Injection Molding Machine Spare Parts for Optimal Performance
2024-06-21 11:25:32
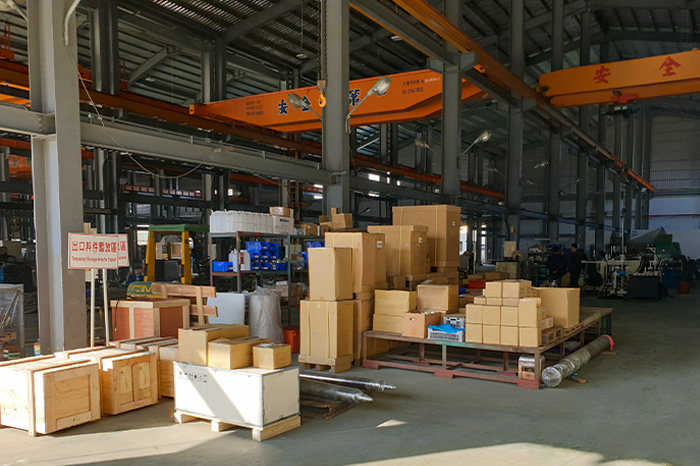
Injection molding machines are indispensable in producing plastic products, ranging from everyday items to specialized industrial components. However, regular maintenance and the right spare parts are crucial to maintaining high efficiency and product quality.
Proper maintenance of injection molding machines not only extends their lifespan, improves production efficiency, and ensures product quality. Here are the key reasons why maintenance is vital:
- Extending Equipment Lifespan: Regular upkeep reduces equipment damage and failure rates, reducing costly replacements and repairs.
- Boosting Production Efficiency: Well-maintained machines operate smoothly, reducing downtime and improving overall productivity and stability.
- Ensuring Safety: Regular checks and maintenance help prevent accidents and safety risks, ensuring a safer working environment.
- Enhancing Product Quality: Maintenance ensures the precision and stability of the machines, leading to higher quality products and better market competitiveness.
- Reducing Costs: Identifying and fixing issues early through regular maintenance helps avoid expensive repairs and prolongs the machine’s operational life.
Further reading: Injection Molding Machine Maintenance PDF and Checklist
Maintaining an injection molding machine often requires replacing various mechanical, electrical parts, and hydraulic spare parts. Below are some of the critical spare parts:
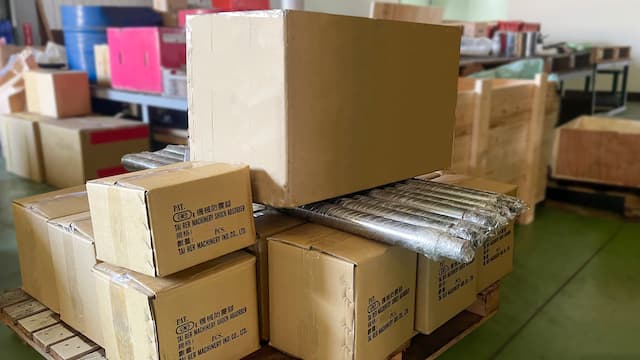
Mechanical Spare Parts
The spare parts for the machine's structure can be categorized into "Oil Pumps, Screws and Barrels, Hydraulic Motors, Screw Tips, Check Rings, and Ring Stopping (Screw Tip Set)” based on information obtained from the Internet. However, given the current state of the injection machine, only the screw tip set should be necessary for the machine structure. If the customer's plastic is reinforced with fiberglass (+GF), we also suggest considering the barrel set.
- Screw Tip Set: The screw tip set is crucial in the injection process. It controls the molten plastic, ensures that the plastic passes through, maintains it, and prevents plastic backflow. Proper sealing and material flow will result in some wear over time. Regular inspection and replacement of worn parts can maintain the machine's efficiency.
- Screw Tip: This guides the flow direction of the injection.
- Check Ring: Blocks and secures the seal ring to prevent backflow during injection.
- Ring Stopping: Prevents molten plastic from leaking backward during injection, avoiding backflow and pressure loss.
- Barrel Set: The Barrel tip and barrel are subjected to high wear under the injection molding material with fiberglass. Using a high-quality barrel set ensures consistent plasticizing and injection performance.
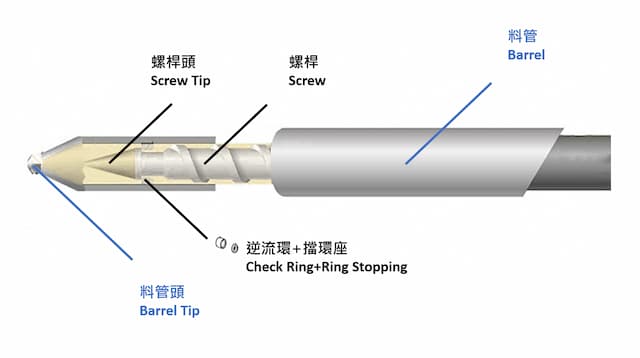
Electrical Spare Parts
- Heater Bands: Ceramic or aluminum heater bands ensure consistent temperature control for material melting.
- Sensors and Transducers: Provide critical feedback for machine operation to ensure the accurate movement of machine components. Regular checks and replacements maintain precision in the molding process.
- Potentiometers: The potentiometer measures displacement and length in control and measurement systems, outputting a DC voltage signal. It sends electronic pulses along a waveguide wire, which returns to the device upon encountering a magnetic field, allowing precise position calculation. Regular inspection and replacement are crucial for maintaining accurate and stable machine operations.
- Directional, Relief, and Proportional Valves: Valves control the flow of hydraulic fluid. Regular maintenance and timely replacement ensure the machine operates smoothly.
- Relays and Switches: Heating relays and limit switches control various aspects of the machine’s operation. Regular checks and replacements prevent operational disruptions.
- Control System Panels: The control system panel is the central hub of an injection molding machine, where operators can monitor and adjust various settings to ensure optimal performance. Spare parts for control panels may include buttons, switches, display screens, and electronic components.
- Main Boards: The main board, or motherboard, is the backbone of the control system and is responsible for processing and coordinating the machine's operations
- Temperature Boards: Temperature boards regulate the temperature of various components in the injection molding machine, such as heaters and heating bands.
Hydraulic Spare Parts
For the hydraulic system, we recommend keeping spare parts such as oil seals and sealing rings for hydraulic cylinders and solenoid valves to maintain the machine's hydraulic efficiency.
- Oil Seals: Oil seals are essential components in hydraulic cylinders. They prevent hydraulic fluid from leaking and ensure the cylinder's efficient operation.
- Sealing Rings: Sealing rings, or O-rings, are used in hydraulic systems to create a tight seal between moving parts such as pistons and cylinders. These rings prevent hydraulic fluid from leaking and maintain the pressure required for efficient operation.
- Solenoid Valves: Solenoid valves control the flow of hydraulic fluid in the system, directing it to different parts of the machine as needed. Proper functioning of solenoid valves is crucial for the overall performance of the injection molding machine.
Other Parts
Huarong recognizes the importance of spare parts. When exporting overseas, we will provide a spare part list based on the customer's specific requirements, such as a lubrication kit set, nylon pipe, buffer, etc. If you have relevant needs, please contact Huarong and provide your machine model and serial number.
- Regular Inspection and Cleaning: Dust and debris accumulation can cause significant damage if not addressed promptly. Routine inspections are essential for maintaining injection molding machines.
- Proper Check of Electrical System: Checking wiring, connectors, and electrical components for signs of wear or damage. It can prevent electrical failures and ensure all safety interlocks and sensors function correctly.
- Proper Lubrication of Moving Parts: Ensuring all moving parts are adequately lubricated to minimize friction that reduces friction, prevent overheating, and minimize wear. Besides, using the right type of lubricant recommended by the manufacturer is essential.
- Proper Check of Hydraulic System: Checking for leaks, maintaining appropriate fluid levels, and ensuring the hydraulic fluid is clean and uncontaminated.
- Proper Maintenance of Cooling System: Regular maintenance of cooling towers, chillers, and cooling circuits ensures they function efficiently to prevent overheating.
- Staff Training: Regularly train staff on maintenance procedures and best practices.
Further reading: Maximizing Injection Molding Machine Efficiency Through Preventive Maintenance
1. How often should injection molding machines be maintained?
Effective maintenance planning is essential and can significantly reduce failures and improve efficiency. It's recommended to schedule daily inspections for common failures and weekly inspections for less frequent issues.
We wrote an article on Injection Molding Machine Maintenance PDF and Checklist to perform maintenance for different machine parts and the use time. Designated personnel must oversee the maintenance and ensure the work is carried out effectively according to schedule.
2. What are the signs of wear in injection molding machines?
Common signs include unusual noises, decreased product quality, and increased downtime.
3. How do I choose the right lubricant for my injection molding machine?
Refer to the machine’s manual for recommended lubricants to ensure compatibility and effectiveness.
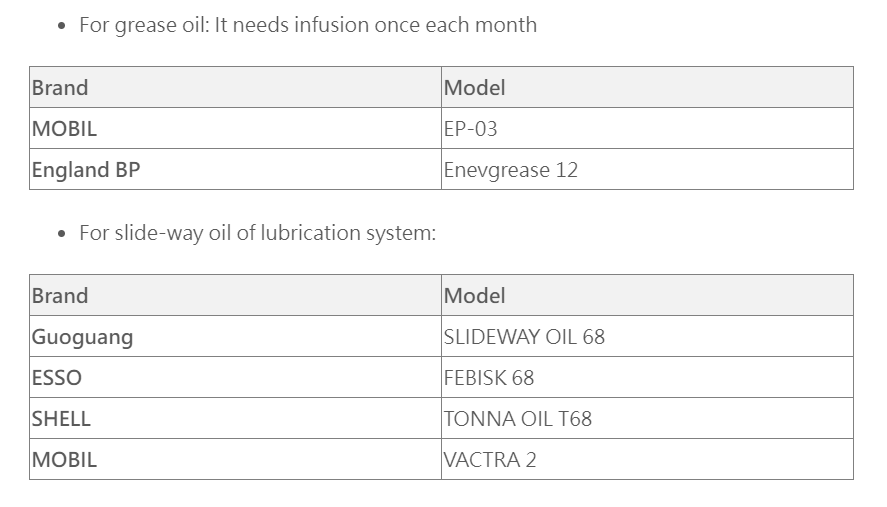
Maintaining a plastic injection molding machine requires regular monitoring, timely spare parts replacement, and adherence to maintenance schedules. Understanding the essential spare parts and implementing proper maintenance practices ensures efficient and cost-effective production. If you have any questions about injection molding or are searching for an experienced injection molding machine manufacturer, don't hesitate to contact Huarong.
- Group Name: Huarong Group
- Brand: Huarong, Yuhdak, Nanrong
- Service Offerings: Injection Molding Machine, Vertical Injection Molding Machine, Injection Molding Automation
- Tel: +886-6-7956777
- Address: No.21-6, Zhongzhou, Chin An Vil., Xigang Dist., Tainan City 72351, Taiwan
- Official Website: https://www.huarong.com.tw/
Previous news : Learning the Injection Molding Machine Components & Functions
Next news : Case Study: Best PVC Pipe Fitting Machine for Your Business