Injection Molding Machine Specifications: What to Look For When Choosing the Right Equipment
2024-07-10 16:40:12
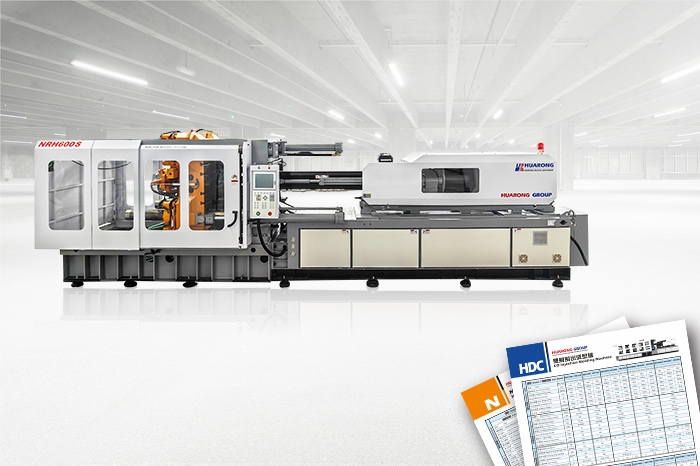
Selecting the right plastic injection molding machine is crucial for manufacturers aiming for efficiency and high-quality output. By understanding the key parameters of each injection molding machine, like injection pressure, clamping force, and cycle time, you can make an informed decision.
The specifications of injection molding machines are vital as they dictate the machine's capabilities and appropriateness for specific applications. These specifications include parameters related to the injection unit, clamping unit, power unit, and others. Each parameter has significance and impact, playing a critical role in the overall performance and efficiency of the machine.
Here’s a detailed overview of the most important specifications:
1. Injection Unit Specifications
The injection unit controls the process of injecting molten injection molding material into the mold. Important parameters are:
2. Clamping Unit Specifications
The clamping unit's primary function is to hold the mold securely during the injection and cooling process. Key parameters include:
3. Power Unit and Other Specifications
The power unit and others control the machine's movements and functions, impacting your injection machine's operational cost and environmental footprint.
The specification defines how well a machine can perform its intended functions and how efficiently it operates. Here’s why these specifications matter:
- Performance and Capability
- Machine Capacity: Specifications like clamping force, injection capacity, and shot size determine the maximum size and complexity of the parts that can be produced. Understanding these specifications helps you select a machine that meets your production needs.
- Precision and Accuracy: Details such as the machine’s tolerance, control systems, and motor specifications influence the precision and accuracy of the molded parts. Accurate specifications ensure that parts meet the required dimensions and quality standards.
- Efficiency and Cost
- Energy Efficiency: Specifications for motor power, hydraulic systems, and energy consumption impact the overall operational cost. Efficient machines use less energy and can lower production costs.
- Production Speed: Parameters such as injection speed and cycle time affect how quickly parts are produced. Faster cycle times can increase overall production efficiency and reduce lead times.
- Compatibility and Integration
- Mold Compatibility: Specifications help determine if a machine can accommodate the molds you plan to use. This includes mold size, weight, and type (e.g., multi-cavity or insert molds).
- Auxiliary Equipment: Understanding the machine’s specifications allows for proper integration with other equipment, such as robots, conveyors, and cooling systems, ensuring a seamless production of the injection molding process.
- Safety and Reliability
- Operational Safety: Proper specifications ensure that the machine operates within its designed limits, reducing the risk of accidents and equipment failure. Safety features and emergency stops are also part of these specifications.
- Maintenance and Longevity: Machines with well-defined specifications are less likely to experience unexpected breakdowns. Regular maintenance can be planned according to the machine’s operational parameters, increasing longevity.
- Investment and ROI
- Cost-Benefit Analysis: Understanding the specifications helps evaluate the machine's cost-effectiveness. It also allows for comparing different models and manufacturers to ensure the best investment.
- Future-Proofing: Choosing a machine with the right specifications can accommodate future production needs or technological changes, providing better long-term value.
Injection molding machine specifications are crucial for selecting the machine that is appropriate for your production needs. By comprehensively understanding the injection, hydraulic, clamping, power unit, and others' specifications, you can ensure that you choose a machine that meets your specific requirements, leading to efficient and cost-effective manufacturing.
Reputation Machine Manufacturer - Huarong
When investing in injection machines, in addition to the technical specifications, it is also important to consider the manufacturer's reputation and support when purchasing. As an experienced injection molding machine manufacturer, Huarong is here to help you find the perfect solution for your manufacturing requirements.
- Group Name: Huarong Group
- Brand: Huarong, Yuhdak, Nanrong
- Service Offerings: Injection Molding Machine, Vertical Injection Molding Machine, Injection Molding Automation
- Tel: +886-6-7956777
- Address: No.21-6, Zhongzhou, Chin An Vil., Xigang Dist., Tainan City 72351, Taiwan
- Official Website: https://www.huarong.com.tw/
Previous news: Comprehensive Guide to Injection Molding Robots: Automate Your Production Process