Why Customized Injection Molding Machines Are Essential for Modern Manufacturing
2025-03-05 17:35:12
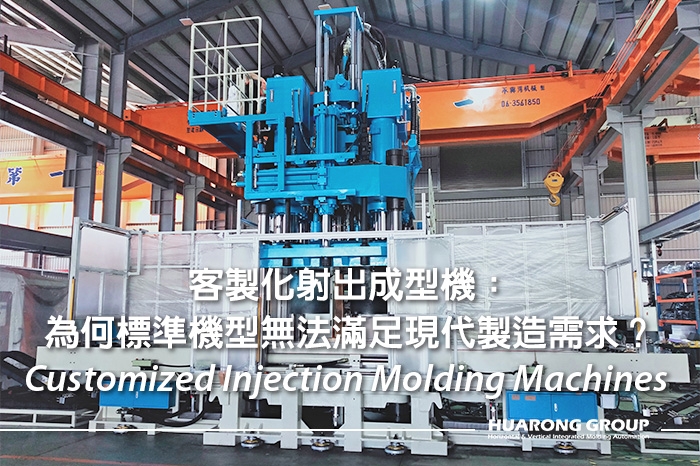
As market demands become increasingly diverse, traditional standard injection molding machines struggle to meet the manufacturing needs of specialized products. Whether it's multi-material integration, large structural components, or the application of emerging eco-friendly materials, companies require more flexible solutions to enhance production efficiency and ensure product quality. In this trend, customized injection molding machines have become the focus of the industry, helping businesses overcome the limitations of standard machines and achieve more efficient, stable, and sustainable production.
Modern industries no longer demand only "stable production" from injection molding machines. Instead, they require optimization for specific applications to improve efficiency, reduce costs, and enhance market competitiveness. While standard injection molding machines can meet mass-market demands, they often fall short in handling specialized processes, material applications, and automation integration.
Key Limiting Factors:
• Ever-changing market demands require greater production flexibility.
• Product designs are becoming increasingly complex, making it difficult for standard machines to accommodate multi-material integration and unique shapes.
• The green manufacturing trend makes it challenging for standard machines to adapt to emerging eco-friendly materials.
• Increasing demand for automated production, yet standard machines have limited integration capabilities.
Given these challenges, customized injection molding machines have become a crucial market trend, helping companies surpass the limitations of standard machines and create higher production value.
Further reading: Understanding Injection Molding Machine Types: Advantages and Disadvantages of 7 Popular Models
Advantage 1: Breaking Product Limitations and Enhancing Production Flexibility
Many products require specialized molding techniques, such as multi-material integration, complex geometries, or large-sized parts, which standard injection machines struggle to handle. Through customized machine structure and injection unit design, companies can enhance manufacturing flexibility and quickly adapt to market changes.
Key Features:
• Supports multi-material molding with precise control of flow channels and temperature.
• Customized injection units and mechanical structures to accommodate complex geometries and structural components.
Case Study: Automotive Glass Edge Molding Technology
Automotive glass edge molding demands high precision and stability, as glass inherently has certain tolerances that, if not properly managed, can lead to breakage or product defects. Huarong provides a customized solution with a precision compensation mechanism that absorbs ±0.2mm tolerances, ensuring that the glass remains stable throughout the injection and molding process while minimizing the risk of breakage. Additionally, injection weight deviations are controlled within ±1g to guarantee product consistency and quality. To meet various production needs, Huarong offers multiple machine configurations, including vertical clamping with horizontal injection, vertical clamping with vertical injection, and dual clamping with single injection.
Further reading: Vertical Injection Molding vs Horizontal Injection Molding for Plastic Components
Advantage 2: Meeting Special Size and Process Needs to Improve Production Efficiency
Many industries require the production of products with specific sizes, such as large structural components or elongated products. Standard injection machines may not have the necessary mold opening stroke or clamping force, affecting production efficiency and product integrity. Thus, machine designs tailored to product characteristics are crucial.
Key Features:
• Customized machines support large, long, or deep-cavity products, addressing mold stroke and clamping force limitations.
• Enhanced clamping structures ensure stable injection of large products, reducing deformation risks.
Case Study: Two-Platen Injection Machine for Long Product Manufacturing
Huarong's NRH series two-platen injection machines feature an extended mold opening stroke, making them ideal for long or deep-cavity products such as automotive interiors and household appliance casings. Their reinforced clamping structure and high-precision control system ensure stable injection molding of large-sized products while reducing deformation risks.
Related product: Two platen injection molding machine – NRH series
Advantage 3: Supporting New Material Technologies for Sustainable Manufacturing
As global demand for eco-friendly materials rises, companies must consider both production efficiency and material feasibility. However, many emerging materials, such as biodegradable plastics and dry-molded fiber, require specialized injection molding technology that standard machines cannot accommodate.
Key Features:
• Supports biodegradable plastics, bio-based materials, and dry-molded fiber molding.
• Specialized mold configurations enhance molding precision for new materials.
• Reduces material waste and carbon emissions, aligning with ESG goals.
Case Study: Breakthrough in Dry-Molded Fiber Injection Technology
Huarong collaborated with Swedish company PulPac to develop the world's first Scala dry-molded fiber forming machine, integrating patented fine-neck large-column design and clamping technology. This technology is successfully applied to 100% plastic-free, recyclable food packaging, such as paper cup lids. Not only does this innovation reduce carbon emissions, but it also offers enterprises a sustainable development solution.
Selecting the right customized injection molding machine requires evaluating a company's product characteristics, production needs, and future development direction. Here are three key factors to help you assess whether a customized solution is necessary:
Does the Product Have Special Structures or Multi-Material Requirements?
If a product design includes multi-material integration (such as dual-shot molding, soft-hard material combinations), complex geometries, or precision structures, standard machines may not provide the best molding results. Customized machines can adjust injection units, mold designs, and flow channels according to product characteristics, ensuring high-quality molding.
Are the Mold Opening Stroke and Clamping Force of Standard Machines Sufficient?
For large or long products, such as automotive interiors, large household appliance casings, or industrial components, standard injection machines may lack the necessary mold opening stroke, leading to incomplete molding or increased deformation risks. Customized machines can be designed with longer mold opening strokes and higher clamping forces to ensure stable production.
Are New Eco-Friendly Materials Being Used, Requiring Specialized Molding Technology?
With the rise of ESG and green manufacturing, many companies are adopting biodegradable plastics, bio-based materials, and dry-molded fiber. However, these materials differ in rheological properties from traditional plastics, requiring specific injection pressure, temperature control, and mold configurations. Customized machines can adjust molding parameters based on material characteristics, ensuring smooth production while minimizing material waste.
Further reading: Custom Injection Molding Machine Services | Precision Manufacturing Solutions
With increasing market diversification, standard injection machines' fixed specifications can no longer meet businesses' needs for specialized products. Customized injection machines break the limitations of traditional models, optimizing specific processes to enhance product quality and production efficiency. By adopting flexible machine designs, companies can maintain adaptability in competitive markets and improve their competitive edge.
Moreover, as environmental awareness grows, businesses are seeking sustainable manufacturing solutions. Customized machines support biodegradable plastics, new green materials, and advanced molding technologies, helping companies achieve environmental goals while reducing their ecological footprint.
With extensive industry experience and technical expertise, Huarong provides tailored machine solutions to ensure optimal production performance and long-term investment returns. If your production process faces challenges, customized injection machines are the key solution to unlocking new possibilities.
Contact Huarong now and let customized injection machines open new opportunities for your production line!
- Group Name: Huarong Group
- Brand: Huarong, Yuhdak, Nanrong
- Service Offerings: Injection Molding Machine, Vertical Injection Molding Machine, Injection Molding Automation
- Tel: +886-6-7956777
- Address: No.21-6, Zhongzhou, Chin An Vil., Xigang Dist., Tainan City 72351, Taiwan
Previous news : PVC Injection Molding: Process, Challenges & Best Practices (2025 Guide)