What is injection molding machine? By clamping mechanism to choose injection molding machine model
2022-08-26 15:54:55
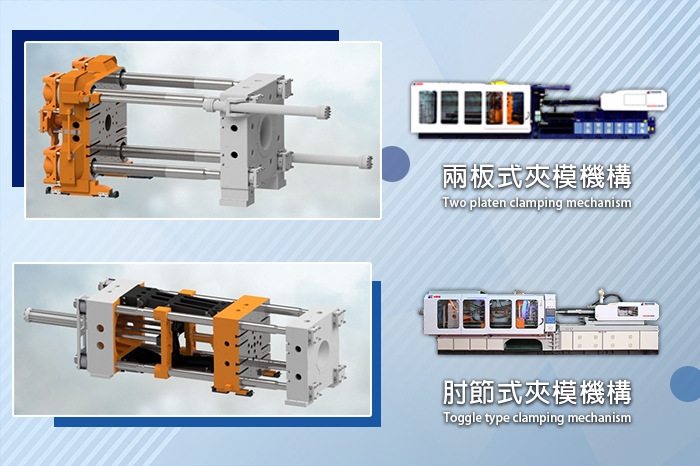
What is an injection molding machine? What can be called a reasonable injection molding machine?
In the article "How to choose a suitable injection molding machine? From the machine itself and plastic product!” mentioned that when deciding on an injection molding machine, you can consider from three directions:
1. Clamping unit : the size of the mechanism :
Determines whether the mold can be put into the injection molding machine, and when the plastic product is completed, whether it can be ejected and automatically dropped.
2. Injection unit : plasticizing ability :
Determines whether the injection volume is sufficient and the ability to plasticize plastic is sufficient.
3. Power system :
Determines whether the injection molding machine's power is sufficient or not.
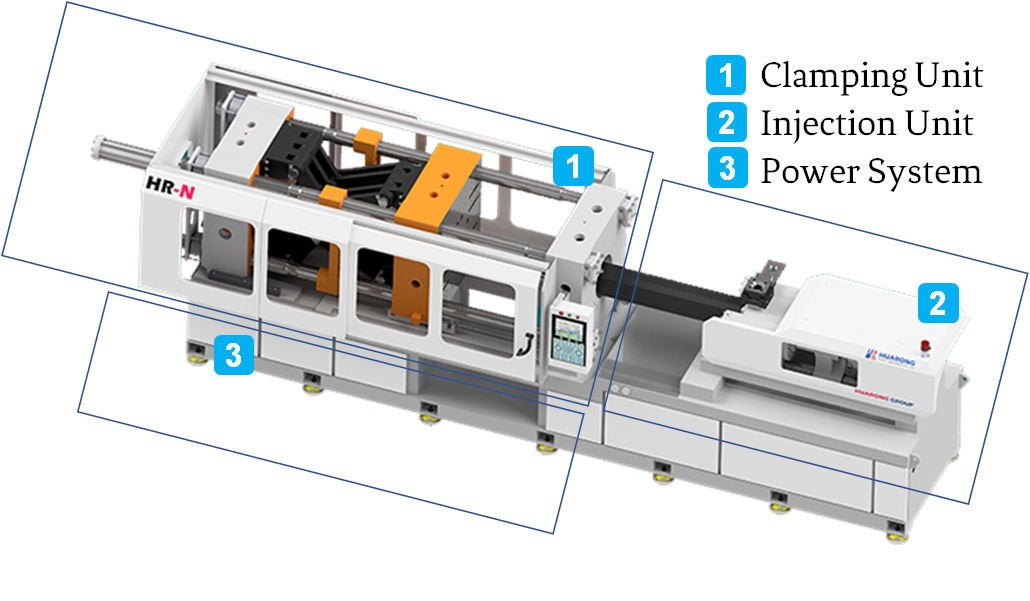
Now let's have a deeper understanding of what an injection molding machine is. First, let's talk about the clamping unit of the injection molding machine.
About the clamping unit of the injection molding machine, its clamping mechanism can be divided into 2 types – Toggle type, Direct pressure type
The clamping mechanism of the injection molding machine can be divided into 2 types – toggle type and direct pressure type. Toggle type injection molding machine can be further divided into 2 types – inward toggle injection molding machine and outward toggle Injection molding machine. Direct pressure injection molding machine can be divided into 3 types – single-cylinder direct pressure injection molding machine, compound direct pressure injection molding machine and the current mainstream two platen injection molding machine (as shown in Figure 1 to Figure 6) .
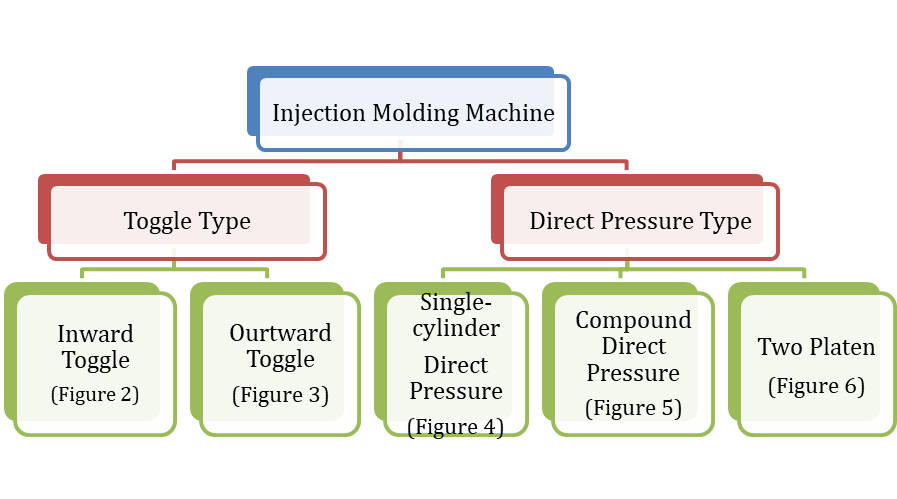
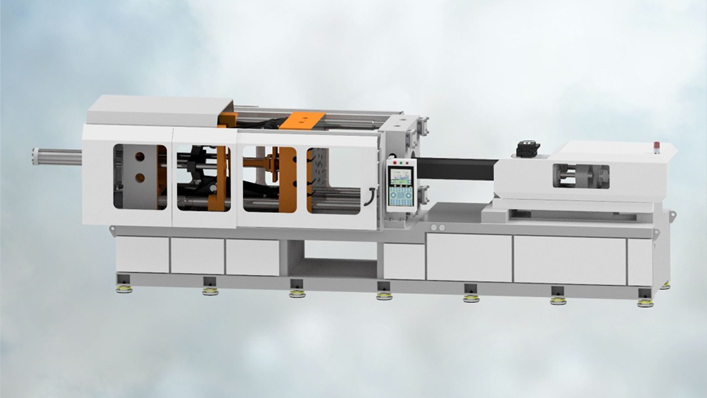
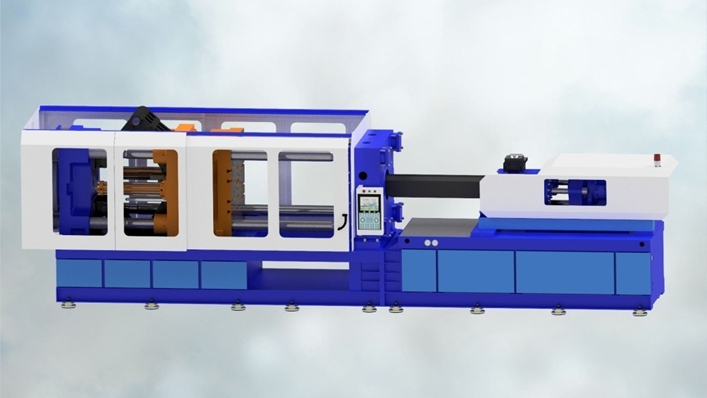
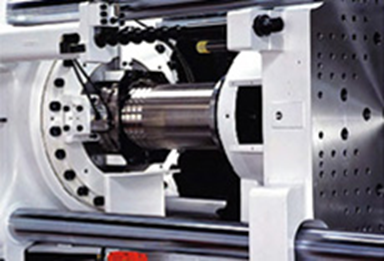
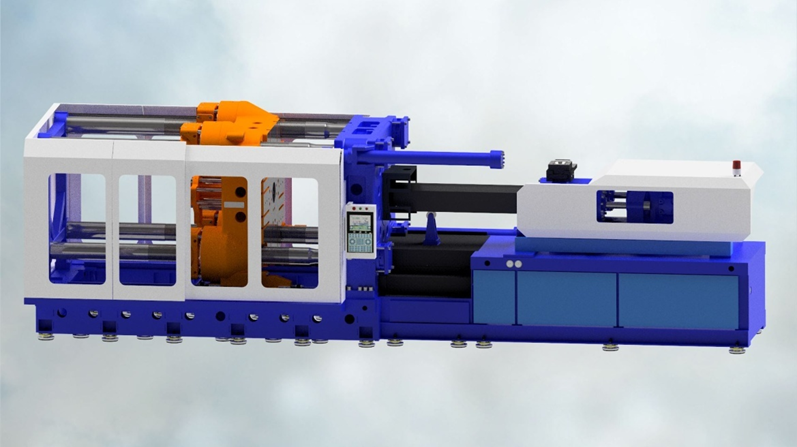
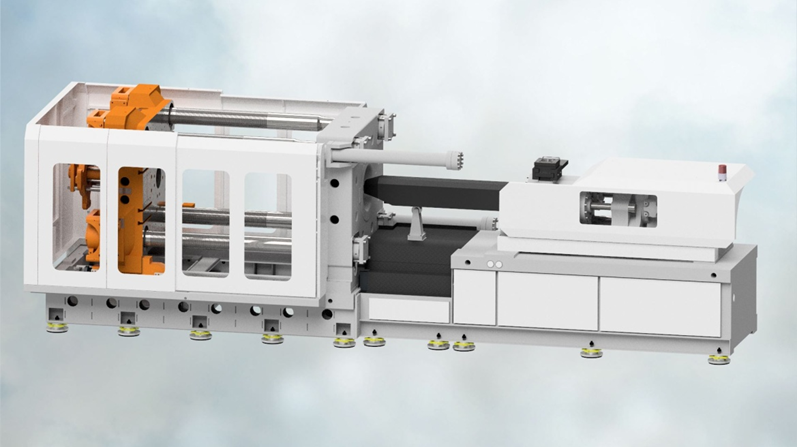
Each clamping mechanism has its own mechanical structure design. Among them, the inward toggle injection molding machine and the outward toggle injection molding machine are both toggle linkage mechanism. The inward toggle injection molding machine currently has the highest market share in the injection molding industry. Although the outward injection molding machine is less, it has its special characteristics that the machine length is shorter and the mold opening stroke is longer, so the outward injection molding machine is very suitable for the production of deeper barrel plastic products.
About the direct pressure injection molding machine, the single-cylinder direct pressure injection molding machine has a large size of the clamping cylinder. In a large size of injection molding machine, single-cylinder direct pressure injection molding machine has difficulties making components and doing the machine maintainence. Therefore, it’s gradually replaced with two platen injection molding machine.
Next, we will use the two types of injection molding machines that have a high market share – the inward toggle injection molding machine and the two plate injection molding machine as models. Through 5 major parts – clamping mechanism components, clamping action, mold opening stroke, clamping force and machine size to have a deeper understanding of what is a reasonable clamping mechanism on a medium-to-large size injection molding machine.
5 major parts to understand a reasonable clamping mechanism of medium-to-large size injection molding machine
1. Clamping mechanism components
The toggle type clamping mechanism is composed of a fixed platen, a movable platen, a die height platen, an I-shaped plate, four sets of tie bars, a set of toggle linkage mechanism, a set of clamping cylinder and a set of mold-adjusting gear (as shown in the figure). 7).
Compared with the two plate clamping mechanism, the toggle clamping mechanism differs in that there are a die height platen, an I-shaped plate, a set of toggle linkage mechanism, a set of clamping cylinder and a set of mold-adjusting gear (as shown in Figure 8).
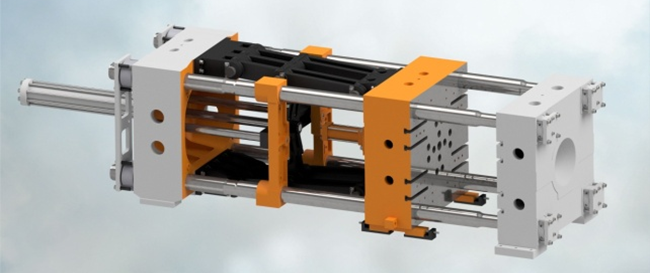
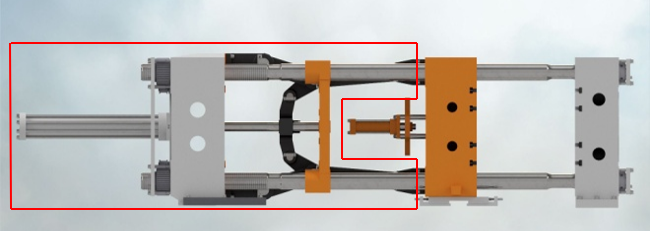
The two plate clamping mechanism is composed of a fixed platen, a movable platen, four sets of tie bars, two sets of mold opening and closing cylinders and four sets of direct pressure clamping cylinders (as shown in Figure 9).
Compared with toggle type clamping mechanism, the two plate clamping mechanism differs in that there is omitted a die height platen, an I-shaped plate, a set of toggle linkage mechanism, a set of clamping cylinder and a set of mold-adjusting gear, and only a set of mold opening and closing cylinder and four sets of direct pressure clamping cylinders are added (as shown in Figure 10).
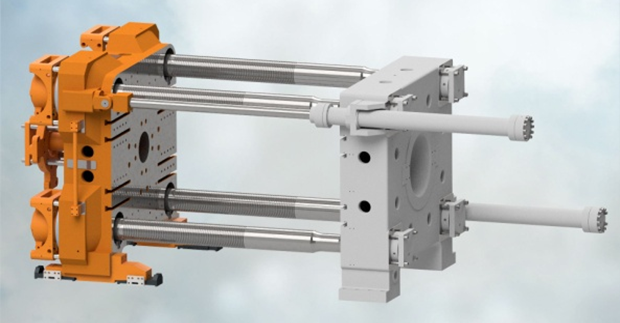
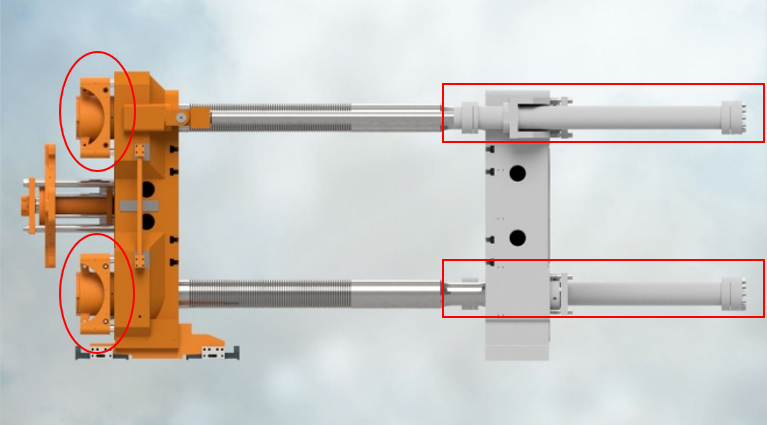
Based on the above comparison, the toggle type clamping mechanism and the two-platen clamping mechanism are significantly different. The toggle type clamping mechanism uses relatively more components. In terms of the injection molding machine weight, because of the difference in the overall mechanism, the two platen injection molding can be reduced by 35%, which is good for energy saving, carbon reduction and material saving.
2. Clamping action
In the process of clamping from the maximum opening distance to the fully extended toggle, the toggle movement ( mold opening and closing movement ) is an uninterrupted continuous action in the toggle clamping mechanism. If the same movable platen moving distance and power of the machine platen closed is used to simulate the movement situation of the toggle clamping mechanism and the two platen clamping mechanism. The toggle type clamping mechanism changes from speed amplification to pressure amplification in the clamping process, and the movable platen movement situation presents a curve (as shown in Figure 11). When the toggle type clamping mechanism is approaching 2 seconds, it enters the pressure amplification stage, the cylinder continues to push at the same speed, and the movable platen exhibits a slight displacement due to the toggle movement, and it takes 3.5 seconds to complete the entire clamping process.
The clamping process of the two platen clamping mechanism needs to go through the three-stage action of closing the mold > clamping action > clamping pressurization. The two platen clamping mechanism directly pushes the movable platen by mold opening and closing cylinders, and the movable platen movement situation presents a linear trend (as shown in Figure 11). When approaching 2.2 seconds, the mold surfaces are in contact. Since the clamping action must include the time of clamping action and clamping pressurization, the overall action time should last for 4.1 seconds to complete the clamping action. Compared with the toggle type clamping mechanism, it added 0.6 seconds.
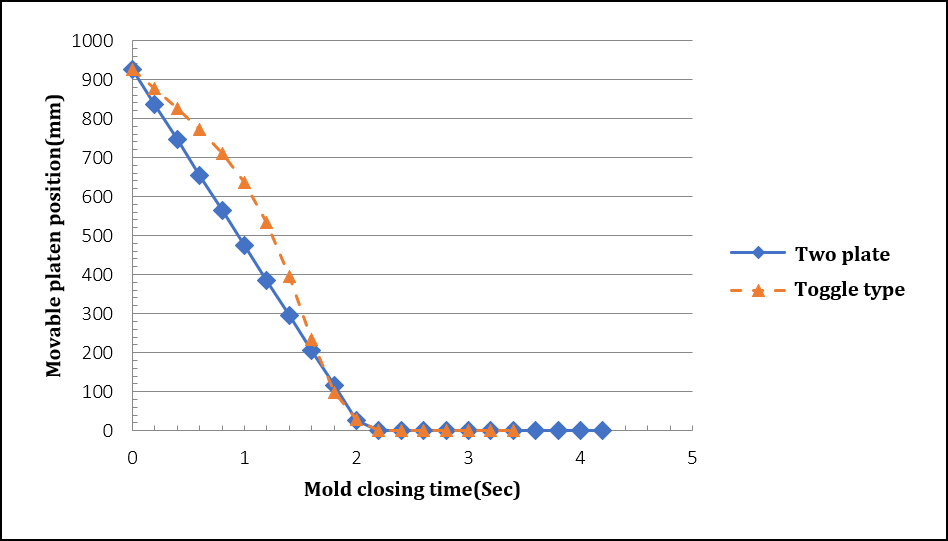
From the above comparison, it can be seen that in the comparison of mold closing time of the same specification, the two platen clamping mechanism takes 0.6 seconds longer than the toggle clamping mechanism, but for medium-to-large size of injection molding which has a longer production cycle for large products, this difference is little impact.
3. Mold opening stroke
The mold opening stroke of the toggle clamping mechanism is limited by the motion range of the toggle linkage mechanism (as shown in Figure 12). When the customer wants to increase the mold opening stroke due to product requirement, the mold opening stroke is not easy to increase.
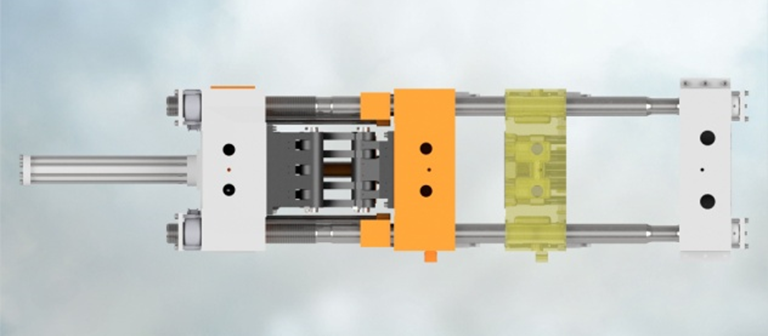
The mold opening stroke of the two platen clamping mechanism is driven by two sets of mold opening and closing cylinders (as shown in Figure 13). When customers want to increase the mold opening stroke due to product requirement, the mold opening stroke can be modified by the cylinder stroke, tie bar and machine frame length to meet product requirements.
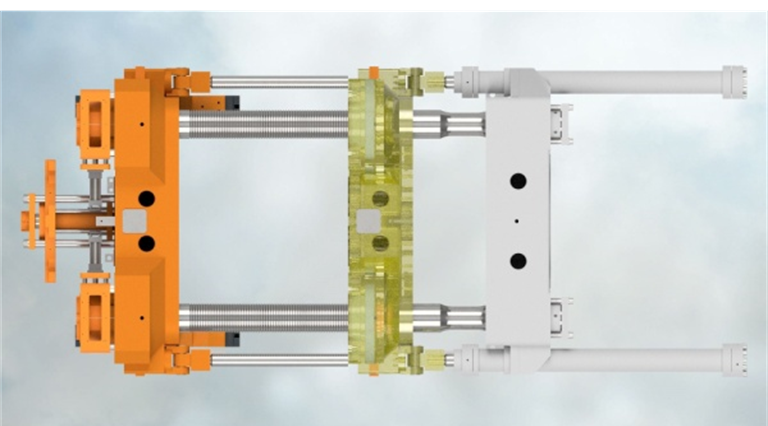
Therefore, the two platen injection molding machine has the advantage on the mold opening stroke. When the customer needs to increase the mold opening stroke due to the product requirement, it can be customized according to the product. There is no need to choose a larger size of the injection molding machine due to the mold opening stroke.
4. Clamping force
The clamping force is applied by the clamping cylinder, and the clamping force is obtained by stretching the tie bar through the magnification of the toggle linkage mechanism. Due to the influence of the four sets of tie bars (as shown in Figure 14), the thread clearance of the 8 nuts, the parallelism of the closing and the rotation angle, the clamping force of each set of tie bars may have a difference, which requires the engineer to match the strain gauge to adjust each nut to a reasonable position.
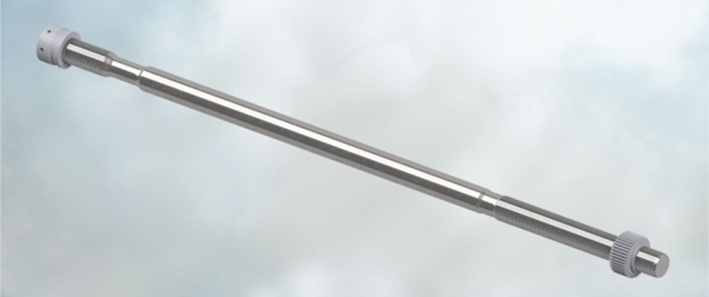
Taking the tie bars with a diameter of 180 and a load of 250 tons as an example, when the gear nut rotation difference is 10∘ (as shown in Figure 15), the nut position difference is 0.235 mm. This difference will affect the stretching amount of the tie bar. The difference is put into the equation (δ=PL/AE) to obtain a clamping force difference of 15.8 tons, which will cause an uneven force on the tie bar and affect the parallelism of the movable platen and tie bars’ service life.
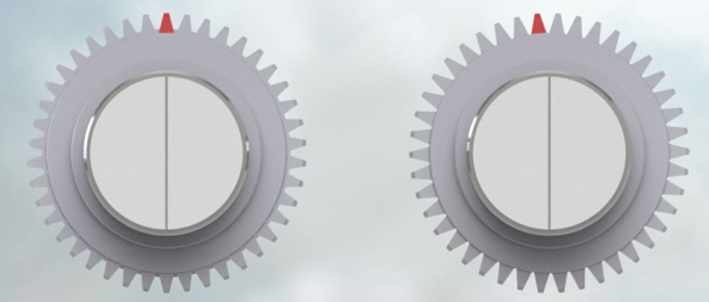
The two platen injection molding machine uses a direct pressure cylinder to stretch the tie bars (as shown in Figure 16). The clamping force can be calculated directly from the system pressure and the action area. The four sets of direct pressure cylinders start pressing quickly and establish accurate clamping force.
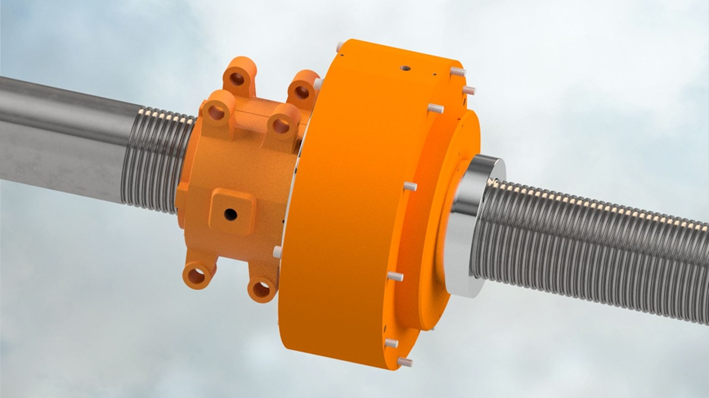
It can be seen from the above that it is quite difficult to adjust the 8 nuts to the same stretching amount for the toggle clamping mechanism, but the direct pressure cylinder of the two platen clamping mechanism is relatively easy. Two platen clamping mechanism ensures that the tie bars are stretched easily. The force balance of the tie bar is guaranteed, and the parallelism of the movable platen and the service life of the tie bars are guaranteed.
5. Machine size
The machine length of the injection molding machine is compared with the same specifications. The toggle type injection molding machine is limited by the motion range of the toggle linkage mechanism. The length of outward toggle injection molding machine is 10.1m, and the length of inward toggle injection molding machine is 11.2 m, The length of both machines is longer than that of the two platen injection molding machine, which the machine length is only 7.9 m.
The overall size of the two platen injection molding machine can reduce the space by more than 20% compared with the same specification of the toggle type injection molding machine (as shown in Figure 17). For customers who produce large plastic products such as car bumpers, car seats, large trash cans or deep buckets, the two platen injection molding machine can have better applications.
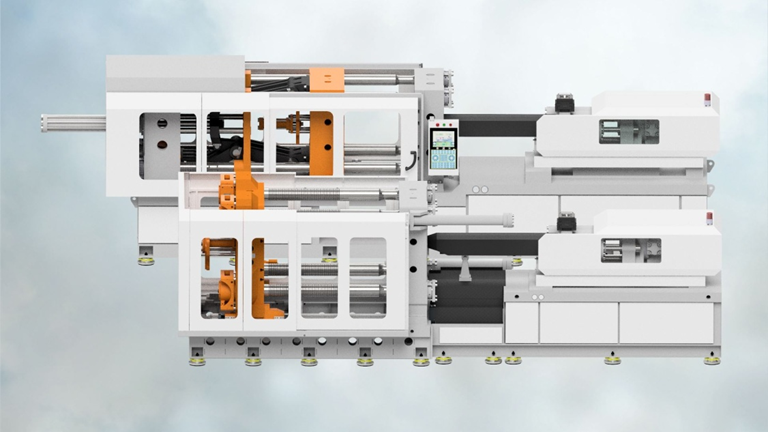
Based on the above summary results, the most reasonable clamping mechanism on the medium-to-large size of injection molding machine is the two platen clamping mechanism. The two platen injection molding machine must meet many precision requirements to ensure structural stability. About the structural stability, it depends on the design of each injection molding machine manufacturer.
The technical research department of Huarong Group has conducted in-depth research on the two platen clamping mechanism, and in view of the advantages of the original two platen injection molding machine, a number of patented technologies are being developed. With standardized assembly operations and rigorous processing technology, the mechanism strength and machine stability of the injection molding machine are ensured.
Previous news : Choosing the Right Injection Molding Machine: A Comprehensive Guide
Next news : 2022 Taipei International Plastics & Rubber Industry Show (TaipeiPLAS) - Huarong will meet you soon!