物理微發泡射出成型:實現最大化的減重與尺寸穩定性
2024-11-13 11:29:57
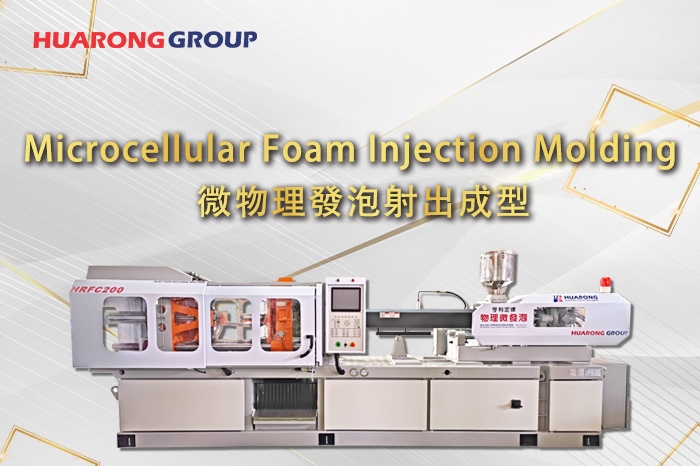
在當今迅速發展的製造環境中,對於永續發展與長期成長的關注比以往任何時候都更加強烈,環境、社會和治理(ESG)的考量正推動創新。減少塑膠材料的使用不僅是一種節約成本的措施,更是企業在這個注重環保的未來中,追求長遠成功的關鍵策略之一。微物理發泡射出成型提供一個先進的解決方案,使製造商能夠在保持或提升產品強度與性能的同時,減少材料的使用。
微物理發泡射出成型是將氣體(例如氮氣或二氧化碳)在高壓下引入聚合物熔體中,氣體均勻溶解於材料中,形成過飽和的聚合物-氣體混合物。當材料被射入模具時,壓力急劇下降,氣體膨脹並在聚合物內形成微小的氣泡。這個可控的發泡過程使最終產品在保持機械完整性的同時,達到降低密度的效果。
延伸閱讀:微物理發泡射出成型技術
微物理發泡射出成型的核心特點
由於該技術在聚合物內形成微細氣泡,與傳統射出成型相比,它具有幾個主要特點:
- 重量與密度降低(輕量化零件):主要優勢是能在不影響機械強度的情況下,使重量降低15%-20%。
- 降低材料成本:透過減少每個零件所需的塑膠量,製造商可以大幅節省原料成本。
- 尺寸穩定性:引入微氣泡後,產品具有出色的尺寸穩定性。
- 縮短生產週期:產品的均勻氣泡結構取消保壓階段,縮短生產時間,加快生產週期。
- 環保效益(永續性與回收):此過程透過減少材料用量和縮短生產週期降低能源消耗,較傳統成型工藝更環保。此外與化學發泡方法不同,微物理發泡屬於物理發泡,不會留下有害殘留物,因此產品更環保且適合回收再利用。
- 降低鎖模力需求:發泡過程使得所需的鎖模力低於傳統射出成型,允許製造商在較小的機台上生產較大的零件,進一步降低成本。
- 提升製程效率:由於生產週期縮短、材料節省以及能使用較小噸位機台,微物理發泡射出成型大幅提升生產效率與產能。
- 減少模具磨損:微物理發泡的低內壓減少模具磨損,延長模具的使用壽命,使得每次生產的運行時間更長,降低翻新或更換模具的頻率。
微物理發泡射出成型與傳統射出成型的流程相似,但引進額外的步驟來提高產品性能,特別是在減重與材料效率方面。以下是微物理發泡成型與傳統方法的比較,並重點介紹該技術的特有要素:
傳統射出成型的延伸閱讀:塑膠射出成型流程為何?射出機製程的6個步驟
步驟 1:鎖模
該過程始於鎖模,模具的兩半藉由鎖模單元緊緊合在一起,以確保在射出階段模具保持閉合。與傳統射出成型的不同之處在於,微物理發泡成型所需的鎖模力遠低於傳統方法,這是由於發泡作用減少內部壓力,進一步節約能源,並且允許在較小的機台上生產較大的零件,從而降低生產成本。
步驟 2:氣體溶解的注射
在傳統射出成型中,塑膠顆粒或膠粒會在高壓下融化並注入模腔,而微物理發泡射出成型則會在注射階段向熔融塑膠中引入超臨界氣體,如氮氣或二氧化碳。這個過程稱為氣體溶解,氣體均勻地溶解於聚合物熔體中,降低材料的密度,從而製造出輕量但堅固的零件。
步驟 3:成核與取消保壓
在傳統射出成型中,保壓階段至關重要,對模具內的空間繼續加壓,用來維持模具中的壓力,確保模具腔體均勻填充並防止材料回流。由於需要持續的壓力來保持保壓,這一階段通常會導致生產週期延長並增加能源消耗。然而在微細孔泡沫注塑過程中,材料內部均勻微泡的形成消除保壓階段的需求,因此不再需要持續加壓來填補模具腔體中的空隙,這減少能源密集型步驟的改進,有助於在射出成型過程中降低能源消耗。
步驟 4:冷卻與氣泡成長
當塑膠注入模腔後,塑膠開始冷卻。微物理發泡射出成型中,形成的氣泡在冷卻時會均勻膨脹,從而降低零件的整體密度,並保持結構完整性。由於氣泡的存在,冷卻時間可能會比傳統成型略短,進一步提升生產效率。
步驟 5:開模
塑膠冷卻並固化後,模具會如同傳統成型一樣打開,鎖模單元鬆開,模具分離,展示新成型的零件。微物理發泡零件密度較低,與傳統實心零件相比,材料收縮較少,從而達到更好的尺寸穩定性,並減少成型後的缺陷。
步驟 6:頂出
在最後一步中,固化的零件從模腔中頂出,這一過程與傳統製程類似,頂出針會將零件從模具中推出。不同的是,微物理發泡零件由於材料密度降低且具有發泡特性,通常需要的頂出力較小,使頂出過程更加順暢,缺陷較少。儘管仍可能需要修剪多餘材料,但由於其原材料利用效率高,微物理發泡零件的材料浪費通常較少。
微物理發泡射出成型的效率依賴於幾個關鍵組件:
- 氣體供應(氮氣或二氧化碳):氣體供應是創造微胞結構的重要組件,通常使用氮氣或二氧化碳等惰性氣體。
- 氣體驅動源:這個組件能夠以控制壓力精確地將氣體注入聚合物熔體,確保在塑化階段內氣體均勻且穩定地溶解於聚合物中,從而形成均勻的微胞結構。
- 專用微物理發泡料管組與止逆射嘴:此專門設計的料管組針對微物理發泡工藝進行優化,改善氣體在聚合物中的混合與分散。指逆射嘴是關鍵組件,防止氣體在射出過程中過早逃逸,確保發泡的完整性。這些專業設備可控制聚合物與氣體混合物在射入模具時的膨脹,確保零件內部的泡孔結構均勻且穩定。
物理發泡射出成型具有高度的靈活性,廣泛應用於各個行業,包括:
- 汽車產業:微物理發泡射出成型適合生產輕量化且高性能的內飾件到引擎零組件,因為減輕零件重量能直接提升燃油效率。
- 消費品產業:這種材料常用於消費電子產品中,用來製造像是智慧手機、筆記型電腦、平板電腦等設備的輕量化且堅固的外殼。它出色的尺寸穩定性確保零件完美契合,而輕量特性則提升這些設備的便攜性。
- 包裝行業:通過減少每個包裝所需的塑膠量,製造商能降低成本並生產具備環保特性的包裝解決方案,同時不犧牲品質。
除微物理發泡成型外,還有哪些其他的發泡射出成型方式?
發泡射出成型可以根據在聚合物內產生泡沫的方式進行分類,主要分為三種方法:物理發泡、化學發泡和結構發泡。本文討論的微物理發泡成型屬於物理發泡,而其他方法也廣泛應用。
項目 | 物理發泡 | 化學發泡 | 結構發泡成型 |
---|---|---|---|
過程 | 將惰性氣體或低沸點液體溶解於聚合物熔體中形成泡沫 | 化學發泡劑在加熱時分解,釋放氣體產生泡沫 | 同時使用物理或化學發泡劑來形成微胞結構 |
機械強度 | 中等;依賴氣體分布的均勻性 | 適合複雜形狀;強度依泡沫密度而異 | 高;結合發泡與厚壁結構,提高整體耐用性 |
使用範圍(應用) | 輕量化汽車零件、包裝、保溫材料 | 複雜消費品、保溫材料、電子產品 | 大型零件,如面板、汽車、重工業建築產品 |
優點 | 輕量化,氣泡均勻,材料使用量低 | 適合複雜設計,高密度潛力 | 適合大型複雜結構,模具成本低,可使用多腔模具 |
缺點 | 需要精確控制壓力與氣體 | 發泡劑殘留可能影響質量 | 生產週期較長,小批量生產成本較高,適合小批量 |
微物理發泡射出成型無疑是未來輕量化與高強度製造技術的發展趨勢。它具有減少材料使用、縮短生產週期和提升尺寸穩定性等多重優勢,將徹底改變多個行業。
聯繫我們
欲解更多關於我們的微物理發泡射出成型技術如何助您下一個專案成功,華嶸機械作為一家專業的射出成型機製造商,不僅提供全系列射出成型機,還為客戶提供可行的解決方案,攜手共創未來
- 集團名稱: 華嶸集團
- 品牌: 華嶸、煜達、南嶸
- 服務項目: 射出成型機、立式射出機、成型設備取出裝置
- 服務電話: (06)7956777
- 集團總部: 台南市西港區慶安里中州21之6號
- 官方網站: https://www.huarong.com.tw/
前一則新聞:華嶸榮獲2025年台灣精品獎,展現創新射出成型技術
下一則新聞:PET瓶胚注塑成型機:實現高產能與高效率的製造