PVC射出成型:工藝、挑戰與最佳實踐
2025-02-27 15:22:01
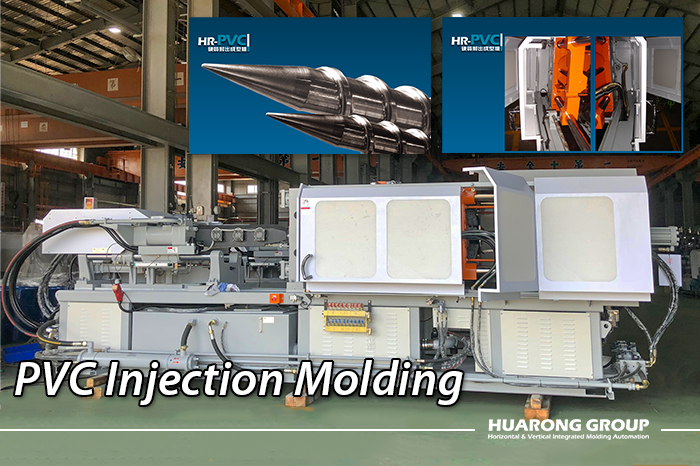
PVC射出成型是一種廣泛應用的製造工藝,能夠以卓越的精度生產高品質、耐用的塑膠零件。PVC因其多功能性、成本效益及化學抗性而受到青睞。然而,與其他塑膠相比,PVC的加工需要特殊技術及嚴格控制,以確保產品品質、機械壽命及安全性。本文將深入探討PVC射出成型,包括材料特性、成型工藝、設計準則及最佳實踐。
PVC(聚氯乙烯)是一種合成熱塑性聚合物,主要分為剛性PVC(RPVC)和軟性PVC(FPVC)兩種形式。PVC由氯乙烯單體(VCM)、增塑劑、穩定劑及其他添加劑組成,這些成分影響其機械及熱性能。與其他塑膠不同,PVC因其低熱穩定性及潛在的降解風險,需要嚴格的加工控制。
PVC類型:
- 剛性PVC(RPVC):以其硬度和強度著稱,廣泛應用於建築材料,如管材和窗框。
- 軟性PVC(FPVC):添加增塑劑後,材料變得更柔軟且具可塑性,常用於醫療管材、電纜絕緣層及各類消費品。
延伸閱讀:10 個常見射出成型塑料及其特性
PVC的關鍵特性
PVC的普及歸因於其多種優異特性:
- 化學抗性:對酸、鹼及大多數有機溶劑具有優異的抗性,非常適合化學處理應用。
- 電絕緣性:具備優異的絕緣特性,被廣泛應用於電子與電氣領域。
- 阻燃性:天然具有耐燃性且自熄特性,可提升防火應用的安全性。
- 耐久性:擁有高抗拉強度與抗衝擊性,確保在嚴苛環境中的使用壽命。
- 低吸濕性:即使在潮濕環境中,也能保持尺寸穩定及機械性能。
材料性能比較
性質 | 剛性PVC(RPVC) | 軟性PVC(FPVC) |
---|---|---|
密度(g/cm³) | 1.35 - 1.45 | 1.1 - 1.3 |
拉伸強度(MPa) | 45 - 60 | 10 - 25 |
斷裂伸長率(%) | 10 - 40 | 100 - 400 |
彎曲模量(GPa) | 2.4 - 4.1 | 0.01 - 0.1 |
介電常數 | 3.0 - 3.8 | 3.2 - 4.0 |
(註:具體數值可能因PVC配方及添加劑不同而有所變化。)
PVC射出成型應用領域
PVC射出成型廣泛應用於各行業,包括:
- 建築:生產耐用且耐候的管材、接頭及外牆覆層材料。
- 醫療:製造具有生物相容性和可消毒性的軟管、點滴袋及其他醫療器材。
- 汽車:用於內飾件、儀表板及密封條,因PVC的美觀性及耐用性而受到青睞。
- 消費品:用於製造鞋類、玩具及各類家用產品,具有成本效益及多用途性。
相關文章:成功案例:最適合您的PVC塑膠管件射出機
PVC射出成型過程遵循一系列關鍵步驟,確保將原料轉化為精確且一致的成品。
1. 材料準備
PVC樹脂需與穩定劑、增塑劑及潤滑劑混合,以改善流動性及熱穩定性。預乾燥(60°C 2-3小時)可防止因水分引起的氣泡或燒焦痕跡。
2. 熔融與塑化
PVC的加工溫度範圍較窄,過熱會導致降解。維持熔融溫度在170°C至190°C 之間,可確保流動性而不降解。
3. 射出
當PVC熔融後,在受控的壓力及速度下注入模具腔內。精確控制可確保無空洞填充,並最小化殘餘應力。
4. 冷卻
冷卻過程至關重要,以防止變形及收縮。高效的模具冷卻系統可確保均勻冷卻並保持尺寸穩定。
5. 脫模
冷卻後,固化的PVC零件從模具中取出。可使用防黏塗層或脫模劑,以防止粘附問題。
參數 | 建議設定 |
---|---|
熔融溫度 | 170°C – 190°C |
射出壓力 | 80 – 120 MPa (800 – 1200 bar) |
射出速度 | 中等至高速 |
模具溫度 | 20°C – 50°C |
冷卻時間 | 20 – 70秒 |
儘管PVC具有出色的多功能性,但對其進行成型需要特殊的考慮。以下是一些常見的挑戰:
1. 熱敏感性
PVC在高溫下會分解,釋放鹽酸(HCl),可能腐蝕機械元件並影響成品品質。防止降解的方法包括:
- 維持加工溫度在 170°C至190°C。
- 使用溫控料筒並避免過長的停留時間。
2. 高黏度
PVC熔融後的黏度較高,填充模具較困難。解決方案:
- 使用 80 – 120 MPa 的射出壓力。
- 確保模具設計具有足夠的排氣孔。
3. 腐蝕問題
PVC會釋放酸性氣體,導致模具及機械元件腐蝕。建議:
- 使用 不鏽鋼或鍍鉻模具。
- 定期維護及潤滑機械部件。
4. 吸濕性
水分可能導致成品產生氣泡或空洞。解決方案:
- 預乾燥 PVC樹脂(60°C 2-3小時)。
設計PVC射出成型產品時,需要考量多個因素,以提升可製造性與產品性能:
- 均勻壁厚:保持一致的壁厚可減少內部應力,降低變形及縮痕風險。
- 脫模斜角設計適當的脫模角度(通常1° 至 2°),可幫助零件順利脫模,減少模具損耗與生產困難。
- 圓角處理:避免尖銳直角,適當添加圓角(R角)可減少應力集中,並改善材料流動性,提高產品品質。
- 孔洞設計:確保孔洞的深徑比不超過2:1,以防止射出成型時產生缺陷,並保持零件的結構完整性。
模具設計對PVC射出成型零件的品質具有關鍵影響:
- 材料選擇:應使用耐腐蝕材料(如 H13、S136 不鏽鋼或鍍鉻鋼),以延長模具壽命並減少腐蝕問題。
- 冷卻通道:應設計 符合模具形狀的冷卻通道(Conformal Cooling),以確保均勻冷卻並提升生產效率。
- 通氣設計:適當的 排氣設計 能有效防止氣體滯留,降低燒焦痕跡或氣泡等缺陷的發生率。
遵循業界最佳實踐可提升生產效率及產品品質:
1. 材料處理與準備
- 適當存放PVC樹脂,防止污染或受潮。
- 成型前預乾燥(60°C 2-3小時),以降低水分影響,提高成品一致性。
2. 機械選擇與維護
推薦產品:PVC射出機 – PVC系列
3. 優化加工參數
- 背壓:維持在 3-10 bar(50-150 psi),確保塑化均勻,防止材料降解。
- 螺桿轉:建議設定 20-60 RPM,確保均勻熔融,避免過度剪切加熱。
了解可能出現的缺陷及相應解決方案,有助於提升成品品質:
1. 燒焦痕跡
- 成因:射出速度過快或氣體滯留,導致「柴油效應」(Diesel Effect)產生高溫燃燒痕跡。
- 解決方案:
- 降低射出速度
- 優化模具排氣設計,確保氣體順利排出
2. 變形
- 成因:冷卻不均勻或壁厚不一致,導致材料內應力分佈不均。
- 解決方案:
- 設計均勻壁厚的零件,降低內應力
- 優化冷卻通道配置,提高冷卻效率
3. 變色
- 成因:熔融溫度過高或材料在料筒內停留時間過長,導致熱降解。
- 解決方案:
- 適當降低料筒溫度
- 減少材料在料筒內的停留時間
PVC射出成型是一項技術複雜但具有高回報的製造工藝,在塑膠零件生產中扮演關鍵角色。透過深入理解材料特性、嚴格控制加工參數,並遵循最佳模具設計及機械維護實踐,製造商可顯著提高產品品質及生產效率,確保在市場競爭中保持優勢。
- 集團名稱: 華嶸集團
- 品牌: 華嶸、煜達、南嶸
- 服務項目: 射出成型機、立式射出機、成型設備取出裝置
- 服務電話: (06)7956777
- 集團總部: 台南市西港區慶安里中州21之6號
- 官方網站: https://www.huarong.com.tw/