Maximizing Injection Molding Machine Efficiency Through Preventive Maintenance
2022-07-15 15:46:07
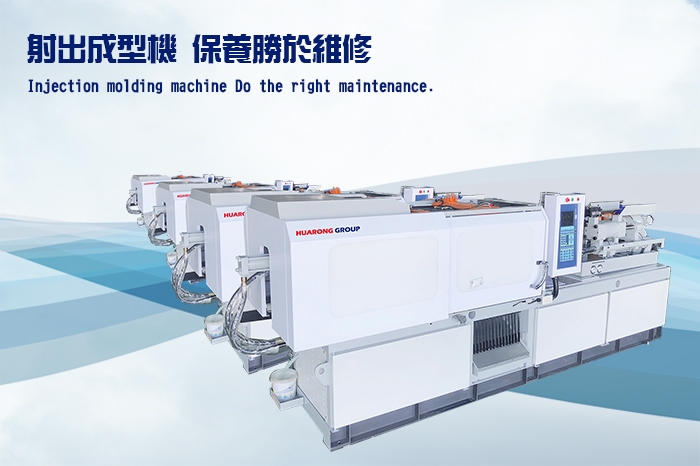
The injection molding machine is the cornerstone of plastic product manufacturing. Its stability is critical for timely order delivery; any malfunction can cause significant disruptions and losses for injection molding plants. Treating your injection molding machine like a long-term partner—one that tirelessly works to create value—is essential. But how well do you know how to maintain and cherish this partner?
Here are three key points to guide you in preventive maintenance. For more comprehensive machine maintenance, we recommend reading the article "Injection Molding Machine Maintenance PDF and Checklist"
Regular preventive maintenance is fundamental for all components of an injection molding machine, ranging from simple weekly tasks to in-depth annual check-ups. Alongside scheduled maintenance, keen observation is crucial. A thorough, diligent inspection during maintenance can prevent many potential problems.
Areas to Observe:
- Injection Unit: Comprising a hydraulic motor, injection double cylinder, screw barrel set, and electric heating components, the injection unit is the machine's core. The hydraulic motor powers the screw, plasticizing the material, which is then injected into the mold. Regular observation and maintenance of this unit are crucial for optimal operation.
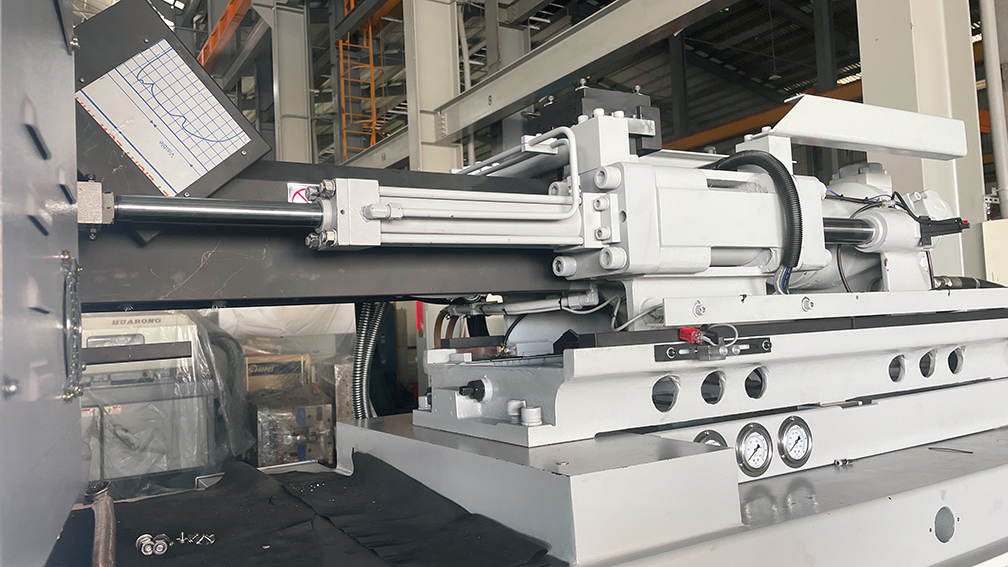
- Clamping Unit: The parallelism of the movable and fixed platens affects the machine's accuracy. Under constant high pressure and rotational force, the toggle rod shaft and bushing are prone to frictional heat and wear. Using high-quality lubricants to prevent these issues is essential.
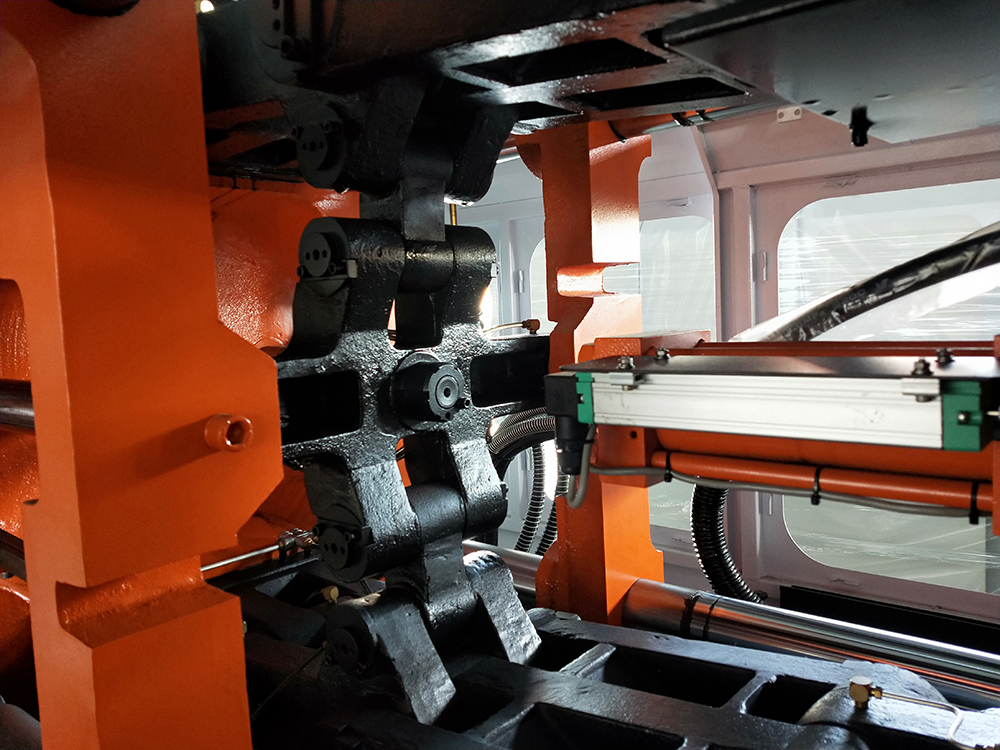
- Hydraulic System: This system includes the pump, motor, brake cylinder, directional valve, flow valve, pressure valve, safety valve, cooler, and hydraulic motor. Maintaining oil temperature between 40°C and 50°C and ensuring good oil quality is critical for stable pressure and performance.
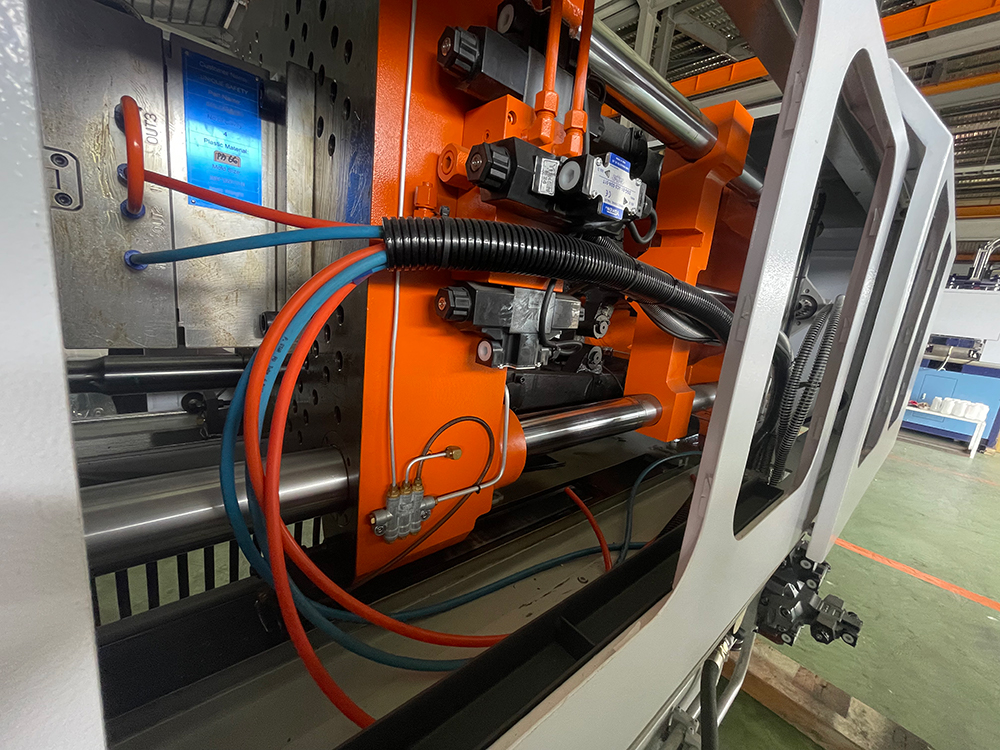
- Electrical System: Vibration can cause electrical components to loosen, leading to excessive current and potential part failure. Regular checks and maintenance can prevent these issues.
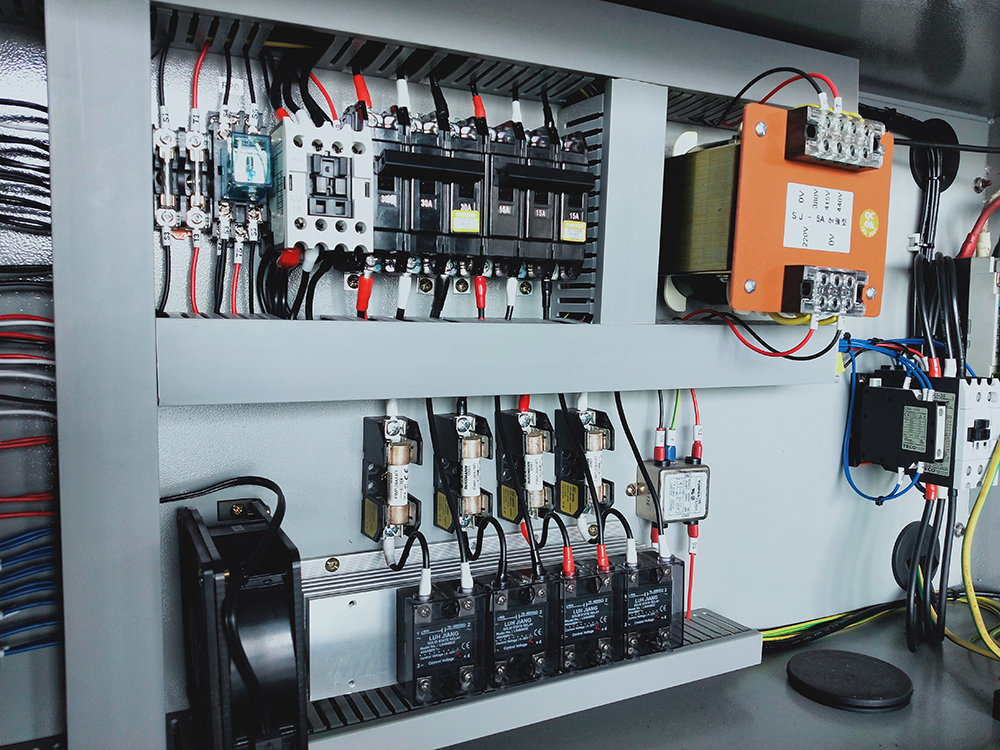
Preventive Maintenance Schedule:
- Weekly: Inspect the electric heater, high-pressure hoses, and joints for oil leaks. Check the screw parts and the nozzle's electric heating. Clean any residual pigments and additives from the machine, remove waste oil, and clean the oil circuit board and hydraulic components.
- Monthly: Inspect the ground wire, electrical circuit, movable platen, and injection double cylinder sliding feet. Perform machine grease maintenance and clean the oil filter.
- Quarterly: Check the hydraulic oil and inspect the machine’s movable points for abnormal wear. If necessary, replace the oil filter.
- Yearly: Inspect the motor and ventilation system, measure insulation resistance, and test the oil seal and cylinder functions. Clean and organize the cooling water system, replacing it if damaged.
Proper lubrication prevents wear, ensures smooth movement, and reduces noise.
Hydraulic Oil:
Hydraulic oil must effectively transmit power and provide mechanical lubrication. Improper hydraulic oil use can lead to rapid wear of hydraulic parts and unstable pressure. The ideal hydraulic oil should be:
- Resistant to compression
- Of appropriate viscosity
- Chemically stable over long-term use
- Lubricative
- Compatible with various oil seal materials
- Fire-resistant
- Non-toxic
- Oxidation-stable
- High-temperature stable
Lubricating Oil:
Lubricating oil must be clean and free of recycled oil, and its filter should be cleaned regularly. Daily checks ensure the lubrication system's normal operation. Remember to use a manual grease gun to apply grease into the grease holes for proper lubrication.
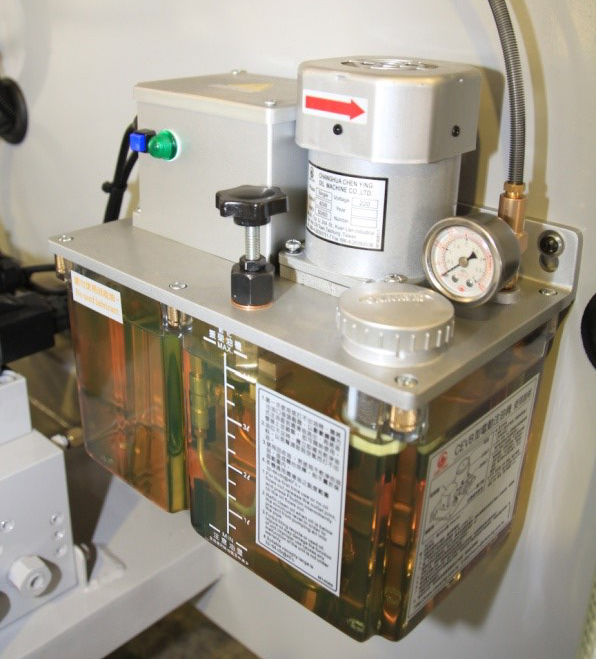
Neglecting the cooler can reduce cooling efficiency due to scale buildup, increasing the machine’s power consumption.
Cooler Tube Cleaning:
- Remove the cover and use a nylon or cleaning preparation to clean inside the cooler.
- Alternatively, circulate 0.6-0.8% hydrochloric acid through the cooler.
- Clean the copper pipes with an air gun.
- Reassemble and connect the cooling water.
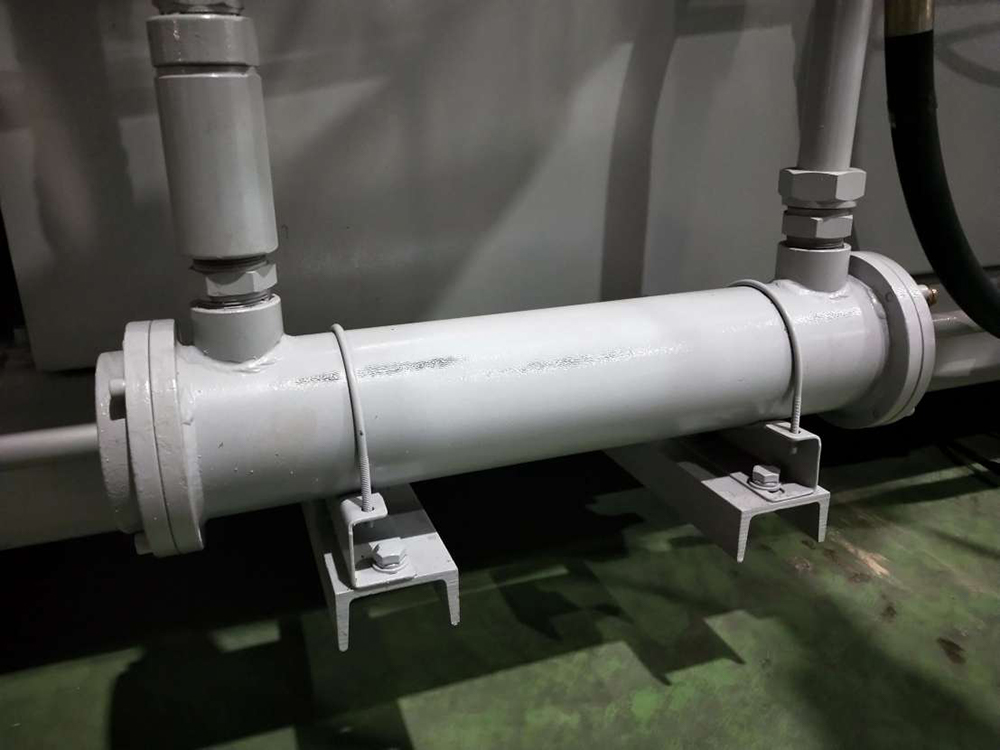
Attention:
- Use only fresh water.
- Maximum operating pressure: oil side 1.0Mpa, waterside 0.5Mpa.
- Drain water from the heat exchanger when not in use during freezing seasons.
- Clean the heat exchange tubes every six months.
- Use soft water to avoid mineral buildup.
Implementing a preventive maintenance strategy and developing good habits can extend the life of your injection molding machine, minimize downtime, and reduce maintenance costs. As an experienced injection molding machine manufacturer, HUARONG emphasizes the importance of durability, reliability, and routine maintenance to ensure your machine operates at full capacity and delivers value beyond expectations.
Contact Details:
- Tel: +886 6 7956777
- Fax: +886 6 7951666
- Email: [email protected]
- Hours: 08:30 AM - 17:30 PM (GMT+8) from Monday to Friday
Further reading: Injection Molding Machine Maintenance PDF and Checklist
Previous news : What's the reason for Indian auto parts manufacturer to choose Huarong's injection molding machines?
Next news : What are Fundamentals of Injection Molding? 3 Keys to Plastic Injection Plant