2 Platen Injection Molding Machine vs 3 Platen
2024-03-25 13:58:16
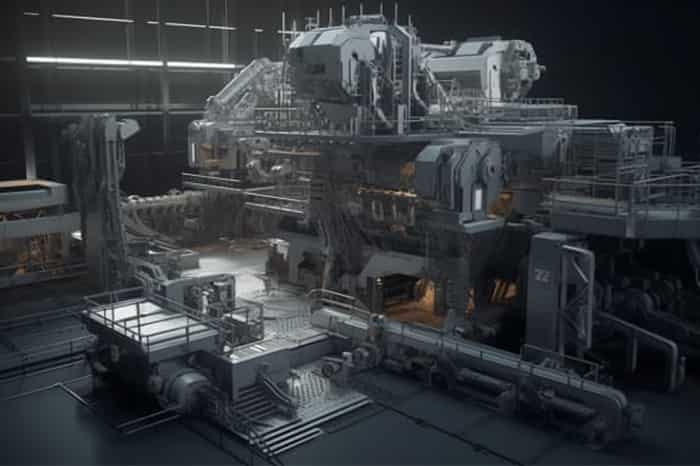
In today's market, 2 platen injection molding machines have emerged as a popular choice, particularly for manufacturing large auto parts, industrial containers, and other products requiring a substantial mold open stroke. This article will explore the two platen and three platen machine differences, benefits, and applications.
Two platen machines primarily use the direct pressure mold clamp system. This system employs four sets of direct-pressure clamping cylinders to generate the clamp force and ensure that the mold remains closed securely.
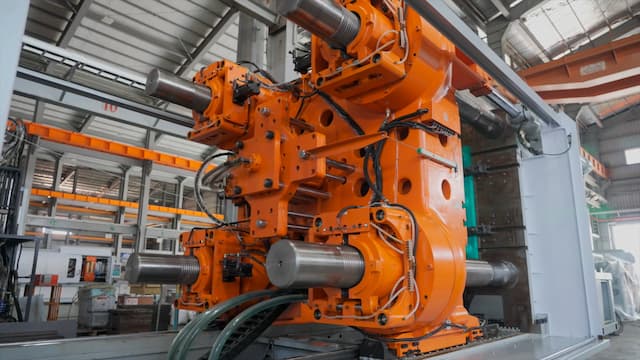
Related product: two platen injection molding machine - NRH series
2 Platen Machine Design
Two platen injection molding machine is composed of a fixed platen, a movable platen, four sets of tie bars, two sets of mold opening and closing cylinders, and four sets of direct pressure clamping cylinders.
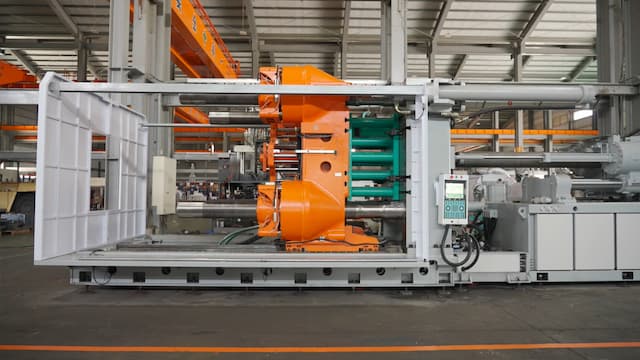
2 Platen Machine Operating Process
The injection molding process of a two platen machine involves the clamping unit closing, injecting the molten material into the mold, cooling, and then opening the mold to eject the finished product.
Benefits and Challenges of 2 Platen Machine
This design offers several benefits, including
- Spatial Efficiency: Due to their compact design, two platen machines require less floor space compared to traditional 3 platen machines, making them ideal for manufacturing environments with limited space.
- High Stability, Precision, and Maintenance: The stationary platen provides increased stability during the injection process, resulting in higher precision and reduced maintenance requirements.
- Large Mold Capacity and Enhanced Accessibility: two platen machines can accommodate larger molds, allowing for the production of larger parts. Additionally, their design provides enhanced accessibility for mold changes and maintenance.
Despite their numerous benefits, two platen machines may face challenges related to higher initial costs and complex mold designs.
2 Platen Machine Applications
The application of two platen injection molding machines is vast and varied, spanning across industries such as automotive, consumer goods, and industrial manufacturing. Their ability to mold medium to large-sized plastic parts with precision and efficiency makes them an indispensable tool in modern manufacturing processes.
- Automotive Industry: These machines are used to produce critical components such as bumpers, instrument panels, and air-conditioner compressor housings.
- Consumer Goods: They are commonly used to manufacture large plastic parts for household appliances, furniture, and industrial containers.
- Industrial Applications: They are often used to produce pallets weighing over 3000 tons, showcasing their capability to handle heavy-duty molding requirements.
Three platen injection molding machines use a toggle link system to generate the clamping force. About the toggle link, the machines can be further divided into inward toggle and outward toggle types which make machine length and mold opening stroke could be different.
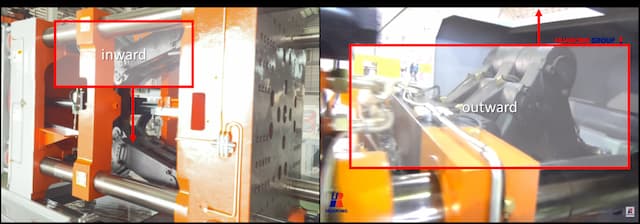
Related product: inward toggle three platen machine - HRN series
Related product: outward toggle three platen machine - NRV series
3 Platen Machine Design
Three platen molding machine is composed of a fixed platen, a movable platen, a die height platen, an I-shaped plate, four sets of tie bars, a set of toggle linkage mechanisms, a set of clamping cylinders, and a set of mold-adjusting gear.
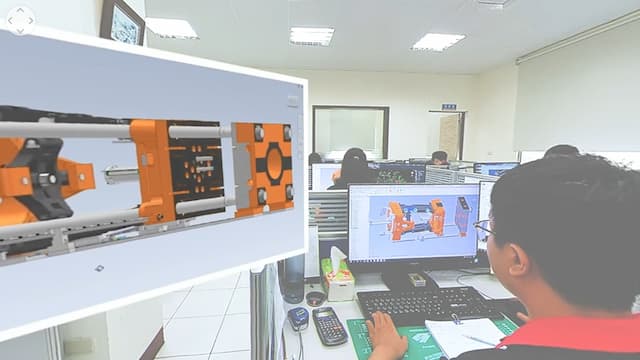
3 Platen Machine Operating Process
The operating process of a 3 platen machine is similar to that of a two platen machine but with an additional platen for increased stability and precision.
Benefits and Challenges of 3 Platen Machine
The toggle design allows for faster mold opening and closing speeds, resulting in reduced cycle times and increased productivity. Compared to two platen machines due to their more complex design, 3 platen machines may have higher maintenance requirements and costs.
3 Platen Machine Applications
Three platen injection machines are commonly used in the production of precision parts and components in industries such as electronics, medical devices, and aerospace.
When comparing two platen and three platen injection molding machines, several factors come into play, including cost, floor space requirements, cycle times, and maintenance needs. While two platen machines offer spatial efficiency and high stability, 3 platen machines provide reduced cycle times and easy mold handling. The choice between these two types of machines ultimately depends on the specific requirements of your manufacturing process.
Further ready: What is injection molding machine? By clamping mechanism to choose injection molding machine model
Both two platen and three platen molding machines have their own unique advantages and challenges. Understanding the differences between these machines can help you make an informed decision when choosing the right injection machine for your manufacturing needs.
Dependable Machine Supplier - Huarong
If you are searching for an experienced injection molding machine manufacturer for two platen injection machines, please feel free to contact Huarong.
- Group Name: Huarong Group
- Brand: Huarong, Yuhdak, Nanrong
- Service Offerings: Injection Molding Machine, Vertical Injection Molding Machine, Injection Molding Automation
- Tel: +886-6-7956777 #521
- Address: No.21-6, Zhongzhou, Chin An Vil., Xigang Dist., Tainan City 72351, Taiwan
- Official Website: https://www.huarong.com.tw/
Previous news : What Is Insert Molding? Process, Advantages and Applications
Next news : Essential for Launching Your Injection Molding Business