (Base + Body): In the final stage, a cotton wheel performs high-precision polishing on both the bottle body and base, meeting the fine quality requirements of the premium market.
Technical Highlights
- Collaborative operation of robotic arms and smart equipment enhances both processing accuracy and production speed.
- AI vision inspection technology ensures product quality and reduces errors caused by manual inspection.
- Modular design allows flexible expansion to accommodate different product models and manufacturing needs.
Further reading: Comprehensive Guide to Injection Molding Robots: Automate Your Production Process
Further reading: Assembly Robots: The Evolution and Future of Robot Assembly Lines
After implementing Huarong's smart polishing and grinding automation line, the insulated bottle manufacturer achieved significant improvements in capacity, quality, and production environment, laying a solid foundation for future market expansion.
Quantifiable Results Post-Implementation
- Increased Capacity:
- Automation significantly improves production efficiency, enabling rapid fulfillment of large orders and enhancing market competitiveness.
- Reduced Labor Dependency:
- Robotic arms and smart devices replace repetitive tasks, reducing reliance on skilled labor and lowering operational costs while enhancing process stability.
- Improved Product Consistency:
- Automated precision processing ensures consistent product quality, reducing customer complaints and increasing satisfaction.
- Reduced Dust Generation:
- Automated polishing effectively controls dust emissions, improving workplace safety and reducing occupational health risks.
- Lower Production Costs:
- Increased efficiency and reduced material waste lower overall production costs, enhancing price competitiveness.
Customer Feedback
The customer expressed high satisfaction with Huarong's smart polishing and grinding automation line, providing the following feedback:
- "After implementing the automated production line, we can respond more flexibly to market changes. Capacity has increased while maintaining stable product quality, leading to significant business growth."
- "Huarong's team is professional and responsive, providing reliable technical support throughout the entire planning and implementation process."
As the manufacturing industry moves toward digitalization and intelligence, turn-key solutions have become a crucial strategy for enhancing competitiveness. Huarong collaborates closely with clients, leveraging technical expertise to deliver customized automation solutions that facilitate smart manufacturing transformation.
Why Are "Turn-Key Solutions" the Future Trend?
- Cross-Industry Applications: Turn-key automation extends beyond the injection molding industry to areas like metal processing and electronics, enhancing efficiency and quality.
- Market Competitiveness: Automated production lines improve efficiency and reduce lead times, offering a competitive edge in diverse market demands.
- Cost and Quality Balance: Smart technology reduces labor costs, increases capacity, and ensures product quality, helping businesses maximize benefits while maintaining competitiveness.
How Can We Help Your Business Achieve Smart Manufacturing?
If your business faces similar challenges, Huarong is ready to provide professional support and customized solutions tailored to your needs.
From initial assessment to system implementation, Huarong provides full technical support, ensuring every step is completed smoothly and helping you quickly achieve smart manufacturing. Contact us today and let's move toward the future of intelligent manufacturing together!
- Group Name: Huarong Group
- Brand: Huarong, Yuhdak, Nanrong
- Service Offerings: Injection Molding Machine, Vertical Injection Molding Machine, Injection Molding Automation
- Tel: +886-6-7956777
- Address: No.21-6, Zhongzhou, Chin An Vil., Xigang Dist., Tainan City 72351, Taiwan
Previous news : Thermoset Injection Molding: Process, Benefits & Applications
Next news : PVC Injection Molding: Process, Challenges, and Best Practices