PVC Injection Molding: Process, Challenges & Best Practices (2025 Guide)
2025-02-27 15:22:01
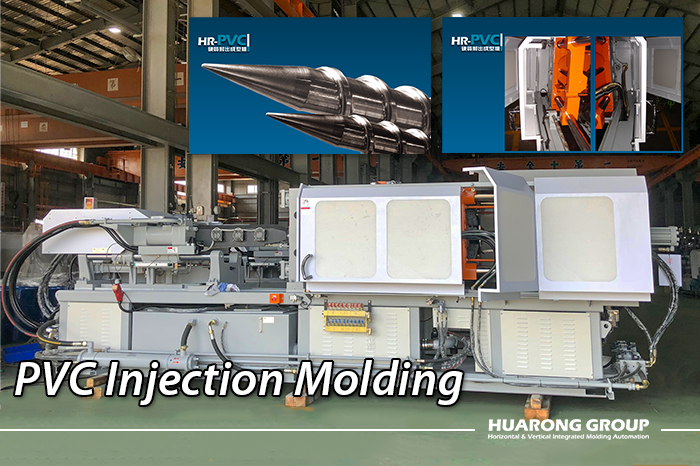
PVC injection molding enables the production of high-quality, durable plastic components with PVC’s versatility, cost-effectiveness, and chemical resistance. However, processing PVC requires specific techniques and careful considerations to ensure product quality, machine longevity, and safety. This article will explore PVC material properties, the molding process, design guidelines, and best practices.
PVC (Polyvinyl Chloride) is a widely used thermoplastic polymer available in rigid (RPVC) and flexible (FPVC) forms. PVC requires careful processing, unlike other plastics, due to its low thermal stability and potential degradation risks.
Types of PVC
- Rigid PVC (RPVC): Known for its strength and durability, it is widely used in construction materials such as pipes and window frames.
- Flexible PVC (FPVC): Softened with plasticizers, ideal for medical tubing, cable insulation, and consumer goods.
Further reading: Understanding the 10 Most Common Injection Molding Materials
Key Properties of PVC
PVC is widely used due to its unique material characteristics:
- Chemical Resistance: Resistant to acids, alkalis, and solvents.
- Electrical Insulation: Ideal for electrical applications.
- Flame Retardancy: Naturally self-extinguishing.
- Durability: High impact and tensile strength.
- Low Moisture Absorption: Ensures stability in humid conditions.
Material Properties Comparison
Property | Rigid PVC (RPVC) | Flexible PVC (FPVC) |
---|---|---|
Density (g/cm³) | 1.35 - 1.45 | 1.1 - 1.3 |
Tensile Strength at Yield (MPa) | 45 - 60 | 10 - 25 |
Elongation at Break (%) | 10 - 40 | 100 - 400 |
Flexural Modulus (GPa) | 2.4 - 4.1 | 0.01 - 0.1 |
Dielectric Constant | 3.0 - 3.8 | 3.2 - 4.0 |
Note: Values may vary based on specific PVC formulations and additives.
Applications of PVC Injection Molding
PVC injection molding is used across multiple industries:
- Construction: Pipes, fittings, and weather-resistant siding materials.
- Medical: IV bags, flexible tubing, biocompatible components.
- Automotive: Interior trims, dashboards, and sealing components.
- Consumer Goods: Footwear, toys, and household items.
Related article: Case Study: Best PVC Pipe Fitting Machine for Your Business
PVC injection molding follows a systematic approach to ensure precision and quality:
1. Material Preparation
- Pre-dry PVC resin at 60°C for 2-3 hours to avoid moisture-related defects.
- Mix PVC with stabilizers, plasticizers, and lubricants for thermal st
2. Melting and Plasticizing
- Maintain melt temperature between 170°C – 190°C to avoid degradation.
- Excessive heat leads to thermal degradation, releasing hydrochloric acid (HCl).
3. Injection
- Melted PVC is injected into the mold cavity with precise pressure control (80 - 120 MPa) to ensure uniform filling and avoid defects.
4. Cooling
- Effective mold cooling prevents warpage and shrinkage.
- Cooling time varies between 20 - 70 seconds, depending on the part thickness.
5. Ejection
- Anti-stick coatings or mold release agents help facilitate smooth part ejection.
Further reading: What is Injection Molding? Processes, Benefits, and Applications
Further reading: Thermoplastic Injection Molding Explained: How It Works & Why It’s Essential
Property | Recommended Setting |
---|---|
Melt Temperature | 170°C – 190°C |
Injection Pressure | 80 – 120 MPa (800 – 1200 bar) |
Injection Speed | Medium to High |
Mold Temperature | 20°C – 50°C |
Cooling Time | 20 – 70 seconds |
Despite its advantages, PVC requires careful handling:
1. Heat Sensitivity
- Excessive temperature degrades PVC, releasing corrosive gases.
- Maintain processing temperature below 190°C.
2. High Viscosity
- PVC's high melt viscosity complicates mold filling.
- Use higher injection pressures and well-vented mold designs.
3. Corrosion Issues
- PVC releases acidic byproducts, corroding molds and machinery.
- Chrome-plated or stainless steel molds prevent damage.
4. Moisture Absorption
- Pre-dry PVC resin to prevent defects like bubbles or voids.
- Uniform Wall Thickness: Reduces stress and prevents warpage.
- Draft Angles: 1° - 2° for easy part removal.
- Rounded Corners: Avoids stress concentrations.
- Hole Design: Depth-to-diameter ratio ≤ 2:1 to maintain strength.
- Corrosion-resistant materials (H13, S136 stainless steel).
- Cooling channels for uniform temperature control.
- Adequate ventilation prevents gas entrapment.
Adhering to industry best practices enhances process efficiency and product quality:
1. Material Handling and Preparation
- Store PVC resin properly to prevent contamination.
- Dry the resin at 60°C for 2-3 hours before molding.
2. Machine Selection and Maintenance
- Use an injection molding machine with corrosion-resistant screws, barrels, and nozzles.
- Ensure proper injection molding machine maintenance to extend machine lifespan.
Suggest product: PVC Injection Molding Machine – PVC Series
3. Optimize Processing Parameters
- Back Pressure: Maintain 3-10 bar to prevent degradation.
- Screw Rotation Speed: 20-60 RPM for consistent melting.
Defect | Cause | Solution |
---|---|---|
Burn Marks | Trapped air or excessive injection speed | Reduce speed, improve mold venting |
Warpage | Uneven cooling or inconsistent wall thickness | Optimize cooling channels, maintain uniform thickness |
Discoloration | Overheating or prolonged residence time | Lower barrel temperature, reduce residence time |
PVC injection molding enables the production of high-quality, durable plastic components across industries. Injection molding businesses can achieve optimal efficiency, quality, and cost-effectiveness in PVC operations by carefully managing material properties, mold design, and process parameters.
- Group Name: Huarong Group
- Brand: Huarong, Yuhdak, Nanrong
- Service Offerings: Injection Molding Machine, Vertical Injection Molding Machine, Injection Molding Automation
- Tel: +886-6-7956777
- Address: No.21-6, Zhongzhou, Chin An Vil., Xigang Dist., Tainan City 72351, Taiwan
Previous news : Beyond Injection Molding! Analyzing Successful Transformation Through Turn-Key Automation Solutions
Next news : Why Customized Injection Molding Machines Are Essential for Modern Manufacturing