Learning Injection Molding Machine Components, Parts and Functions
2024-06-19 16:04:21
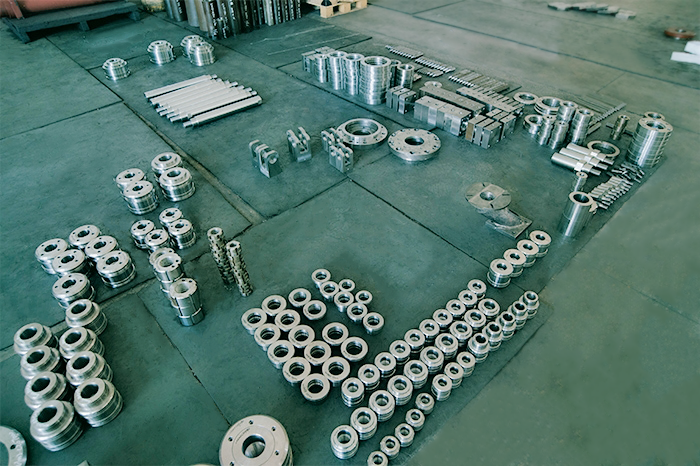
Injection molding machine components are the backbone to ensure smooth production, driving the production of a vast array of plastic products with precision and efficiency. Here we split Huarong’s injection molding machine into three main units and introduce their respective components in order. Read on to discover how each component contributes to the overall functionality and performance of these essential machines.
An injection molding machine is composed of three critical units and several components that work in unison to produce high-quality plastic parts by injection molding process. In the following sections, we will explore the clamping unit, the injection unit, and the power unit.
Clamping Unit
The clamping unit is one of the three main sections of an injection molding machine, and its primary function is to hold the mold together during the injection, molding and cooling process. This unit must apply significant force to keep the mold closed and prevent plastic from leaking out. The clamping unit also opens the mold after the part has cooled, allowing for ejection.
Injection Unit
The injection unit is responsible for melting and injecting the plastic material into the mold. It consists of a barrel, screw, and nozzle. The screw rotates to melt the plastic and then moves forward to inject it into the mold cavity. The speed and pressure of the injection process are crucial for producing high-quality parts.
Power Unit
The power unit provides the necessary energy to operate the clamping and injection units. It typically includes hydraulic or electric systems, which generate the force required for the machine’s operations. The choice between hydraulic and electric power units depends on the specific needs of the manufacturing process, with each having its own advantages.
Further reading: What are Fundamentals of Injection Molding? 3 Keys to Plastic Injection Plant
1. Toggle
The toggle is a mechanical linkage system used in the clamping unit of the machine. The primary function of the toggle mechanism is to generate and maintain the clamping force required to keep the mold halves closed during the injection, molding and cooling phases of the molding cycle.
2. Platen
Platens are the large plates to which the mold halves are attached. The movable platen is driven by the clamping unit to open and close the mold, while the stationary platen remains fixed. They are crucial for maintaining the alignment and stability of the mold during the injection process. Clamping strength distributed evenly to the platens can prevent mold deformation.
3. Ejection Hydraulic Cylinder
This component is part of the ejector system and is fixed on the movable platen. The ejection hydraulic cylinder provides the force needed to eject the part, adjust the suitable ejector stroke by setting the proximity switch and potentiometer, and push the finished part out of the mold.
4. Clamping Hydraulic Cylinder
Clamping unit is driven by the clamping hydraulic cylinder, through the toggle to drive platen, clamping toggle magnifying power to clip mold tight, and maximum clamping force.
5. Tie-bar
Tie-bars are the steel rods that guide and support the movable platen. Huarong's patented tie-bars adopt the patented design of non-rigid absorption method to improve the stability of the platens and avoid breakage of the platen tie-bars.
Further reading: What is injection molding machine? By clamping mechanism to choose injection molding machine model
1. Barrel and Screw
The barrel and screw are central to the injection unit. The screw rotates to melt the plastic material as it moves through the barrel. Once the material is melted, the screw acts as a plunger, injecting the molten plastic into the mold cavity through the nozzle.
2. Nozzle
The nozzle is the final point of contact between the injection unit and the mold. It directs the molten plastic into the mold cavity. Nozzles come in various designs, each suited for different types of molding processes and materials.
3. Heater Band
Heater bands are wrapped around the barrel to maintain the necessary temperature for melting the plastic. They ensure consistent and efficient heating, also ensure enough molding ability.
4. Material Charging Hydraulic Motor
This motor drives the screw rotation during the material melting phase. It ensures a consistent feed of plastic material into the barrel.
5. Dual Twin-Hydraulic Cylinder
This component active injection to promote screw forward, to squeeze material into mold to molding, backward is to prevent material overflow. Dual twin-hydraulic cylinders offer improved stability and accuracy, enhancing the overall performance of the machine.
1. Hydraulic vs. Electric Systems
Hydraulic systems use fluid power to generate the necessary force for machine operations, while electric systems use motors. Hydraulic systems are known for their high force capacity and robustness, while electric systems offer greater energy efficiency, precision, and cleanliness.
2. Servo Motor
Servo motors are used in modern injection molding machines to provide precise control over the injection and clamping processes. They offer high efficiency and accuracy, leading to improved part quality and reduced energy consumption.
Safety features are important in injection molding machines to protect operators and maintain safe working conditions. Common safety mechanisms include emergency stop buttons, safety doors, and interlocks that prevent the machine from operating when the mold area is accessible. Additionally, pressure sensors and alarms help monitor and control the machine’s operations, reducing the risk of accidents.
When it comes to safety doors, Huarong’s injection molding machine was designed with Outward-opening Safety Door, which is for easy opening / closing, spacious opening, convenient and time-saving for mechanical maintenance.
After learning the injection molding machine components, regular maintenance is important, which ensures the longevity and optimal performance of injection molding machines. Routine tasks include inspecting and lubricating moving parts, checking hydraulic fluid levels, and cleaning the machine to prevent buildup of debris. Addressing common issues such as leaks, wear and tear, and calibration errors promptly can prevent costly downtime and extend the machine’s lifespan.
In conclusion, understanding the injection molding machine components and the functions might help you get better success in the industry. And by maintaining these machines properly and staying informed about the latest advancements, manufacturers can ensure efficient production and high-quality output. At Huarong, we are committed to providing state-of-the-art injection molding solutions to meet the diverse needs of our customers. Have any question about injection molding machine components? Contact Huarong, let us help you learn more about the fascinating injection molding machines world!
- Group Name: Huarong Group
- Brand: Huarong, Yuhdak, Nanrong
- Service Offerings: Injection Molding Machine, Vertical Injection Molding Machine, Injection Molding Automation
- Tel: +886-6-7956777
- Address: No.21-6, Zhongzhou, Chin An Vil., Xigang Dist., Tainan City 72351, Taiwan
- Official Website: https://www.huarong.com.tw/
Previous news: How to Change a Mold? Mold Change Process for Efficient Mold Loading and Unloading
Next news: Essential Injection Molding Machine Spare Parts for Optimal Performance