How Our Vertical Injection Machines Produce High-Quality Tubes for CPAP | Success Story
2024-08-02 14:20:47
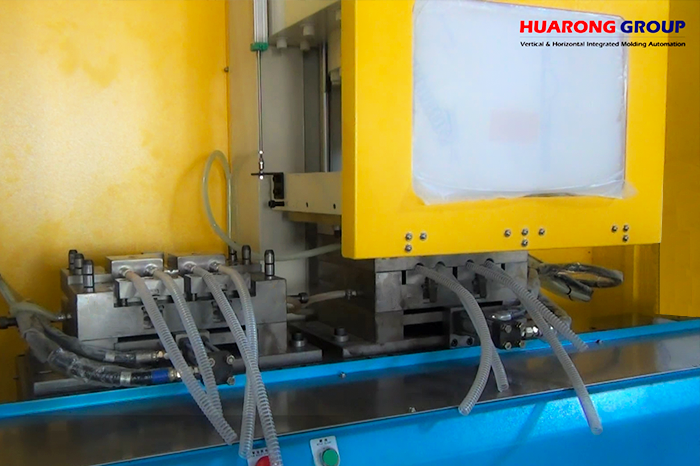
Tubes for CPAP (Continuous Positive Airway Pressure) devices are critical components in sleep apnea treatment, they need to be replaced regularly to avoid rupture after prolonged use, and producing a tube for CPAP that meets the stringent requirements of the medical industry is no easy task. At Huarong, our advanced vertical injection machines strive to deliver essential medical accessories. This case study explores how our machines have transformed CPAP tube manufacturing, meeting the growing demand for high-quality, precise, and efficient production. Read on to discover how Huarong's injection molding solutions are setting high standards in the medical device industry, particularly in the realm of CPAP therapy accessories.
The CPAP industry faces challenges in producing high-quality tubes that meet stringent medical standards while keeping pace with increasing demand. Let's explore the factors driving this need and the specific requirements for medical-grade tube production.
Rising Need for CPAP Devices and Accessories
The global prevalence of sleep apnea has led to a surge in demand for CPAP devices and their associated accessories, particularly tubes for CPAP. According to recent studies, an estimated 936 million adults worldwide suffer from sleep apnea, with many relying on CPAP therapy for treatment. This growing patient population has created a pressing need for efficient, large-scale production of CPAP tubes. Manufacturers face the challenge of producing tubes that keep up with the market demand while not compromise on quality or safety.
Quality and Efficiency Requirements in Medical-Grade Tube Production
Manufacturing tubes for CPAP devices presents unique challenges due to the stringent quality standards required for medical applications. These tubes must be:
- Biocompatible and non-toxic
- Flexible yet durable
- Resistant to bacteria growth
- Capable of withstanding regular cleaning and sterilization
Moreover, the production process must ensure consistent quality across large batches while maintaining cost-effectiveness. This delicate balance between quality, efficiency, and cost has pushed manufacturers to seek innovative solutions in injection molding technology.
At Huarong, we have the most suitable vertical injection machines for producing CPAP tubes fittings, specifically designed to handle its unique long shape and insert molding need.
Key Features of Our Vertical Injection Machine
Introduce you to our “vertical injection molding machine – YC series”, which specializes in dealing with plastic products that need to be embedded so that they can be produced.
- Vertical clamping, without machine column design, the mechanical constitutive property is strong, Injection powerfully, suit large-scale embedment to take shape the processing.
- Three-sides open space, easier operation for embedded parts and finished products, and able to combine automation connecting planning
- The height of operating surface is ergonomic, and the height of the machine is low. The operating environment can have more additional space to use.
- Diversified oil circuit design can be customized according to customer requirements.
Related product: Tie-barless Vertical Clamping Horizontal Injection Machine – YC Series
Vertical Injection Molding Technology for CPAP Tube Fitting Production
Our vertical injection machines are equipped with advanced features tailored for CPAP tube fitting manufacturing:
- Precision Control: Precise temperature and pressure controls ensure consistency in material flow and cooling, critical for maintaining the exact dimensions and properties required for CPAP tubes fittings.
- Rapid Cycle Times: Optimized heating and cooling systems significantly reduce cycle times, boosting production efficiency without compromising quality.
- Smart Factory Management: Real-time quality control measures, including autonomous detection functionality, ensure each tube for CPAP meets exact quality.
By incorporating these specialized features, our injection molding technology addresses the specific needs of CPAP tube fitting production, ensuring high-quality, consistent output that meets medical device standards.
Our team at Huarong works closely with clients to ensure a smooth transition and optimal performance of our vertical injection machines in their CPAP tube fitting production lines, leading to significant improvements in CPAP tube production across various metrics.
Increased Output of CPAP Tubes
Our clients have reported substantial increases in production capacity, now they have the ability to meet sudden spikes in demand without compromising quality. This boost in productivity has allowed manufacturers to better meet the growing global demand for CPAP accessories, positioning them as reliable suppliers in the competitive medical device market.
Enhanced Precision and Consistency in Tube Manufacturing
Quality improvements have been equally impressive, not only defect rates reduced, consistent wall thickness and durability across batches, but also improved longevity of CPAP tube fittings. These quality enhancements not only ensure regulatory compliance but also contribute to improved patient satisfaction.
Cost Savings and ROI for Our Customer
The economic benefits of implementing our injection molding technology can be seen, including reduced energy consumption, decrease material waste. Many of our customers find they soon achieving full return on investment, with ongoing savings contributing to improved profitability in their CPAP tube production lines.
CPAP Tube Fitting Production Video
Plastic Part | CPAP Tube Fitting
Machine Model | YC-90-2S
Industry | Medical Industry
Don't just take our word for it. Here's what one of our valued customers, a leading manufacturer of CPAP accessories, had to say about their experience with Huarong's injection molding machines:
This testimonial underscores the real-world impact of our technology on CPAP tube manufacturing, highlighting the multifaceted benefits experienced by our clients.
Huarong's advanced vertical injection machines have proven to be a great partner for your injection molding business, offering unparalleled precision, efficiency, and customization options. As the demand for CPAP therapy continues to grow, manufacturers equipped with our technology are well-positioned to meet this challenge head-on, delivering superior products while optimizing their operations.
Are you ready to revolutionize your CPAP tube production and gain a competitive edge in the medical device market? Contact Huarong today for a personalized consultation and discover how our cutting-edge injection molding solutions can transform your manufacturing process.
- Group Name: Huarong Group
- Brand: Huarong, Yuhdak, Nanrong
- Service Offerings: Injection Molding Machine, Vertical Injection Molding Machine, Injection Molding Automation
- Tel: +886-6-7956777
- Address: No.21-6, Zhongzhou, Chin An Vil., Xigang Dist., Tainan City 72351, Taiwan
- Official Website: https://www.huarong.com.tw/
Previous news : Controller Specification of Injection Molding Machine PLC Controller
Next news : Guide to Running Huarong Injection Molding Machine Manual Operations