Understanding the 10 Most Common Injection Molding Materials
2024-03-29 14:57:50
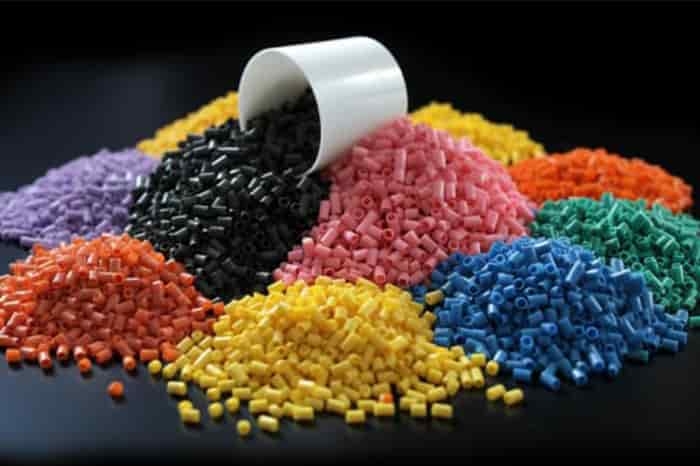
When it comes to plastic materials for injection molding, the options are vast and varied. From common polymers to specialty plastics and polymer blends, each material has its unique characteristics and processing requirements. This comprehensive guide will walk you through the top 10 plastic injection molding materials, discussing their properties and applications.
Choosing the right plastic injection molding material is pivotal in achieving the desired characteristics for your products. Each type of plastic material offers unique properties, making it suitable for specific applications. These are the most common plastic materials for injection molding:
- acrylonitrile butadiene styrene (ABS)
- polyethylene (PE)
- polypropylene (PP)
- polystyrene (PS)
- polycarbonate (PC)
- poly (methyl methacrylate) (PMMA)
- polyvinyl chloride (PVC)
- nylon (polyamide, PA)
- polyoxymethylene (POM)
- bulk molding compound (BMC)
Acrylonitrile Butadiene Styrene (ABS) is a popular thermoplastic polymer known for its versatility and excellent performance characteristics. It is widely used in various industries due to its unique combination of impact resistance, chemical resistance, ease of processing, and excellent surface finish, making it suitable for various applications, from automotive parts to consumer electronics and household appliances.
Processing Considerations for ABS
- Temperature Control: ABS is an amorphous polymer with a broad processing temperature range, typically between 200°C and 250°C. Precise temperature control is essential to prevent degradation and achieve a high-quality finish.
- Mold Design: The mold design should account for the material's shrinkage and flow characteristics. Proper venting is necessary to avoid air traps and surface defects.
- Injection Pressure and Speed: Adjusting the injection pressure and speed is crucial to fill the mold correctly and avoid defects such as sink marks or warping. Higher injection speeds can improve surface gloss and reduce cycle times.
- Drying: ABS is hygroscopic and absorbs moisture from the environment. Proper drying before processing is essential to prevent hydrolysis and defects in the molded parts. Drying at 80°C to 90°C for 2 to 4 hours is recommended.
- Post-Processing: After molding, ABS parts can be easily machined, painted, or plated. Surface treatments can enhance the appearance and performance of ABS components.
Polyethylene (PE) is one of the most widely used plastics globally, known for its versatility, ease of processing, and wide range of applications. It is a polymer made from the polymerization of ethylene and is available in various grades, each with unique properties that make it suitable for different applications, such as packaging, pipes, consumer goods, and more.
Polyethylene is a simple polymer consisting of long chains of ethylene monomers. Its properties can vary significantly depending on its density and branching, leading to different types of polyethylene, such as Low-Density Polyethylene (LDPE), High-Density Polyethylene (HDPE), Linear Low-Density Polyethylene (LLDPE), and Ultra-High-Molecular-Weight Polyethylene (UHMWPE).
Processing Considerations for PE
- Temperature Control: The processing temperature for PE varies depending on its grade. For example, LDPE is typically processed at temperatures between 160°C and 260°C, while HDPE is processed between 180°C and 280°C. Accurate temperature control is essential to prevent degradation and achieve the desired properties.
- Mold Design: The mold design should consider PE’s shrinkage and flow characteristics. Proper cooling and venting are necessary to avoid warping and ensure consistent part quality.
- Injection Pressure and Speed: Adjusting the injection pressure and speed is crucial to fill the mold correctly and avoid defects such as sink marks or warping. Higher injection speeds can enhance surface gloss and reduce cycle times.
- Drying: Although PE is not hygroscopic, ensuring the material is dry before processing can help maintain consistent quality and reduce the risk of defects.
- Cooling Time: PE parts need sufficient cooling time to achieve dimensional stability and avoid warping or shrinkage. Cooling systems should be designed to provide uniform cooling throughout the part.
As one of the most produced plastics in the world, Polypropylene (PP) is a highly versatile thermoplastic polymer widely used in various industries due to its low density, chemical resistance, mechanical strength, thermal stability, and recyclability make it a preferred material in industries such as packaging, automotive, medical, textiles, and construction.
Processing Considerations for PP
- Temperature Control: Proper temperature control is essential for processing PP. The recommended processing temperature ranges from 200°C to 280°C, depending on the specific grade of PP. Precise temperature management helps prevent degradation and ensures high-quality parts.
- Mold Design: Mold design is crucial for achieving optimal part quality. PP tends to shrink upon cooling, so molds must account for shrinkage to ensure dimensional accuracy. Adequate venting and cooling channels help maintain consistent part quality.
- Injection Speed and Pressure: Adjusting injection speed and pressure is vital to fill the mold and avoid defects. Higher injection speeds can help improve surface finish and reduce cycle times, while appropriate pressure ensures proper material flow.
- Drying: Although PP is not hygroscopic, drying the material before processing can help eliminate surface defects and ensure consistent part quality.
- Cooling Time: Adequate cooling time is necessary to achieve dimensional stability and prevent warping or shrinkage. Uniform cooling throughout the part is essential for maintaining quality.
Polystyrene (PS) is a versatile and widely used thermoplastic polymer, offering a unique combination of properties that make it suitable for various applications. Its transparency, rigidity, chemical resistance, and ease of processing make it a preferred material in packaging, consumer goods, medical devices, construction, electronics, and automotive industries.
Processing Considerations for PS
- Temperature Control: PS typically processes at temperatures between 180°C and 240°C. Precise temperature control is essential to avoid degradation and ensure high-quality parts.
- Mold Design: Proper mold design is crucial for achieving optimal part quality. PS tends to shrink upon cooling, so molds must account for shrinkage to ensure dimensional accuracy.
- Injection Speed and Pressure: Adjusting injection speed and pressure is vital to fill the mold and avoid defects. High injection speeds can help improve surface finish and reduce cycle times, while appropriate pressure ensures proper material flow.
- Drying: Although PS is not hygroscopic, drying the material before processing can help eliminate surface defects and ensure consistent part quality.
- Cooling Time: Adequate cooling time is necessary to achieve dimensional stability and prevent warping or shrinkage. Uniform cooling throughout the part is essential for maintaining quality.
Polycarbonate (PC) is a high-performance engineering thermoplastic known for its exceptional toughness, clarity, and thermal stability combination. It stands out due to its remarkable properties, which include high impact resistance, transparency, thermal stability, dimensional stability, electrical insulation, and flame retardancy. Its unique properties make it suitable for various automotive, medical devices, electronics, construction, consumer goods, and optical media applications.
Processing Considerations for PC
- Temperature Control: The recommended processing temperature for PC is typically between 270°C and 320°C. Precise temperature control is crucial to prevent degradation and achieve optimal material flow.
- Drying: PC is hygroscopic, meaning it absorbs moisture from the air. Before processing, it is essential to dry the material to prevent defects such as hydrolysis, which can affect mechanical properties and surface finish. Drying temperatures typically range from 120°C to 125°C for 2 to 4 hours.
- Mold Design: Proper mold design is essential for maintaining dimensional stability and achieving high-quality surface finishes. Mold temperatures should be maintained between 80°C and 120°C to ensure good part quality.
- Injection Speed and Pressure: Adjusting injection speed and pressure is vital for filling the mold and avoiding defects such as flow marks or voids. High injection speeds can improve surface finish, while appropriate pressure ensures proper material distribution.
- Cooling Time: Adequate cooling time is necessary to achieve dimensional stability and prevent warping or shrinkage. Uniform cooling throughout the part is essential for maintaining quality.
Polymethyl methacrylate (PMMA), also known as acrylic, is a modern type of plastic known for its excellent transparency, similar to regular glass. Its exceptional optical clarity, durability, weather resistance, and ease of fabrication make it a preferred material for aesthetic and durability applications such as headlights, taillight covers, and optical lenses.
Processing Considerations for PMMA
- Temperature Control: PMMA typically requires processing temperatures between 180°C and 250°C. Temperature management is crucial to prevent thermal degradation and achieve optimal material flow.
- Drying: PMMA is hygroscopic, meaning it absorbs moisture from the air. Drying the material before processing is essential to prevent defects such as bubbles and surface blemishes. Recommended drying conditions are 80°C to 90°C for 2 to 4 hours.
- Mold Design: Proper mold design is critical for maintaining dimensional stability and achieving high-quality surface finishes. Mold temperatures should be maintained between 40°C and 80°C to ensure good part quality.
- Injection Speed and Pressure: Adjusting injection speed and pressure is vital for filling the mold and avoiding defects such as flow marks or voids. Moderate injection speeds can help achieve a smooth surface finish, while appropriate pressure ensures proper material distribution.
- Cooling Time: Adequate cooling time is necessary to achieve dimensional stability and prevent warping or shrinkage. Uniform cooling throughout the part is essential for maintaining quality.
Polyvinyl Chloride (PVC) is one of the most versatile and widely used thermoplastics globally. Known for its excellent chemical stability, durability, and cost-effectiveness, PVC has applications in various industries for pipes, fittings, window frames, and electrical cables.
Processing Considerations for PVC
- Temperature Control: PVC is sensitive to thermal degradation. The processing temperature should be carefully controlled, typically between 160°C to 190°C for rigid PVC and slightly lower for flexible PVC.
- Stabilizers and Additives: Stabilizers, plasticizers, and other additives are commonly used in PVC formulations to prevent degradation and improve properties. These must be carefully selected based on the intended application.
- Drying: PVC does not typically require drying before processing, but moisture control is essential to prevent defects.
- Mold Design: Proper mold design is critical for achieving dimensional stability and preventing warping. Molds should be designed to accommodate the specific shrinkage characteristics of PVC.
- Injection Speed and Pressure: Adjusting injection speed and pressure is vital to ensure complete mold filling and avoid defects such as flow lines or voids. Moderate to high injection pressures are often used to achieve detailed and accurate parts.
- Cooling Time: Adequate cooling time is necessary to achieve dimensional stability and prevent warping or shrinkage. Uniform cooling throughout the part is essential for maintaining quality.
Exclusive Machine: PVC Injection Machine - PVC Series
Nylon, also known as polyamide (PA), stands out for its impressive range of properties, durability, chemical resistance, and thermal stability. These make it suitable for various demanding applications, such as consumer products, automotive engine covers, gears, bushings, and medical-surgical instruments.
Processing Considerations for Nylon
- Drying: Nylon absorbs moisture, affecting the molding process and final product quality. Pre-drying is essential to reduce moisture content to acceptable levels, typically at 80°C to 90°C for several hours.
- Temperature Control: The processing temperature for nylon typically ranges between 240°C and 280°C, depending on the type. Precise temperature control is necessary to prevent degradation.
- Injection Speed and Pressure: Moderate to high injection speeds and pressures ensure complete mold filling and achieve good surface finish and dimensional accuracy.
- Mold Design: Proper mold design is crucial for nylon parts. Considerations include shrinkage compensation, venting to prevent gas entrapment, and uniform cooling to avoid warping and internal stresses.
- Post-Processing: Annealing can relieve internal stresses and enhance nylon parts' dimensional stability and mechanical properties.
Polyoxymethylene (POM), also known as acetal, is a highly crystalline thermoplastic that stands out for its exceptional balance of mechanical properties, high mechanical strength, low friction and high wear resistance, dimensional stability, chemical resistance, excellent fatigue resistance, good electrical insulation, and low moisture absorption, which make it suitable for a variety of high-performance applications.
Processing Considerations for POM
- Drying: Although POM has low moisture absorption, it should still be dried before processing to prevent hydrolysis and achieve optimal mechanical properties.
- Molding Temperature: The processing temperature for POM typically ranges from 190°C to 230°C. Precise temperature control is essential to avoid degradation and achieve the desired mechanical properties.
- Injection Pressure and Speed: Moderate to high injection pressures and speeds are recommended to ensure complete mold filling and to minimize defects such as voids and sink marks.
- Mold Design: Proper mold design is crucial for POM parts. Considerations include shrinkage compensation, venting to prevent gas entrapment, and uniform cooling to avoid warping and internal stresses.
- Post-Processing: Annealing can relieve internal stresses and enhance POM parts' dimensional stability and mechanical properties.
Bulk Molding Compound (BMC) is a thermosetting resin composed primarily of special unsaturated polyester and various fillers, reinforcements, and additives. It exhibits excellent electrical insulation properties, heat resistance, flame resistance, high mechanical strength, dimensional stability, corrosion resistance, water resistance, and shrinkage stability. Among various thermosetting molding materials, BMC is considered the highest grade. It finds wide application in various electrical products, communication, and information equipment components, automotive parts, insulation coatings for electric tools, ultra-quiet motors, food utensils, and more.
Processing Considerations for BMC
To achieve high-quality BMC parts, careful attention must be paid to various processing factors:
- Molding Temperature: The processing temperature for BMC typically ranges from 120°C to 180°C, depending on the specific formulation. Precise temperature control ensures proper curing and minimizes voids and defects.
- Mold Design: Proper mold design is crucial for BMC parts. Considerations include gate design, venting to prevent gas entrapment, and cooling to ensure uniform curing and minimize warping.
- Injection Pressure and Speed: Moderate injection pressure and speed are typically used for BMC to ensure complete mold filling and minimize voids.
- Curing Time: BMC requires sufficient curing time to achieve full cure and optimal mechanical properties. The curing time can vary depending on the part size and thickness.
Exclusive Machine: Bulk Molding Injection Machine - HMC Series
Here's a table comparing the properties of the above 10 common plastic injection molding materials:
Choosing the right plastic injection molding material for your high-quality products is a critical decision that can significantly impact their quality, durability, and performance. You can make an informed decision that meets your needs by considering application requirements, material properties, cost considerations, and environmental impact. Conducting thorough research, consulting with suppliers, and implementing testing and quality control measures will further enhance the success of your injection molding process.
Injection Molding Machine Supplier
Huarong Group understands the importance of selecting the right materials for injection molding processes. As a leading injection molding machine manufacturer, we are committed to providing comprehensive solutions to meet your manufacturing needs. Contact Huarong today to discover how we can help you achieve exceptional results in your injection molding endeavors.
- Group Name: Huarong Group
- Brand: Huarong, Yuhdak, Nanrong
- Service Offerings: Injection Molding Machine, Vertical Injection Molding Machine, Injection Molding Automation
- Tel: +886-6-7956777
- Address: No.21-6, Zhongzhou, Chin An Vil., Xigang Dist., Tainan City 72351, Taiwan
- Official Website: https://www.huarong.com.tw/
Previous news: Essential for Launching Your Injection Molding Business
Next news : Large and Medium Injection Molding|Plastic Machine Experts