What are Fundamentals of Injection Molding? 3 Keys to Plastic Injection Plant
2022-07-21 09:54:27
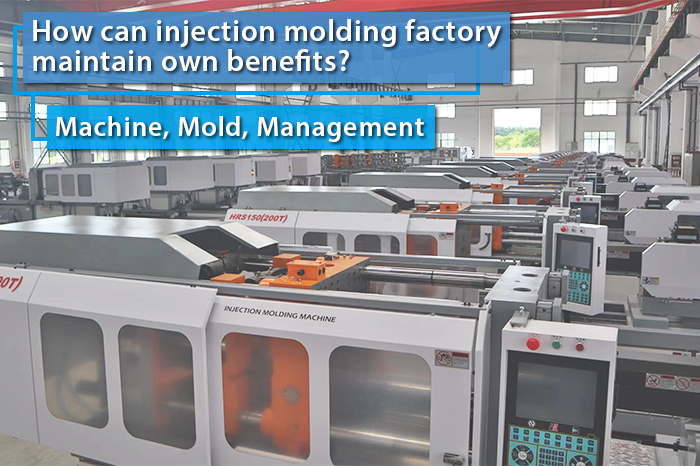
In the bustling world of manufacturing, few processes are as crucial and fascinating as plastic injection molding. At the heart of this industry lie the plastic injection plants, where raw materials are transformed into a vast array of products that shape our daily lives. Join us on a journey deep into the heart of plastic injection molding moldingplants as we explore the fundamentals of injection molding.
Injection molding is a pivotal production process that yields a myriad of fixed-shaped items by injecting molten material into a mold. This process, critical to various industries, encompasses metal, glass, and common thermoplastic and thermosetting plastic products. The heart of this manufacturing marvel lies in the injection molding machine, also known as a plastic injection machine, which orchestrates the intricate dance of plastic transformation through two key stages: injection and molding.
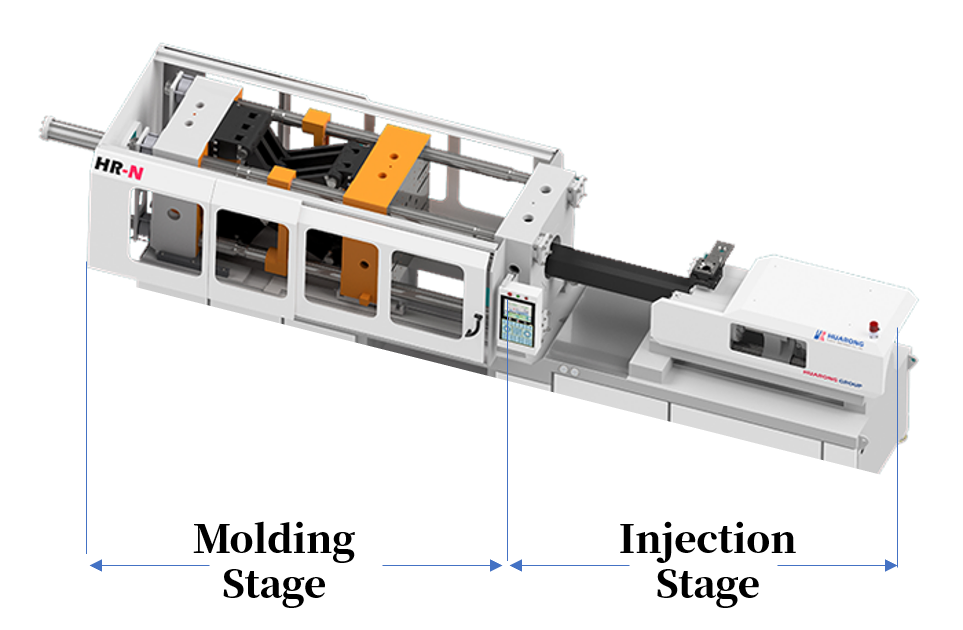
Related article: What is Injection Molding Process? Definition, Step and Product
Injection Stage
In the initial "injection" stage, plastics, typically in granular form, are introduced into the barrel of the injection machine via a hopper dryer or autoloader. Here, the plastics undergo a metamorphosis, transitioning from solid to fluid under the barrel's intense heat. This molten state is crucial as the plastics are then compressed and propelled forward by a screw within the barrel. With precision and speed, the molten plastics are injected into a closed mold, setting the stage for the next act.
Molding Stage
The subsequent "molding" stage unfolds as the molten plastics, now within the confines of the mold, undergo a cooling process. This cooling period is essential, as it solidifies the plastics, ensuring they conform to the mold's shape. Once cooled and solidified, the mold is opened, and the product is ready for extraction, marking the completion of the injection molding cycle.
Applications and Market Dynamics
Injection molding's versatility shines through its ability to produce a vast array of plastic products, ranging from everyday essentials to intricate automotive components, medical devices, and cutting-edge 3C electronics. Its widespread use underscores its importance in modern manufacturing, driving innovation and shaping the products we rely on daily.
As the world's demand for plastic products continues to grow, how to stand out and maintain a competitive advantage for plastic injection plants has become an important issue. Having good injection molding technology can not only improve production efficiency but also effectively improve the quality of finished products and reduce unnecessary production waste. Huarong group combines more than 40 years of the manufacturting and assisting customers experience in injection molding, for injection molding technology, it is divided into 3 major keys: “Machine”, “Mold”, and “Management”.
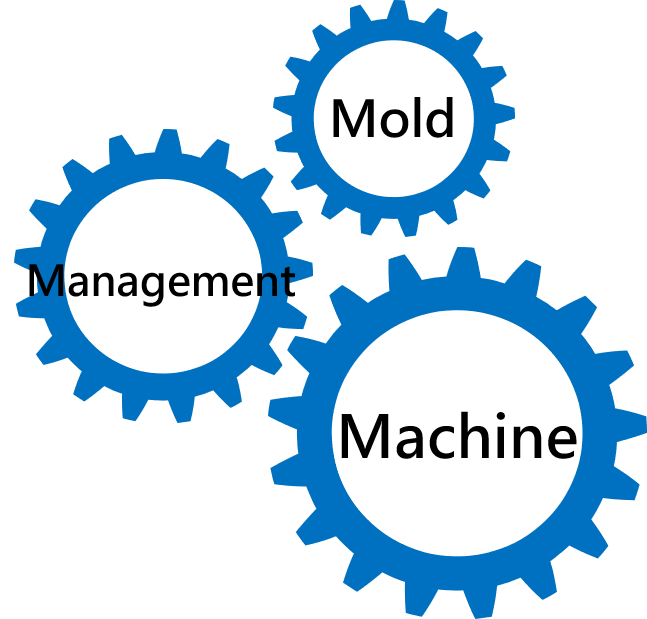
The Injection Molding Machine: Where Magic Happens
The cornerstone of any plastic injection plant is the injection molding machine. These marvels of engineering come in various sizes and configurations, but they all work on the same basic principle. Here's a simplified overview of the process:
- Clamping: The two halves of the mold are securely clamped together.
- Injection: Molten plastic is injected into the mold cavity under high pressure.
- Cooling: The plastic cools and solidifies inside the mold.
- Ejection: The mold opens, and the newly formed plastic part is ejected.
Huarong's Machine Features
- Sturdy
- Stable
- Versatile
- Simple in Operation
- Simple in Maintenance

Related product: Horizontal Injection Machine
Related product: Vertical Injection Machine
The Mold: A Work of Art
The mold is where the magic happens. Crafted with precision and care, the mold determines the shape and features of the final plastic part. Molds can be simple or complex, depending on the intricacy of the part being produced. They are typically made from hardened steel and can last for thousands or even millions of cycles.
The Raw Materials: From Pellets to Products
Plastic injection plants use a variety of raw materials, known as resin or pellets, to create their products. These pellets are melted down and injected into the mold, where they cool and solidify to form the final part. Different types of plastics have different properties, such as strength, flexibility, and heat resistance, making them suitable for a wide range of applications.
Further reading: Understanding the 10 Most Common Injection Molding Materials
Innovation is the lifeblood of the plastic injection plant industry, driving it forward into new realms of efficiency and productivity. From cutting-edge technologies to sustainable practices, here are some of the key innovations shaping the future of plastic injection molding:
Industry 4.0: The Age of Smart Manufacturing
One of the most significant trends shaping the plastic injection plant industry is Industry 4.0, also known as the Fourth Industrial Revolution. This paradigm shift is driven by the integration of digital technologies into the manufacturing process, leading to increased automation, efficiency, and productivity.
Smart Factory: The Future of Manufacturing
Our company invested in a system for plastic injection plants called the HFM system. This effective management is the cornerstone of successful injection molding operations. Smart factory management encompasses planning, organization, leadership, and control of resources to achieve set goals. Huarong Group's intelligent platform enables real-time monitoring of production progress, empowering managers of plastic injection molding plants to make informed decisions swiftly. From grassroots operators to top managers, this platform enhances efficiency and streamlines operations, ensuring optimal performance across all levels of the organization.
Huarong's Management Features
- Enhance Efficiency from Grassroots Operators to Top Managers: The HFM system facilitates seamless communication and collaboration among all levels of the organization, enhancing overall efficiency.
- Information Transmission: The platform ensures smooth and timely transmission of critical information, reducing delays and improving decision-making.
- Information Collection: HFM collects and analyzes data from various sources, providing valuable insights for process optimization and resource allocation.
- Machine Intelligent Self-Inspection: The system enables machines to perform self-inspections, identifying potential issues before they escalate, and reducing downtime.
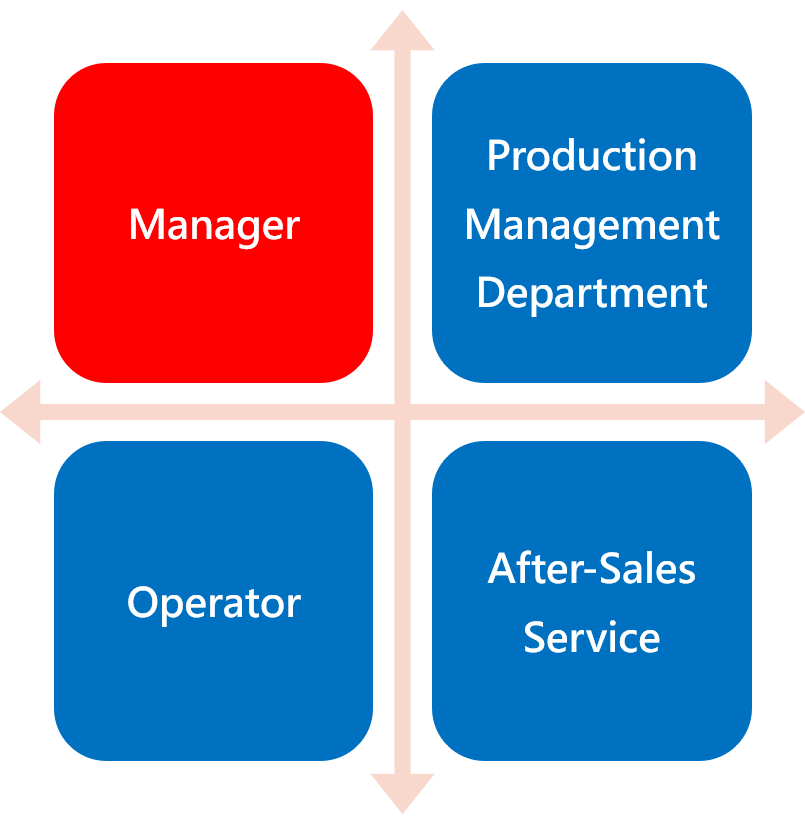
Related product: Smart Factory Management - HFM
Injection molding is a testament to human ingenuity. It revolutionized the manufacturing landscape with its precision, efficiency, and versatility. As the plastic industry continues to evolve, embracing technological advancements and innovative practices will be key to sustaining growth and meeting the demands of an ever-changing world. Huarong Group is an experienced injection molding machine manufacturer and insists on meeting plastic injection molding plants' production needs. If you have any inquiries, please feel free to contact Huarong.
- Group Name: Huarong Group
- Brand: Huarong, Yuhdamolk, Nanrong
- Service Offerings: Injection Molding Machine, Vertical Injection Molding Machine, Injection Molding Automation
- Tel: +886-6-7956777 #521
- Address: No.21-6, Zhongzhou,Chin An Vil., Xigang Dist., Tainan City 72351, Taiwan
- Official Website: https://www.huarong.com.tw/
Previous news : 3 main points teach you Injection molding machine preventive maintenance
Next news : Machinery Installation in Injection Molding: Essential Procedures and Precautions