What is Dual Injection Molding?
2023-03-02 14:38:34
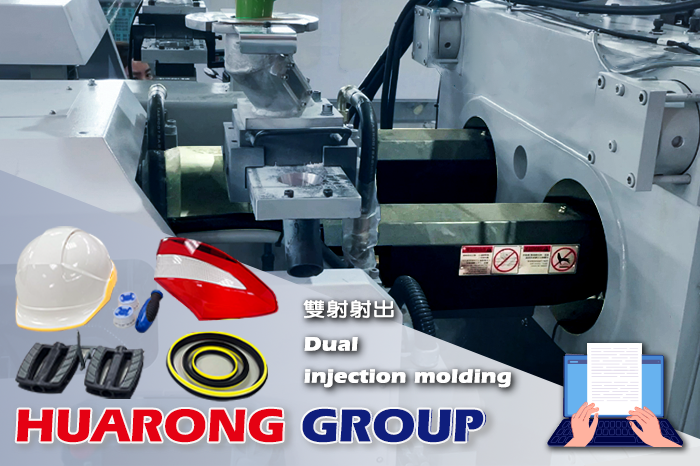
In plastic injection molding, efficiency, quality, and innovation are key. Dual injection molding offers a unique set of advantages for complex plastic parts. While it may seem more complex or expensive at first glance, dual injection molding can actually be a cost-effective solution that enhances functionality and saves time. The following will give a detailed introduction to dual injection molding, its advantages, and its applications.
Dual injection molding, also known as two shot, multi shot, or double shot injection molding, is a commonly used plastic injection molding technology that allows engineers to create multi-material or multi-colored parts without adding extra assembly steps in one molding cycle. This process typically consists of two stages: the first stage involves injecting the first resin into a mold to create the initial part, and the second stage involves overmolding with a second resin. Through this technology, products can with more complex designs and diversified functions. Compared with encapsulation technology, dual injection molding reduces the assembly process and secondary processing costs.
Dual Injection Molding Process in Detail
The dual injection molding process begins with the injection of the first resin into a mold. Once this part cools and solidifies, it is transferred to a second mold where the second resin is injected. The two injection molding materials bond on a molecular level, resulting in a single, multi-material component. Mastery of this process requires technical expertise and precision to avoid issues such as flashes, flow lines, or short-shots.
Dual injection molding offers a range of benefits that make it an attractive option for producing complex plastic parts:
- High Degree of Design Freedom: Double shot molding combines various plastic materials, colors, and textures, allowing for more diversified product designs.
- Cost Reduction: Compared to traditional assembly processes, double shot injection molding can reduce costs associated with operations, labor, and production cycles.
- High Production Efficiency: Dual shot molding can complete the injection and molding of two materials simultaneously, leading to higher production efficiency and more stable product quality.
- Part Consolidation: Reduces the number of components in a finished assembly, saving on development and engineering costs.
- Improved Efficiency: Allows multiple components to be molded with a single tool, reducing labor and post-molding assembly.
- Improved Quality: Enables lower tolerances, high accuracy, and reduced scrap rates.
- Complex Moldings: Allows for the creation of complex mold designs with multiple materials.
Dual injection molding technology injects two different plastic materials into the same mold simultaneously to achieve different color and texture effects. It consists of a "dual injection mold" and a "dual injection molding machine."
Dual Injection Mold
Regarding the dual injection mold, the final plastic product must be considered in the design.
- Product shape and size.
The shape, size, complexity, and other product factors (such as thread) affect the design of the flow channel, cavity, positioning, and opening and closing mechanism of the mold.- Regarding runner and cavity design:
One of the mold design cores is the design of runners and cavities. Designers must base their designs on the final product's shape, size, and structural complexity. They also need to consider the plastic's Physical properties, such as fluidity, injection pressure, filling time, and other factors, to design the flow channel. - Regarding the design of positioning and opening and closing mechanism:
It ensures the precise alignment of the two mold bases (male mold and female mold). When designing these mechanisms, it is necessary to consider mold size, weight, rigidity, and other factors.
- Regarding runner and cavity design:
- Design of mold cooling system.
The design of the mold cooling system affects the production cycle, product quality, and production cost.- Location of the cooling system:
When designing the cooling system, it's at the thickest part of the mold for better cooling of the entire mold - Piping design of the cooling system:
The pipeline should be kept unobstructed to ensure that the cooling water can flow evenly through the entire mold, and enough inlets and outlets should be designed to adjust the flow and pressure of the cooling water.
- Location of the cooling system:
Dual Injection Molding Machine
Regarding the dual injection molding machine, it is necessary to cooperate with the dual injection mold design.
- Injection Unit: The injection molding machine is equipped with two injection systems that can operate independently to process two different materials/colors.
- Clamping Unit: The distance between the tie bars can accommodate two sets of molds (or possibly designing one pair with a left-right symmetrical design), and relying on the rotation of the table (or the shaft), that one-shot injection product is diverted to the two-shot injection to achieve dual injection molding.
Further reading:How to choose a suitable injection molding machine? From the machine itself and plastic product!
Dual injection molding technology has a wide range of applications.
- Auto Parts (in the automotive industry): To produce automotive interiors, exterior parts, lights, doors, and other parts can make auto parts meet higher appearance, function, and performance requirements while reducing production costs
- Home Appliances ( in the houseware industry): Producing various home appliances, such as mobile phone cases, disposable wavetables, buckets, and baskets, can enhance the appearance of the products and their functions and performance.
- Medical Devices (in the medical industry): This includes producing various medical devices, such as syringes and pipeline connectors.
- Sports Equipment (in the sports industry): Producing various sports equipment, such as skateboards, bicycle frames, fitness equipment, etc., can enhance the product's appearance and function.
Dual injection molding technology has a wide range of applications. It can improve product quality and performance while reducing production costs, making it an essential technology in the plastics processing industry.
Further reading:Applications > Video - HUARONG GROUP
To meet the client's design needs, we proposed using dual injection molding for consumer goods, automotive, and other industries. This process allows for combining different materials, colors, and textures in a single process. We used hard and soft materials for the headphone outer cases to achieve a durable yet comfortable design. Similarly, we employed dual injection molding for the hair clips to create intricate designs with multiple colors and textures.
- A successful case of dual-color hair clip: How To Make Your Own Dual Color Hair Clips
- A successful case of headphone outer case: How the Production of Headphone Outer Cases Works
Dual injection molding is a versatile, cost-effective solution for producing complex plastic parts such as headphone outer cases and hair clips. Its ability to combine different materials, colors, and textures in a single process makes it ideal for various applications in the electronics and fashion industries. If you are searching for a dual injection molding machine, Huarong is an experienced injection molding machine manufacturer who offers professional advice; feel free to contact Huarong.
- Group Name: Huarong Group
- Brand: Huarong, Yuhdak, Nanrong
- Service Offerings: Injection Molding Machine, Vertical Injection Molding Machine, Injection Molding Automation
- Tel: +886-6-7956777
- Address: No.21-6, Zhongzhou, Chin An Vil., Xigang Dist., Tainan City 72351, Taiwan
- Official Website: https://www.huarong.com.tw/
Previous news: How the Production of Headphone Outer Cases Works? - Dual Injection Machine
Next news:Injection Molding Machine: Key to Precision Manufacturing of Automotive Parts