How much do you know about the history of injection molding machines?
2023-12-07 16:10:12
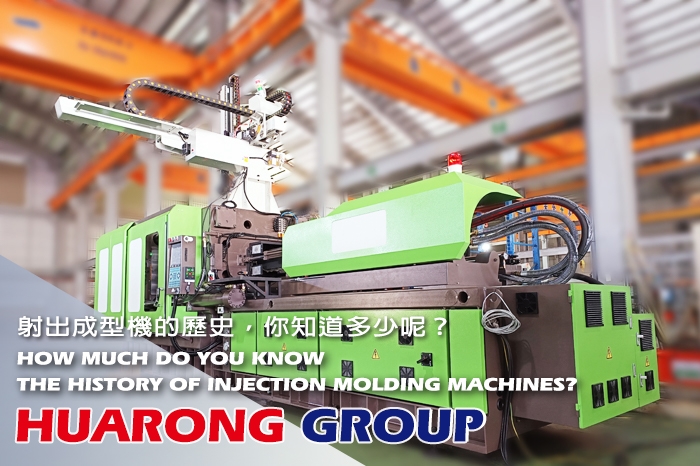
Injection molding machines play a crucial role in the production of many plastic products we use daily. According to research from Emergen Research on November 14, 2023, the global market for injection molding machines reached $17.5 billion in 2022 and is expected to continue growing steadily. The main driving factors for this growth include increased demand from the packaging and automotive industries. So, how much do you know about injection molding machines? As one of the primary production equipment for plastic products, their history and origins are integral to the significant development of modern industrial manufacturing. Let's explore the overview of the history of injection molding technology and machines through this article.
Firstly, let's introduce the basics of injection molding technology. We have introduced the three fundamental aspects of injection molding, with the main concept being the injection of melted plastic into molds after which, with a certain pressure and cooling time, the molds are opened to obtain the finished product. All these actions are carried out in a single cycle by the injection molding machine. Now, let's delve into the earliest records of injection molding.
1. The origins of injection molding:
The earliest thermoplastic to be molded – Celluloid
The earliest thermoplastic material processed into a molded form was celluloid. Alexander Parkes first invented celluloid in 1855, later improved by John Wesley Hyatt in the United States to manufacture products. Originally, celluloid was developed as a substitute for ivory. In the 19th century, billiard balls were made from ivory. However, due to the high demand and limited supply of ivory at the time, billiard ball manufacturers offered a reward for finding an alternative material. It was during this period that Hyatt attempted to create billiard balls using celluloid. However, celluloid proved to be unstable in nature, highly flammable, and prone to cracking. As more plastics emerged, celluloid was gradually replaced, and its usage has become scarce in modern times. Celluloid was used for various products, including table tennis balls, dolls, guitar picks, eyeglass frames, fountain pen bodies, and photographic film.
The production equipment for plastic products - Injection molding machine
American inventor John Wesley Hyatt, together with his brother Isaiah, patented one of the first injection molding machines in 1872. This machine was relatively simple compared to machines in use today. It works by using a plunger to inject plastic through a heated cylinder into a mold. However, the drawback of the plunger is its limited plasticizing ability, as it fails to fully melt the plastic. Additionally, there is a significant loss of injection pressure, making it less commonly used nowadays. Although this method had limited capabilities at the time, it laid the foundation for the future development of injection molding technology. During this period, the applications of injection molding primarily focused on producing small plastic products such as collar stays, buttons, and combs.
The industry expanded rapidly in the 1940s because World War II created a huge demand for inexpensive, mass-produced products. In 1946, American inventor James Watson Hendry built the first screw injection machine, which allowed much more precise control over injection molding process, resulting in a substantial enhancement of product quality and a reduction in production time. The application expanded to the automotive and electronics industries, producing larger and more complex plastic products. Today, screw injection machines account for the vast majority of all injection machines.
2. Modern innovations in injection molding technology
In recent years, injection molding technology has continued to evolve, driven by the demand for even higher precision, faster cycle times, and reduced environmental impact. Another significant advancement is the integration of robotics and automation into injection molding processes. Automation can now be used for tasks such as products removal, quality inspection, and assembly, further streamlining the production process and reducing labor costs.
As a manufacturer of injection molding machines, Huarong not only provides injection molding machines but also offers Turn-key solution, including automation integration services. From pre-sales consultation services to manufacturing during sales and after-sales services, Huarong can meet all your injection molding needs.
3. future outlook of injection molding machines
As mentioned at the beginning of the article, the injection molding machine market is expected to continue growing steadily. With the rise of the Sustainable Development concept, the injection molding industry will focus more on sustainable environmental protection, energy conservation, and carbon reduction in the future, and adapt to changing market demands.
There will be more applications of advanced materials in the future, and the outlook for injection molding machines is full of challenges and opportunities. The entire industry chain will continue to progress, and adhering to the core philosophy of "Quality-Innovation & Industry-Alliance," Huarong will grow hand in hand with our customers, providing reliable injection molding equipment and professional services.
Previous news : HUARONG is honored with the 2024 Taiwan Excellence Award!
Next news : What is Injection Molding Process? 6 Steps in Machine Process