Energy Saving Injection Molding: The Key to Lower Costs, Higher Productivity, and ESG Readiness
2025-04-11 10:22:37
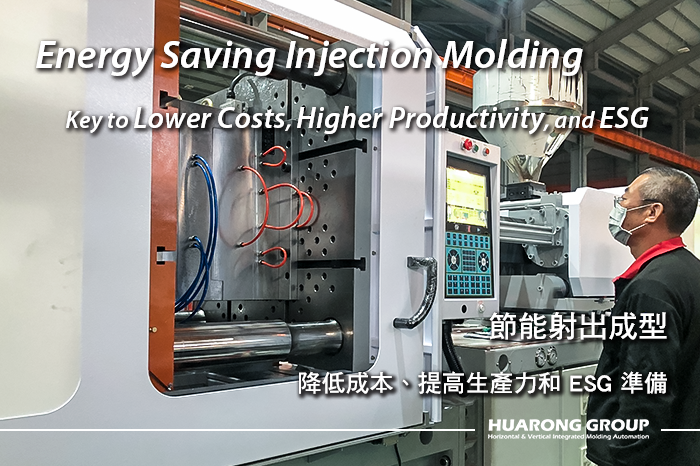
Energy Saving Injection Molding is not just a buzzword—it’s a crucial pivot that forward-thinking manufacturers across the world are embracing. With rising energy costs, stringent environmental norms, and increasing global competition, injection molding businesses must evolve to survive and thrive.
The injection molding business has traditionally been energy-intensive. From heating the barrel to generation of clamping force, significant energy is consumed at every stage. Improving energy efficiency is a direct path to cost reduction for factories that run dozens of machines 24/7, where electricity costs can heavily impact profitability.
Moreover, with growing awareness of sustainability, manufacturers must reduce emissions due to client and regulatory pressure. Energy-efficient injection molding machines lower costs and support your company’s ESG goals. Opting for energy-efficient solutions is beneficial for the planet and a smart business move.
Delve into the transformative technologies that make injection molding more energy-efficient than ever before.
Servo Motor Systems: Power When You Need It
Traditional hydraulic systems run continuously, wasting power even when not molding. In contrast, servo motor systems operate only when required, reducing idle energy consumption.
Customer Benefits:
- Lower Cost per Part: Save up to 70% in electricity costs
- High Precision: Enhanced injection speed and pressure control for superior part quality.
- Faster Cycle Times: Quicker response increases productivity and reduces manufacturing time.
- Lower Oil Temperatures: Minimizes heat generation, extending hydraulic oil and component lifespan.
- Less Frequent Maintenance: Reduced wear-and-tear ensures longer machine uptime and fewer service interruptions.
"After switching to servo, the machine only moves when it should. You can literally hear the savings." – Senior Technician
Energy-Efficient Direct Drive Material Storage Motor (Patent No: M654645)
One of the hidden energy hogs in injection molding is the material storage (plasticizing) process. Using an Energy-Efficient Direct Drive Material Storage Motor specifically designed for this stage eliminates energy loss through gear and belt transmissions.
Customer Benefits:
- Up to 26% Energy Savings: Efficient power transmission significantly reduces energy consumption during material storage and plasticizing.
- Concurrent Operation: Allows material storage to coincide with cooling and mold opening, reducing total cycle time.
- Enhanced Productivity: Shorter cycles directly boost production efficiency.
- Lower Mechanical Loss: Direct drive eliminates belts and gears, reducing maintenance needs and increasing overall system lifespan.
- Stable Processing: More consistent screw speed and torque improve melt quality and reduce scrap rate.
"This one upgrade can cut a huge chunk off your energy bill—especially for machines with long screw retraction times."
Microcellular Foaming Injection Molding Device (Patent M659181)
A breakthrough in energy saving and material efficiency, a microcellular foam injection molding technology reduces melt density by injecting supercritical fluids—such as nitrogen or carbon dioxide—into the molten plastic to create uniformly distributed micro-bubble structures (pores), leading to lighter parts with equal strength.
Further reading: Microcellular Foam Injection Molding: Achieving Maximum Weight Reduction and Dimensional Stability
Customer Benefits:
- Product Weight Reduction of 15–20%: Nitrogen gas creates a foamed structure, significantly reducing weight while maintaining structural integrity and lowering material costs.
- No Holding Pressure Required: The foaming process replaces the holding pressure stage, shortening cycle times, minimizing internal stress, and ensuring consistent dimensional accuracy with reduced warpage.
- Reduced Clamping Force by 30–50%: The internal bubble structure reduces cavity pressure during injection and decreases clamping force, lowering stress on molds and machines to prolong their operational life.
- Lower Injection Pressure: Microcellular molding lowers mold filling pressure, reducing machine load and maintenance costs, leading to a longer lifespan and less operating stress.
- Directly Recyclable and Eco-Friendly: Unlike chemical methods, this physical foaming process uses no harmful additives. Products are recyclable, reducing waste, lowering emissions, and improving environmental compliance—ideal for manufacturers aiming for sustainability.
"This tech doesn't just save resin—it saves warehouse space and delivery cost too."
Item | Traditional Motor System | Servo System | All-Electric System |
---|---|---|---|
Precision | ★ | ★★★★ | ★★★★★ |
Energy Saving Performance | ★ | ★★★★ | ★★★★★ |
Versatility (Mold Adaptability) | ★★★★ | ★★★★★ | ★★ ~ ★★★ |
Finished Product Stability | ★★ | ★★★★ | ★★★★★ |
System Cost (Initial Investment) | ★ (Low) | ★★★ (Medium) | ★★★★★ (High) |
Maintenance Difficulty | ★ (Easy) | ★★★ | ★★★★ (Requires Electrical Control Expertise) |
Implementation Recommendation | Limited to basic applications | Mainstream choice with a balance of performance and versatility | Ideal for ultra-high precision and maximum energy-saving needs |
Many factory owners hesitate to replace their older injection molding machines. The machines run smoothly, and no major issues are apparent. Your equipment has served you well for over 15 years and still produces acceptable parts.
But here’s the real question:
What’s the hidden cost of doing nothing?
Older machines, even if they appear to be operating “just fine,” often consume significantly more energy, require more frequent maintenance, and deliver lower precision. These small inefficiencies—slightly higher power bills, slightly longer cycle times, and slightly more rejected parts—add to major losses over time.
You may not see the cost daily, but it’s there—eating into your profit margins, reducing competitiveness, and holding you back from achieving ESG goals or automation readiness.
Item | Old Machine (15+ years) | New HRFC Servo Machine |
---|---|---|
Energy Consumption | High hourly power usage Annual electricity costs continue rising | Saves over 10 kWh per hour. Could decrease annual electricity expenses by USD 10,000 to 16,000. |
Maintenance Costs | Frequent breakdowns and aging components Maintenance can easily cost USD 600 to 2,800 annually | More stable and reliable Lower repair frequency and cost |
Precision & Yield | Slow response, low repeatability More defects and scrap | Precision improved by 10–15 times Better yield, consistent quality |
Smart Connectivity | Outdated control system No support for automation or networking | Fully compatible with smart factory systems Supports automation and remote monitoring |
Estimated Payback | - | ROI achievable in about 4–5 years with energy and maintenance savings combined |
" Upgrading isn’t just about fixing what’s broken—it’s about preventing waste, unlocking efficiency, and preparing your factory for the next decade."
Replace the Old with the New: A Real-World Upgrade Path
If you're running machines over 10 or 15 years old, chances are they are energy guzzlers. But don’t worry—you don’t need to overhaul everything overnight. There’s a structured path to modernization that many Indian manufacturers are already following.
Many SMEs think ESG is a corporate buzzword—but ESG compliance is quickly becoming a business reality.
- Exports to EU and ASEAN? Carbon footprint reporting is coming. Energy-efficient machines help you comply.
- Supplying to global OEMs? They’ll soon require ISO 50001 or green certifications. Using servo systems helps check that box.
- Looking for loans? Some banks now offer better terms to ESG-compliant manufacturers.
Switching to energy-saving machines reduces Scope 1 emissions, enhances your factory’s energy efficiency, and makes you a more appealing partner for international buyers. Government incentives for energy-efficient equipment are also expected to increase, benefiting early adopters.
Energy efficiency isn’t only about lower bills. It’s about smarter, faster, more stable production.
True Energy Saving's Meaning
- 1 second less per cycle
- 1 fewer defect per shift
- 1 fewer emergency repair
- 1 less technician on standby
These “lesses” add up to a lot more for your bottom line.
Energy Saving Injection Molding is a necessity for manufacturers to remain relevant, profitable, and sustainable. The tools, like servo-driven machines and direct drive motors, are available. A willingness to act and a strategic plan for implementation is needed. Whether you're unsure about the ROI, or simply need help auditing your current machine performance, we're here to help.
Book your free one-on-one energy-saving consultation today.
Let us map out a plan that fits your production goals, ESG needs, and investment budget.
- Group Name: Huarong Group
- Brand: Huarong, Yuhdak, Nanrong
- Service Offerings: Injection Molding Machine, Vertical Injection Molding Machine, Injection Molding Automation
- Tel: +886-6-7956777
- Address: No.21-6, Zhongzhou, Chin An Vil., Xigang Dist., Tainan City 72351, Taiwan
Previous news: 15 Years Strong: Two Platen Machine Powered by Huarong