Comprehensive Guide to Injection Molding Robots: Automate Your Production Process
2024-07-08 11:01:29
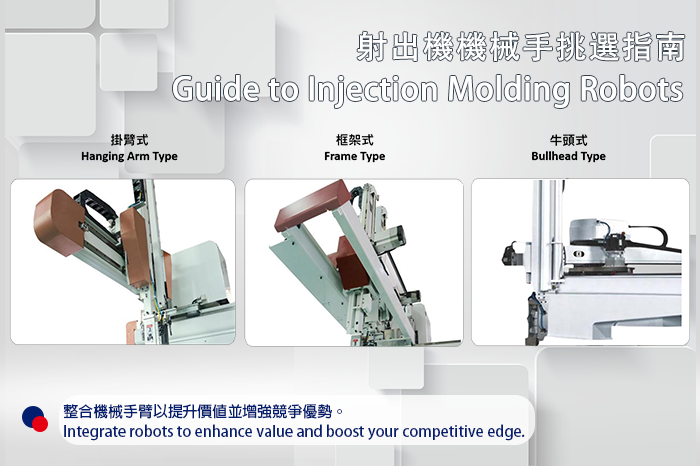
Plastic manufacturing is evolving rapidly, and automation is at the forefront of this transformation. Injection molding robots are no longer a luxury but necessary for companies aiming to stay competitive. Manufacturers can enhance productivity, ensure safety, and maintain high quality by automating various tasks within the injection molding process. This guide explores the types of injection molding robots, applications, and key considerations for integrating robots into your production line.
Traditional injection molding involves manual loading and is reliable but labor-intensive and prone to human error. Instead, automated injection molding uses robots to handle the repetitive loading and unloading tasks. It reduces labor costs and ensures greater precision and consistency in the production process.
Insert Molding
Insert molding involves encapsulating a preformed component, known as an insert, typically metal or plastic, which is placed into the mold cavity, and molten plastic is injected around it, bonding the materials together as the plastic cools and solidifies. Incorporating injection molding robots into the insert molding process can handle small parts accurately, reducing errors and enhancing quality. Besides, using robots in insert molding reduces the need to manually handle inserts and finished parts, minimizing the risk of workplace injuries.
Related product: Vertical Injection Molding Machine
Further reading: What Is Insert Molding? Process, Advantages and Applications
Overmolding
Overmolding is a process in which a single part is created using multiple materials. It typically involves molding a soft material over a hard substrate. Injection molding robots enhance the efficiency, accuracy, and consistency of the overmolding process.
Further reading: What Is Overmolding? Overmolding Process, Example and vs Insert Molding
Post-Processing and Recycling
Robots perform various post-processing tasks, including drilling, trimming, and recycling. Trimming and drilling are crucial for ensuring final product quality. Recycling excess plastic from the molding process optimizes material usage and maintains production line efficiency.
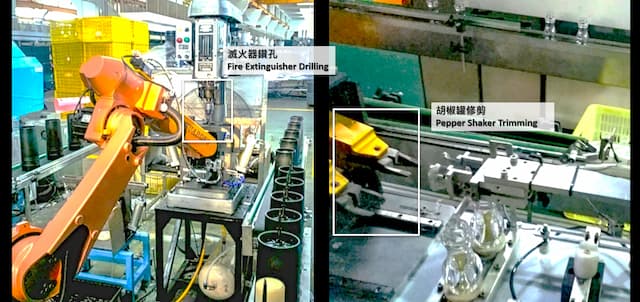
In-Mold Labeling
In the in-mold labeling process, before each mold cycle begins, the mold opens, and a robot takes the pre-printed label film and precisely places it in the designated position within the mold. The printed side of the label faces the inner wall of the mold and is firmly fixed inside the mold through small holes and a vacuum suction device. The plastic material is heated during this process, forming a tubular shape that enters the mold vertically. With the label already secured on its inner wall, the mold closes quickly, ensuring that the label adheres tightly to the plastic surface during the molding process. This automated step not only ensures the consistency of the label on the product but also enhances the appearance and overall quality of the final product.
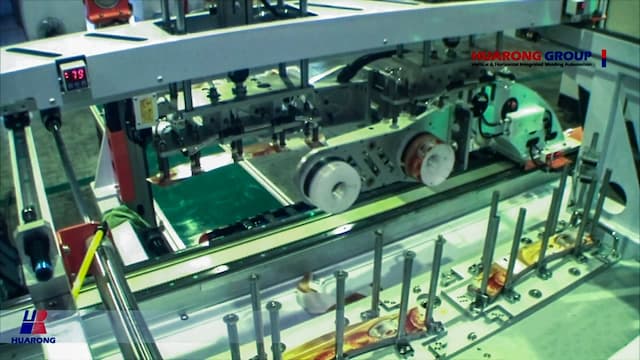
Related product: In molding labeling machine - IML series
Further reading: What is IML? In Mold Labeling Process, Benefits, and Applications
Assembly
In the assembly of plastic components, speed and precision are paramount. Robots outperform humans in repetitive assembly tasks, significantly enhancing production throughput.
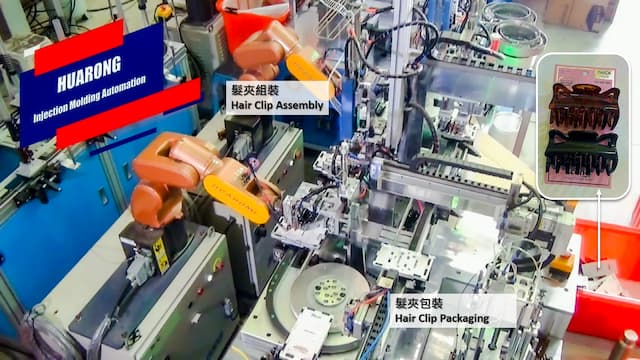
By automating various tasks within the injection molding process, linear robots equipped with linear guides are widely used. They operate along specific directional axes, primarily categorized into the X, Y, and Z axes.
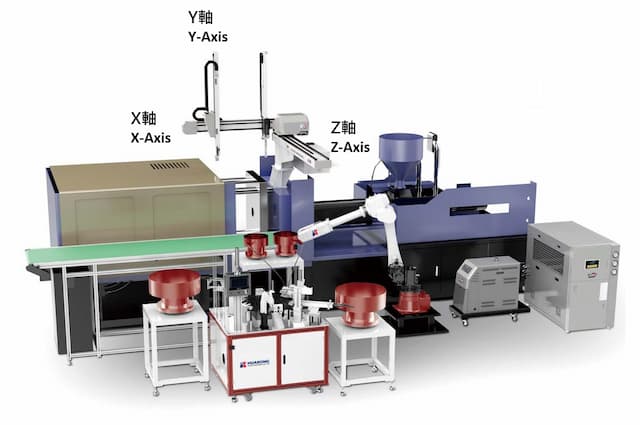
Classification Based on X-Axis Structure
Linear robots can be further classified based on the structure of the X-axis (drawing axis):
- Hanging Arm Type: Suitable for standard lightweight loads ranging from 3 to 5 kg.
- Frame Type: Designed for standard medium loads from 6 to 15 kg.
- Bullhead Type: Ideal for heavy loads from 20 to 30 kg.
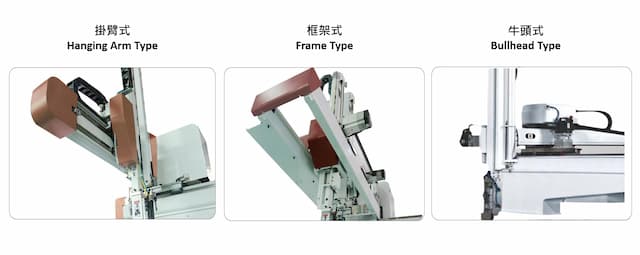
Classification Based on Arm Structure
Linear robots can also be categorized by their arm structure:
- Single Arm Single Section: A simple structure with a single arm and segment.
- Double Arm Double Section: Features a dual-arm, dual-segment design, offering advantages such as fast vertical movement, making it suitable for environments with lower ceilings. This structure can operate at twice the speed of single-arm designs.
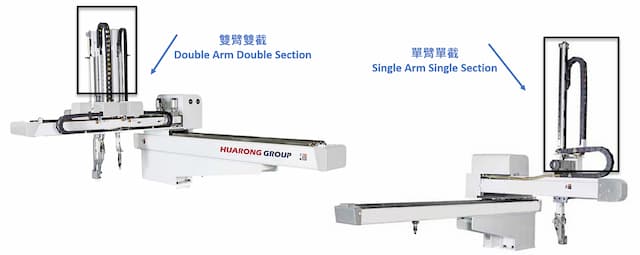
Axis-Based Classification of Robots
Linear injection molding robots are classified based on the number of directional axes they operate on. This classification method is very commonly used as it determines the robot's range of motion and application suitability:
- Three-Axis Robots: These robots operate along the X, Y, and Z axes, providing basic movement capabilities ideal for simple pick-and-place tasks.
- Four-Axis Robots: Adding an axis of rotation, these robots offer improved flexibility and are suitable for more complex operations.
- Five-Axis Robots: With enhanced dexterity, five-axis robots can perform more intricate tasks that require precise positioning and orientation.
- Six-Axis Robots: These robots provide the highest level of flexibility and control, making them suitable for complex and precise operations that demand a full range of motion.
Related product: Injection Molding Robot - Manipulator Arm
Integrating robots in injection molding offers numerous advantages that significantly enhance the efficiency and quality of manufacturing processes. Key benefits include:
- Precision and Repeatability: Injection molding robots are equipped with advanced control systems and sensors that ensure precise placement of inserts within the mold cavity and alignment of components during the injection molding process. Robots can perform the same task repeatedly with minimal variation, ensuring uniformity in mass production.
- Increased Efficiency and Speed: Robots can handle multiple tasks simultaneously, such as picking up substrates, placing them in the mold, and removing finished parts. This multitasking capability reduces cycle times and increases production throughput. Additionally, robots can operate continuously without fatigue, increasing overall efficiency and productivity.
- Enhanced Safety: Using robots in insert molding or overmolding reduces the need for manual handling of components, minimizing the risk of workplace injuries. Robots can easily operate in hazardous environments and handle heavy or delicate components, ensuring a safer working environment for human operators.
- Reduced Labor Costs: Automation decreases the reliance on manual labor, leading to cost savings in wages, training, and human resource management.
- Quality Control and Inspection: Robots can be integrated with vision systems and other quality control technologies to inspect substrates and finished parts in real-time inspection. This capability ensures that only components meeting stringent quality standards are used in production, reducing the incidence of defects and improving overall product quality.
Before embarking on automation solutions in injection molding machines, it's essential to consider several factors:
Choosing the Right Robot Type
Selecting the appropriate injection molding robot depends on several factors:
- Load Requirements: Determine the weight of the parts being handled to choose between lightweight, medium, or heavy-load robots.
- Movement Complexity: Assess the complexity of the tasks to decide between three-axis, four-axis, five-axis, or six-axis robots.
- Space Constraints: Consider the physical constraints of your facility, such as ceiling height and available floor space, when selecting the arm structure.
End-of-Arm Tooling (EOAT)
Selecting appropriate EOAT, such as mechanical grippers or suction cups, is crucial for handling plastic parts without damage and maximizing robot productivity.
Planning and Testing
Robust planning and thorough testing are indispensable in integrating robotics into injection molding operations. Fine-tuning parameters such as timing, temperature, and pressure settings ensure optimal performance and avoid potential setbacks during production ramp-up. Therefore, it is recommended that you find a professional injection molding expert to provide you with full-process automation solutions.
Injection molding robots offer numerous advantages, from enhanced efficiency to improved safety and quality. Understanding the different types of linear injection molding robots, their classifications, and their applications can help manufacturers make informed decisions and optimize their production processes. By selecting the right robot for your specific needs, you can achieve higher productivity, better quality, and greater cost savings.
Expert Integration and Support
Selecting and integrating the right robotic technology requires expertise. At Huarong, our automation department provides tailored solutions for your manufacturing needs. Contact Huarong to discuss your project and explore our past successes.
- Group Name: Huarong Group
- Brand: Huarong, Yuhdak, Nanrong
- Service Offerings: Injection Molding Machine, Vertical Injection Molding Machine, Injection Molding Automation
- Tel: +886-6-7956777
- Address: No.21-6, Zhongzhou, Chin An Vil., Xigang Dist., Tainan City 72351, Taiwan
- Official Website: https://www.huarong.com.tw/
Previous news : Case Study: Best PVC Pipe Fitting Machine for Your Business
Next news : Injection Molding Machine Specifications: What to Look For When Choosing the Right Equipment