Comprehensive Guide to Vertical Injection Molding Machines
2024-05-30 11:42:00
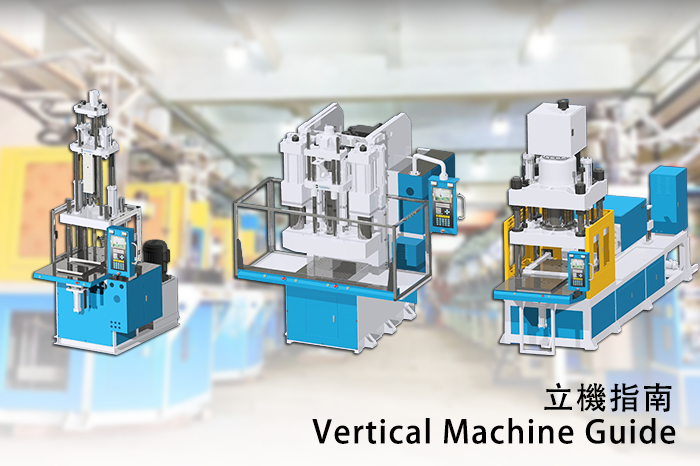
Vertical injection molding machines are crucial in various manufacturing sectors, especially in producing high-precision plastic components. Unlike traditional injection molding machines, these machines operate on the vertical axis, offering specific benefits for different applications. This comprehensive guide will explore the different types of vertical injection molding machines, their specific uses, and how they can enhance manufacturing processes.
Choosing the right vertical injection molding machine is a critical step in optimizing manufacturing processes and ensuring high product quality. The various configurations, including injection units, structures, and templates, are designed to meet specific insert molding requirements. Customer can configure the three parts to combine a machine to meet their injection molding needs tailored to different applications.
Injection Units – Vertical, Horizontal, or Multi-Shot
1. Vertical Injection Unit
The vertical injection unit is commonly configured and requires less floor space. It is used for precision molding small shot-weight parts and overmolding applications. It offers excellent control and is ideal for insert molding processes.
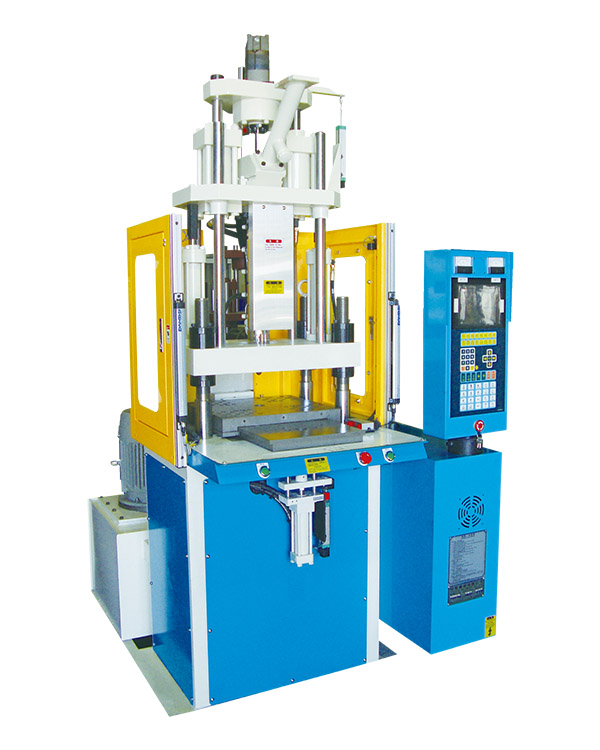
Advantages:
- Twin injection cylinder balanced for smooth and powerful injection.
- Suitable for overmolding and insert molding.
- Compact design saves floor space.
2. Horizontal Injection Unit
Horizontal injection units are designed for applications requiring large shot-weight parts and overmolding applications. This machine can have wider tie-bar distance and its injection seat height is adjustable, allowing more flexibility in mold design. It is ideal for larger components and provide consistent performance across various plastic types.
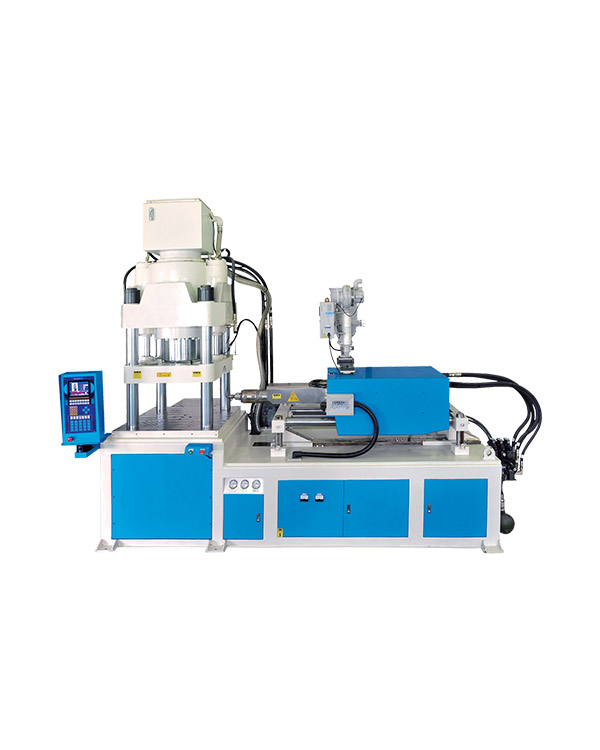
Advantages:
- Higher injection volume capability.
- Consistent performance for larger parts.
3. Multi Injection Unit
Multi injection units are versatile systems that allow for the simultaneous injection of multiple materials or colors. They are perfect for complex parts that require multiple material properties.
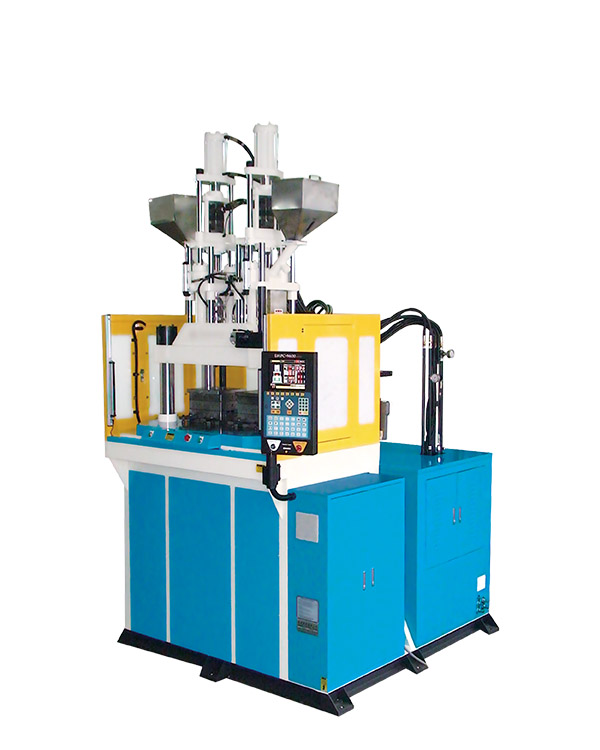
Advantages:
- Multi-material and multi-color capabilities.
- Suitable for complex and functional parts.
- Enhances product aesthetics and functionality.
Structures – Tie-Bar or Tie-Barless
1. Tie-Bar
Tie-bar structures provide robust support and precise alignment of molds, making them suitable for high-pressure applications and large molds.
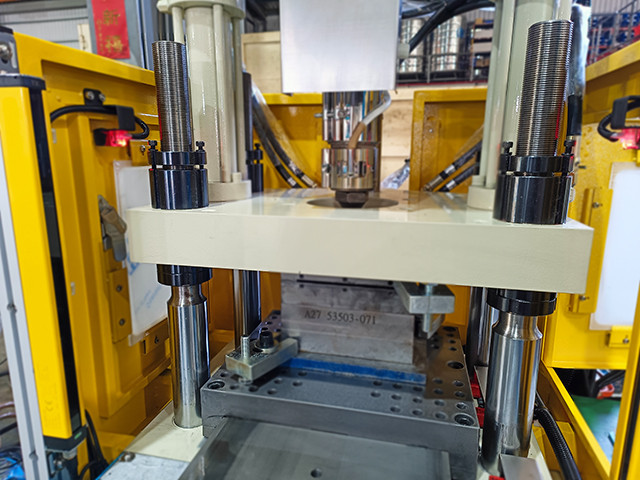
Advantages:
- High rigidity and stability.
- Precise mold alignment.
- Suitable for high-pressure applications.
2. Tie-Barless
Tie-barless structures have three open spaces to offer greater flexibility and accessibility, particularly for products with special long strips or wires. They are easier to operate and can also be used with automatic wiring planning. Tie-barless structures are ideal for applications requiring long embedded parts and can seamlessly integrate with automation processes.
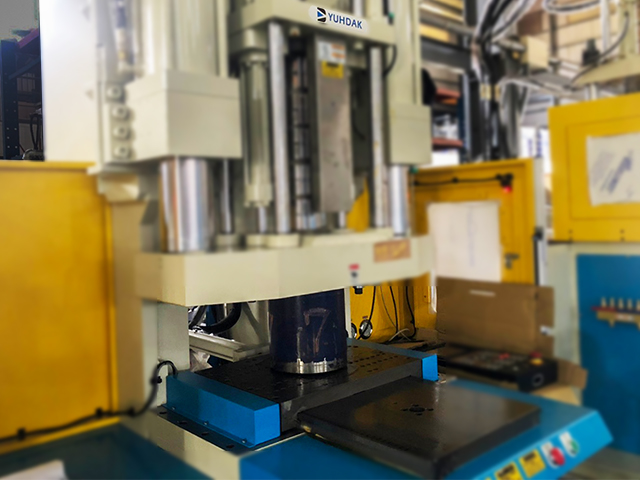
Advantages:
- Greater mold accessibility.
- Easier mold changes.
- Suitable for products with long strips or wires.
- Ideal for integrating with automated wiring systems.
Templates– Fixed Bottom Platen, Sliding Table, or Rotary Table
1. Fixed Bottom Platen
The fixed bottom platen provides a stable base for molding, ensuring consistent product quality and reducing maintenance needs.
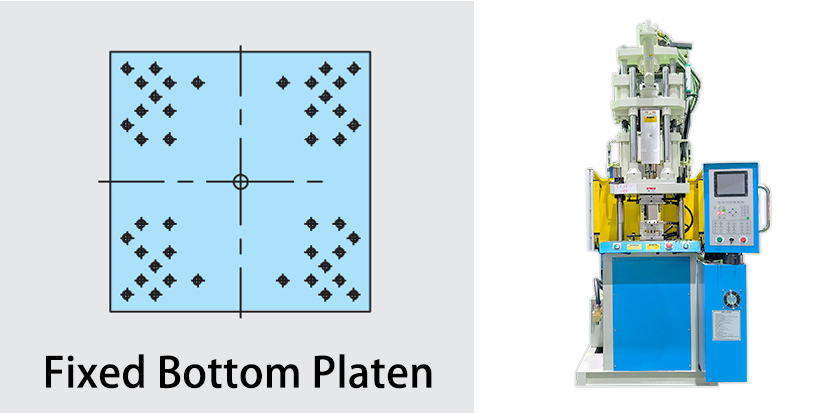
Advantages:
- Stability and durability.
- Consistent product quality.
- Low maintenance requirements.
2. Sliding Table– Single Sliding Table (1S), 180° Double Sliding Table (2S), or 90° Double Sliding Table (2SL)
- Single Sliding Table (1S):
A single sliding table allows the male mold to slide away from the tie-bars, requiring a smaller mold opening stroke and making it easier to insert objects and remove finished products.
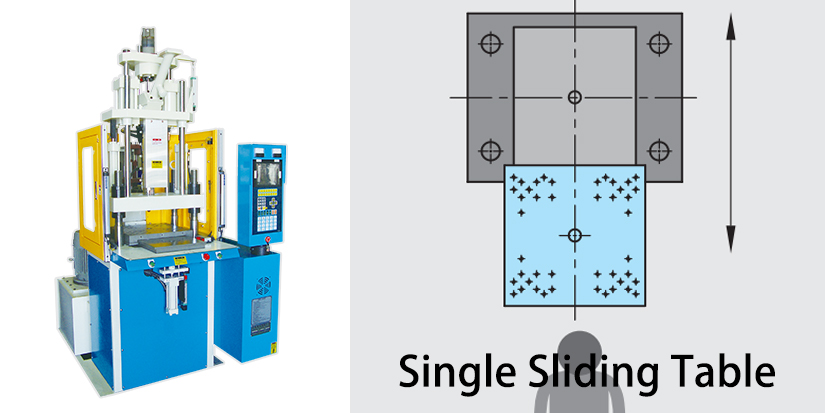
- 180° Double Sliding Table (2S):
The 180° double sliding table allows two male molds for continuous operation, significantly increasing production throughput.
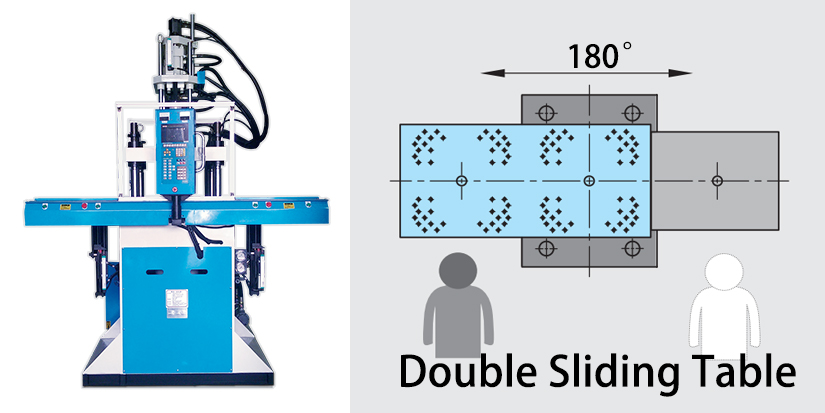
- 90° Double Sliding Table (2SL):
The 90° double sliding table allows for continuous operation by alternating between two molds, is designed for applications requiring one operator to perform the actions of two male molds at a fixed position.
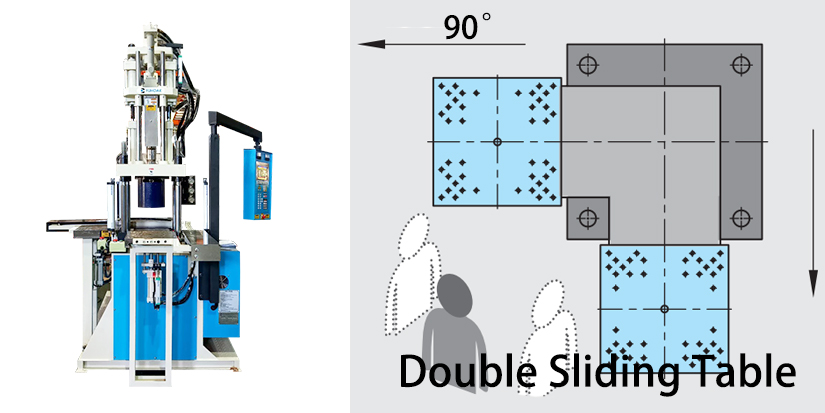
Advantages:
- Reduced downtime.
- Improved production efficiency.
- Enhanced operational accuracy.
3. Rotary Table
Rotary tables are ideal for complex and multi-component molding processes, offering flexibility and efficiency in handling multiple molds.
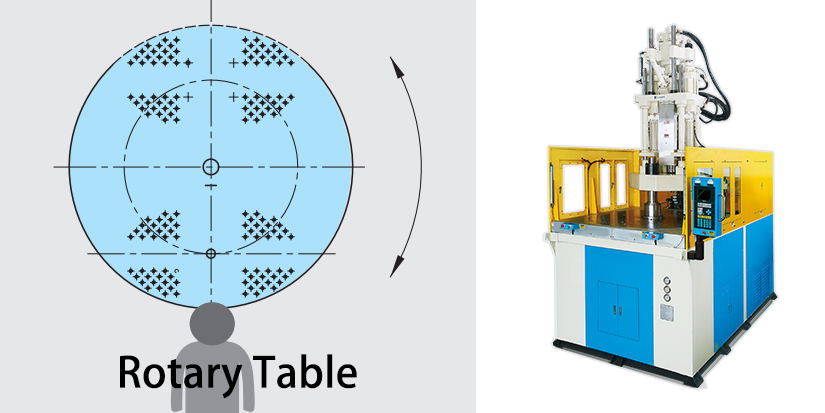
Advantages:
- Flexibility in mold handling.
- Efficient multi-component molding.
- Suitable for complex production needs.
When selecting a vertical injection machine, it is essential to consider the specific requirements of your application. You can create a customized solution that meets your precise molding needs by configuring the injection unit, structure, and template. Here is a step-by-step guide to help you make the right choice:
Step 1: Determine Your Injection Requirements
- Assess the volume and type of materials you will be injecting.
- Choose vertical, horizontal, or multi-injection units based on your injection mold design or production needs.
Step 2: Choose the Appropriate Structure
- Consider the size and shape of your molds.
- Decide between tie-bar and tie-barless structures depending on the required mold accessibility and stability.
Step 3: Select the Template Configuration
- Evaluate the complexity and precision required for your molds.
- Choose from fixed bottom platen, single sliding table, double sliding table, or rotary table based on your operational efficiency needs.
Complete Vertical Machine Models: https://www.huarong.com.tw/page/product/en/vertical-injection-molding-machine/
Understanding the various types of vertical injection molding machines and their configurations, you can select the right combination of injection units, structures, and template to achieve optimal performance, efficiency, and product quality. For further assistance in choosing the perfect vertical injection molding machine for your needs, please contact Huarong who are an experienced injection molding machine manufacturer ready to help you find the best solution.
- Group Name: Huarong Group
- Brand: Huarong, Yuhdak, Nanrong
- Service Offerings: Injection Molding Machine, Vertical Injection Molding Machine, Injection Molding Automation
- Tel: +886-6-7956777
- Address: No.21-6, Zhongzhou, Chin An Vil., Xigang Dist., Tainan City 72351, Taiwan
- Official Website: https://www.huarong.com.tw/
Previous news : Transforming Home Appliance Manufacturing: A Success Story with Huarong's Injection Molding Machines
Next news : How to Change a Mold? Mold Change Process for Efficient Mold Loading and Unloading